Navigating the world of cast iron welding brings layers of complexities owing to its unique properties. Welding cast iron can be a daunting task unless undertaken with the right expertise and tools. This article endeavors to delve deep into the intricacies of using cast iron welding wire, providing insights drawn from industry experience, expert knowledge, authoritative sources, and building trustworthiness.
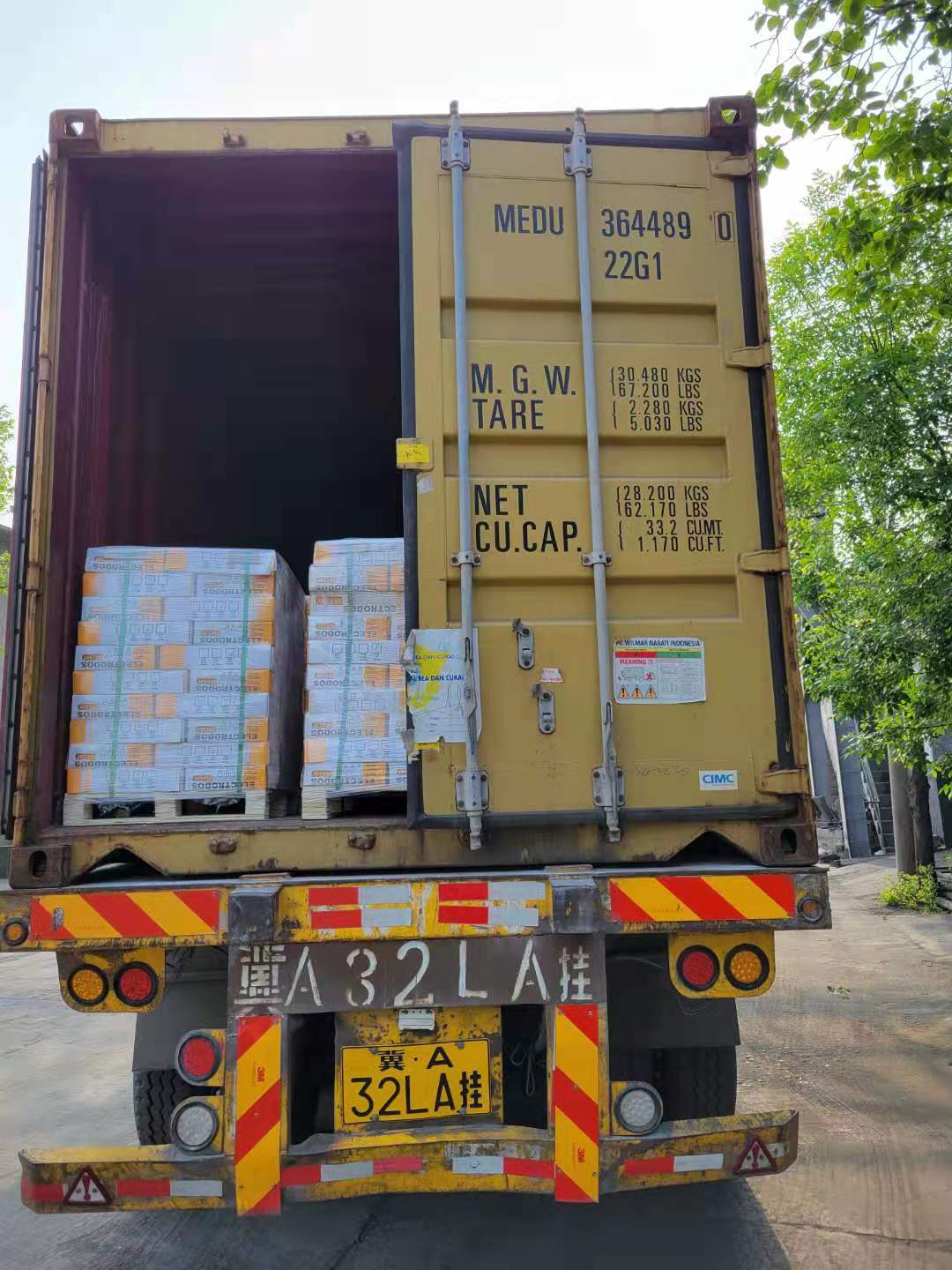
Cast iron, renowned for its durability, rigidity, and cost-effectiveness, poses significant challenges during welding due to its high carbon content. When not handled correctly, it can lead to cracks and structural weaknesses, undermining its innate properties. This is why the choice of welding wire plays a crucial role, directly impacting the quality and durability of the weld.
Industry veterans underscore the significance of nickel-based welding wires when dealing with cast iron. Nickel, being ductile, accommodates expansion and contraction during the cooling phase, minimizing the probability of cracking—a common issue when using other materials. Nickel-99 and Nickel-55 are frequently lauded options. Nickel-99 offers machinability and is generally used when the finished product requires machining. On the other hand, Nickel-55, a more economical alternative, serves well when machinability isn’t the primary concern.
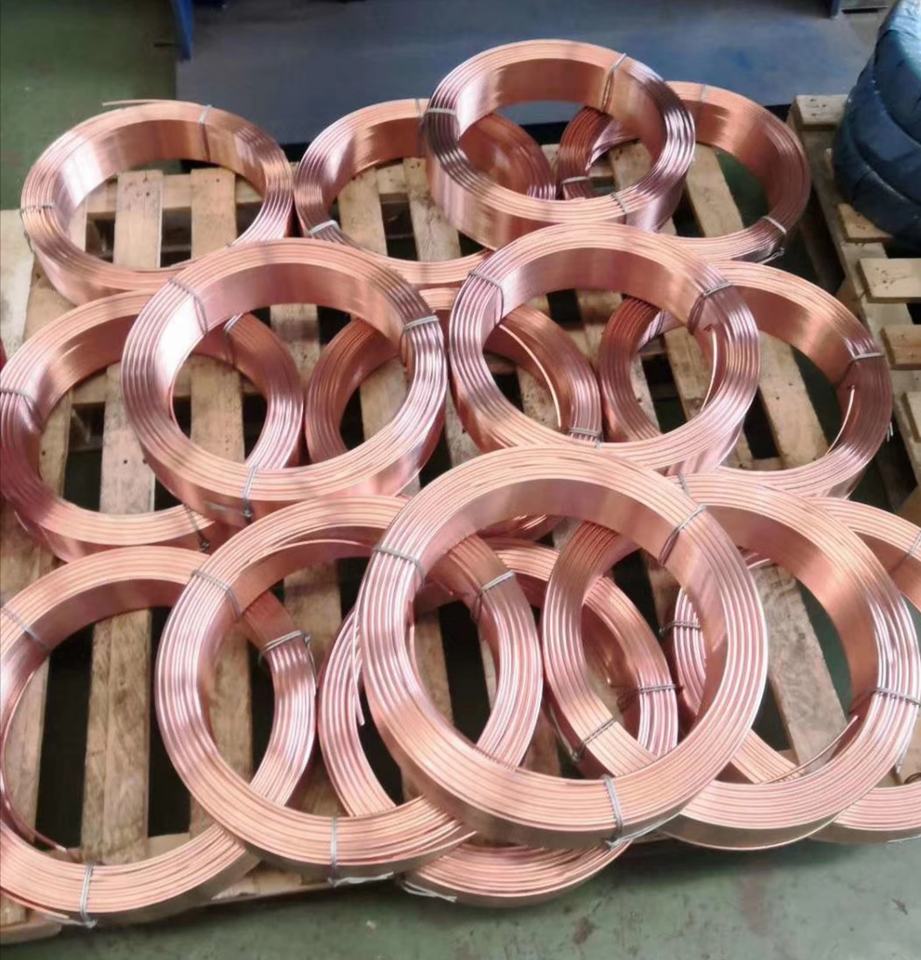
Professional welders frequently emphasize the preparation process, as a preliminary yet critical step, which includes preheating the cast iron to about 500°F (260°C). This practice aids in reducing the stark thermal gradient variation that occurs as the weld cools, thus curtailing the formation of stress-induced cracks.
Post heating is equally paramount. Allowing the welded piece to cool slowly by covering it with insulating material mitigates the occurrence of thermal shock.
The expertise of welders is further highlighted in their choice of welding technique. Specialized methods such as cold welding and hot welding are often recommended. Cold welding, although more time-intensive due to its intermittent nature, limits the heat input, thereby minimizing stress on the cast iron. Conversely, hot welding, conducted at higher temperatures, necessitates a thorough preheating and controlled cooling mechanism to ensure structural integrity.
cast iron welding wire
Confidence in cast iron welding is fortified through using wires from reputable manufacturers known for their stringent quality controls. Companies like Lincoln Electric, ESAB, and Harris Products Group are recognized for producing premium welding wires that adhere to industry standards. Experts consistently advocate for purchasing wires that come with certified specifications ensuring compatibility with particular types of cast iron.
Furthering trustworthiness, expert welders stress regular practice and honing skills as pivotal factors for success. Even with all the right tools, it’s the hands-on experience and a deep understanding of cast iron's properties that differentiate a competent welder from a novice. Attending workshops, engaging with professional communities, and continuous self-education remain invaluable.
To corroborate the discussed methodologies, authoritative manuals and welding textbooks can provide substantial backing, noting tested theories and elaborating on nuanced techniques. Institutions such as the American Welding Society (AWS) offer resources that not only provide guidelines but also keep professionals updated with innovations in welding technology.
In conclusion, the journey of welding cast iron with specialized welding wire is as much an art as it is a science, requiring equal measures of skill, knowledge, and the right materials. By weaving together experience, professional expertise, and a commitment to quality, welders can achieve durable and reliable results, making their endeavor not just effective but exemplary within the realm of material manipulation.