Aluminum arc welding rods have become integral in modern manufacturing and construction due to their versatility and strength. Understanding their unique properties and how to use them effectively can significantly enhance the quality and reliability of metallurgical projects.
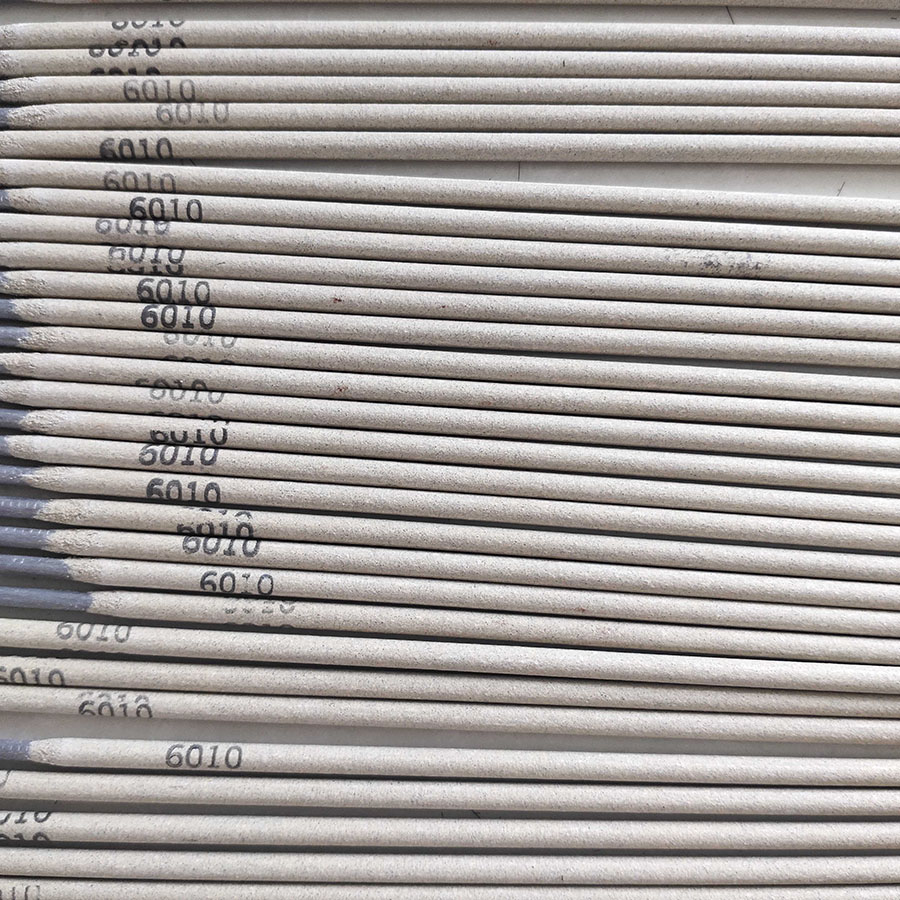
Aluminum, known for its inherent corrosion resistance and lightweight properties, is a popular material across various industries, from automotive to aerospace. However, welding aluminum presents specific challenges different from welding steel. This is where aluminum arc welding rods come into play, offering solutions to these challenges by providing robust and consistent welds.
Expert welders recognize the importance of selecting the right arc welding rod for the job. Aluminum welding rods are designed to combat the issues of distortion and burn-through associated with aluminum welding due to its conductivity and low melting point. Industry experts suggest ER4043 and ER5356 series rods as the most common choices. The ER4043 is primarily used for its ease of operation and its ability to produce quality welds, especially in automotive and shipbuilding applications. This rod is known for creating a softer, more ductile weld, which is essential for applications that may require forming post-welding.
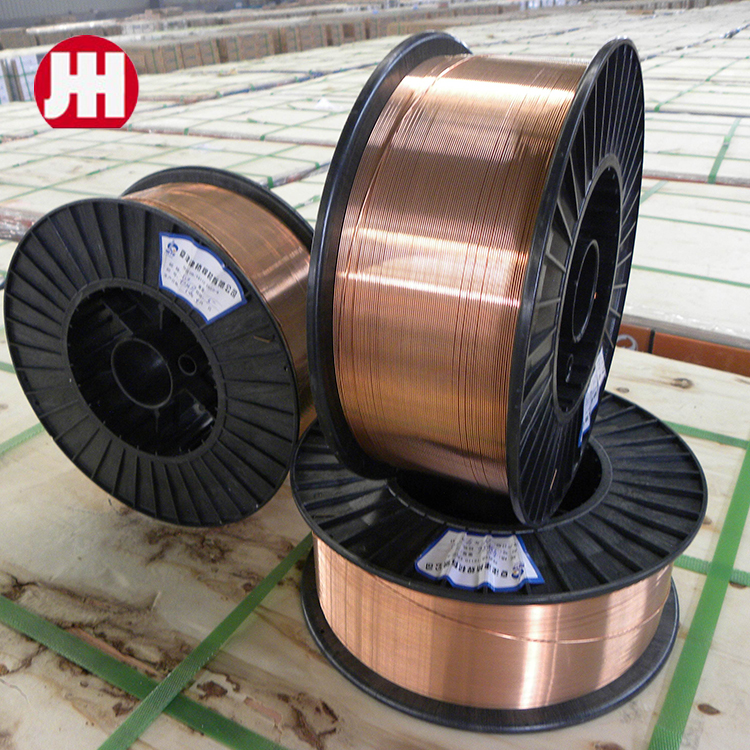
ER5356, on the other hand, is favored for its higher strength. It contains more magnesium, making it suitable for welding on higher strength alloys. It's commonly used in applications requiring a sturdier weld and is preferred for marine structures and storage tanks that demand resistance to saltwater corrosion.
One of the pivotal factors contributing to a successful aluminum welding process is the cleanliness of the welding surface.
Aluminum forms a natural oxide layer that can impede the welding process. Therefore, thorough cleaning with a wire brush or dedicated chemical cleaner is recommended before any welding begins. Additionally, controlling the welding environment by reducing drafts or using a suitable welding blanket can help prevent weld contamination and ensure a higher quality weld.
aluminum arc welding rod
Furthermore, achieving the perfect weld requires understanding the thermal conductivity of aluminum, which is five to six times higher than that of steel. This means preheating can be beneficial to ensure the weld pool is adequately controlled, averting the risk of heat distortion. Preheating also aids in minimizing the risk of cracking due to thermal shock.
Advancements in technology have also enhanced the usability of aluminum arc welding rods. Today, many rods are engineered to provide improved feedability and arc stability, resulting in smoother welds with minimal spatter. This not only improves the aesthetics of the weld but also its structural integrity, granting greater confidence in the final product.
For professionals, relying on trusted manufacturers for aluminum arc welding rods is crucial. Quality assurance certifications and adherence to standards play vital roles in ensuring that the welding rods are reliable and perform optimally under specified conditions. Additionally, consulting product datasheets can provide valuable insights into the rod’s compatibility with specific aluminum alloys and recommended operating conditions.
Lastly, ongoing training and staying informed about the latest welding techniques and products can significantly impact the efficiency and outcome of aluminum welding projects. Joining welding forums, participating in workshops, and reading industry publications are excellent ways to stay updated and refine skills.
In summary, aluminum arc welding rods are indispensable for achieving high-quality, durable welds. By selecting the appropriate rod, maintaining rigorous cleaning protocols, and leveraging modern welding technology, professionals can enhance their project outcomes and ensure the superior performance of their aluminum weldments. This expertise is essential in asserting authority and trustworthiness in the competitive fields that rely on precision welding techniques.