Choosing the best welding wire is crucial for any welding project, and the right selection can significantly impact the quality, strength, and durability of the finished work. With various options available on the market, making an informed decision requires understanding the nuances of welding wires, from their composition to their applications.
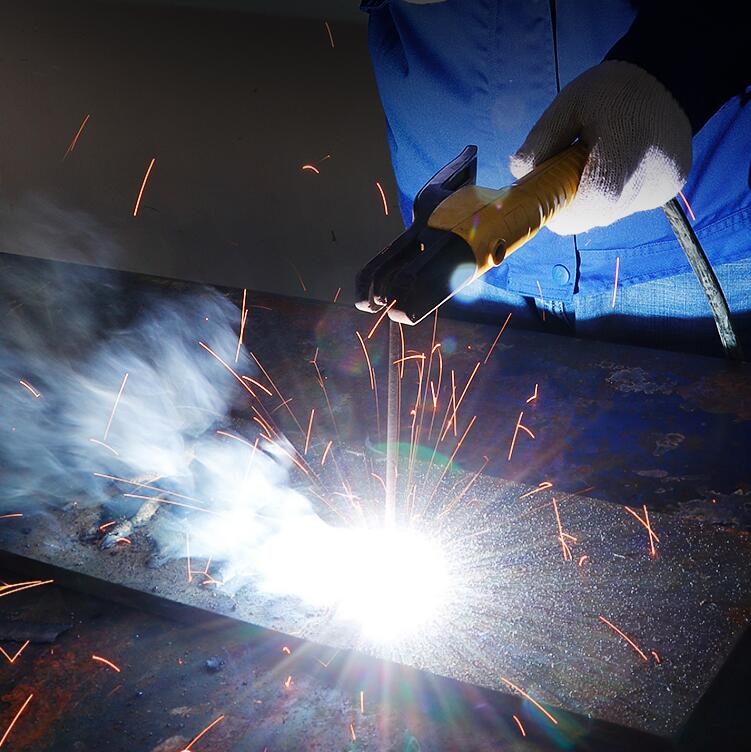
When discussing high-tier welding wire, the realm of material science cannot be overlooked. Welding wires come in several types, primarily defined by the materials they are made from, which include steel, stainless steel, and aluminum alloys. For example, if your project involves automotive repairs or construction, mild steel wires such as ER70S-6 are frequently recommended due to their compatibility with various welding processes and affordability. Their copper coating not only promotes excellent electrical conductivity but also enhances the longevity of the wire itself by reducing rust formation.
In contrast, stainless steel wires like ER308L are preferred in projects requiring resistance against corrosion and high temperatures, often used in the food processing and chemical industries. These wires produce superior welds with chromium-nickel content, making them suitable for a clean, aesthetic finish. Most importantly,
selecting the right wire diameter is essential. Thicker materials require larger diameters for proper penetration and, consequently, stronger welds.
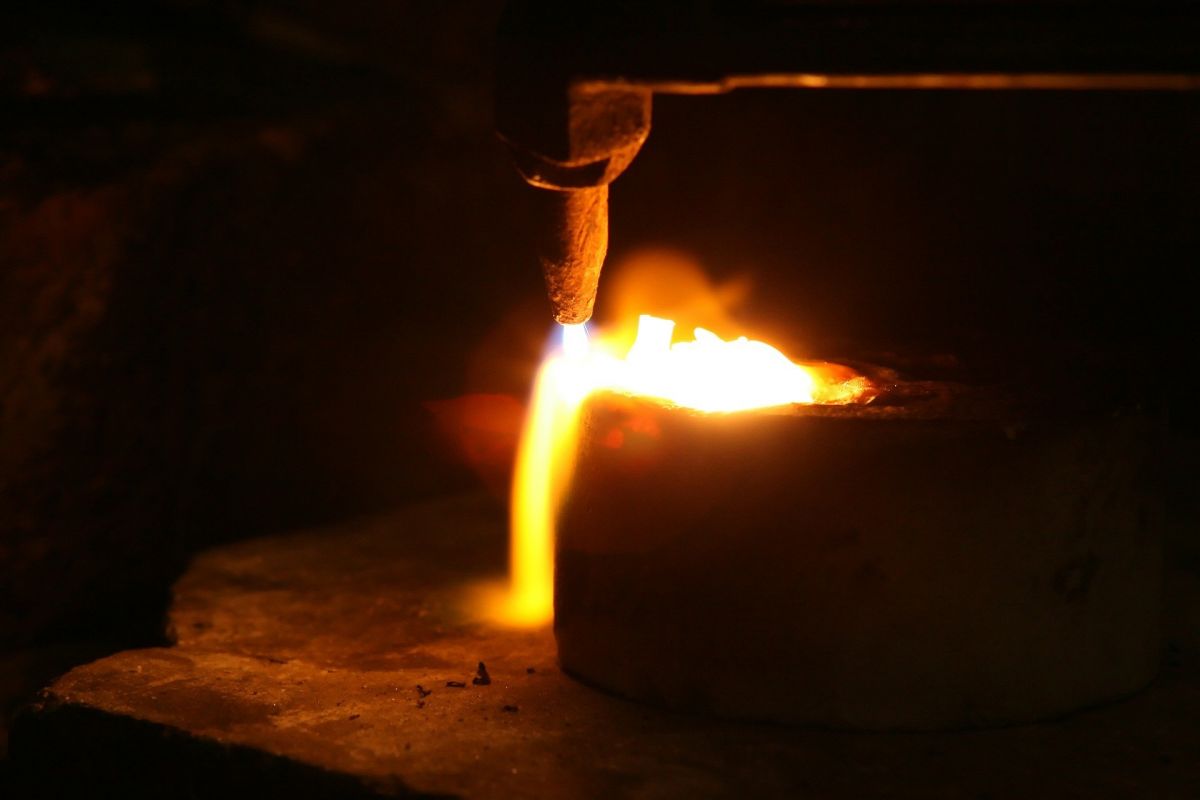
Aluminum welding wires, such as ER4043, cater to the aerospace and automotive sectors where lightweight yet strong joinery is paramount. Their usage necessitates meticulous surface preparation and specialized welding techniques. Skill in handling these wires ensures minimized distortion and porosity, which are common challenges faced when working with aluminum.
The nuances of selecting the best welding wire extend beyond just materials and include manufacturer credibility and industry standards. Opting for wires from reputable manufacturers with ISO certifications ensures that you're using supplies that meet rigorous quality checks and have consistent performance metrics. Conducting proper due diligence, through either peer reviews or expert endorsements, adds an additional layer of certainty and confidence to any welding project.
best welding wire
Another factor to consider is the specific welding process that aligns with your chosen wire. MIG welding, for instance, favors solid wires due to simplicity and speed. Flux-core wires, on the other hand, offer advantages in outdoor settings due to their gas-shield coverage but can introduce additional variables in terms of cleanliness and fume production. Understanding these detailed distinctions between processes and wire choices can lead to optimal project outputs.
Trust in the equipment and materials plays a vital role, underlining the importance of technical support and after-sales services. Industry leaders offer robust customer support services, helping troubleshoot and provide solutions for any arising issues during the welding process. This is a crucial component that assures project success from start to finish.
Real-world experience also elevates understanding and application. Engaging with welding forums, attending workshops, and seeking mentorship can provide invaluable insights and practical tips that aren't available through mere theoretical study. Alongside product knowledge, the finesse of a welding task is honed by hands-on practice and continuous learning. Unique challenges encountered during actual projects often lead to innovative strategies, maximizing both resource efficiency and technical outcomes.
Lastly, one must not overlook the environmental considerations associated with modern-day welding practices. Selecting wires that minimize environmental impact, offer recyclability, or reduce harmful emissions is becoming an industry standard rather than an option. The rising awareness and response to environmental impact ensure that welding practices contribute positively to sustainable development goals.
In conclusion, the journey to choosing the best welding wire is a blend of technical knowledge, practical experience, and a keen understanding of industry standards. Expertise in this field ensures that welders produce the highest quality joints, compete effectively in their craft, and remain adaptable to the evolving landscape of materials technology. When all factors are meticulously considered, from materials to expertise, the welding wire becomes more than just a component—it transforms into a cornerstone of excellent craftsmanship.