Gasless MIG welding wire, especially when discussing stainless steel variants like 304, is revolutionizing the welding landscape. Imagine a world where welding doesn’t require gas tanks, regulators, or hoses, dramatically simplifying the process for hobbyists and professionals alike.
Such is the promise and potential of gasless MIG welding wire.
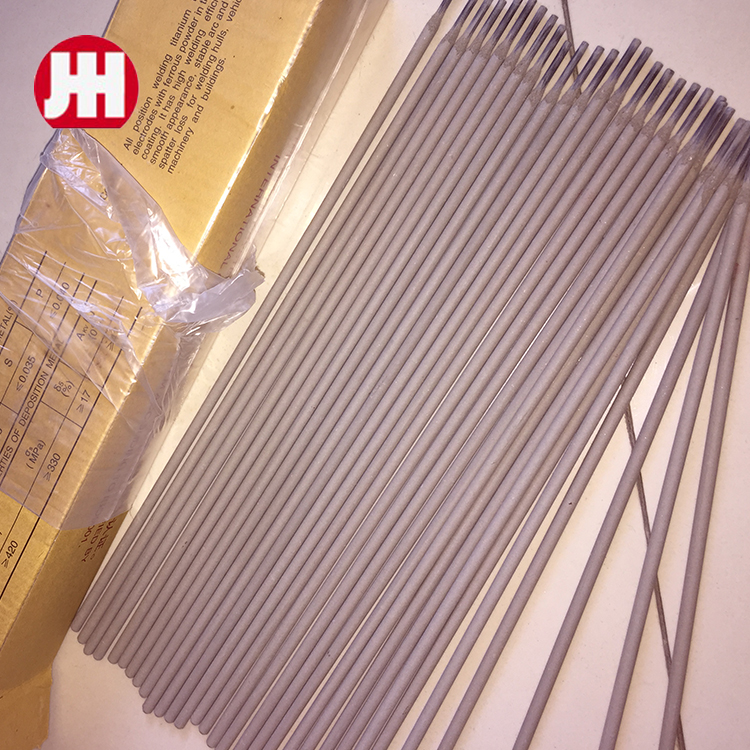
Traditionally, MIG welding involved the shielding of the arc and the molten weld pool using inert gases like argon or CO2—a necessity that added complexity and cost to welding setups. However, for some time, the advent of self-shielding flux-cored wires has been offering welders an alternative that eliminates the need for external gas. The critical advantage of gasless MIG wire is its all-in-one design. The wire consists of an outer layer of metal with a flux at the core that vaporizes during welding, creating a protective gas around the weld pool.
For stainless steel enthusiasts, 304 stainless steel wire is a standard bearer for utilities requiring rust and corrosion resistance in high-moisture environments, such as marine fittings and kitchenware. When combined with the advancements of gasless MIG welding technology, 304 promises durability without the additional hassle or expense associated with gas bottles and their maintenance.
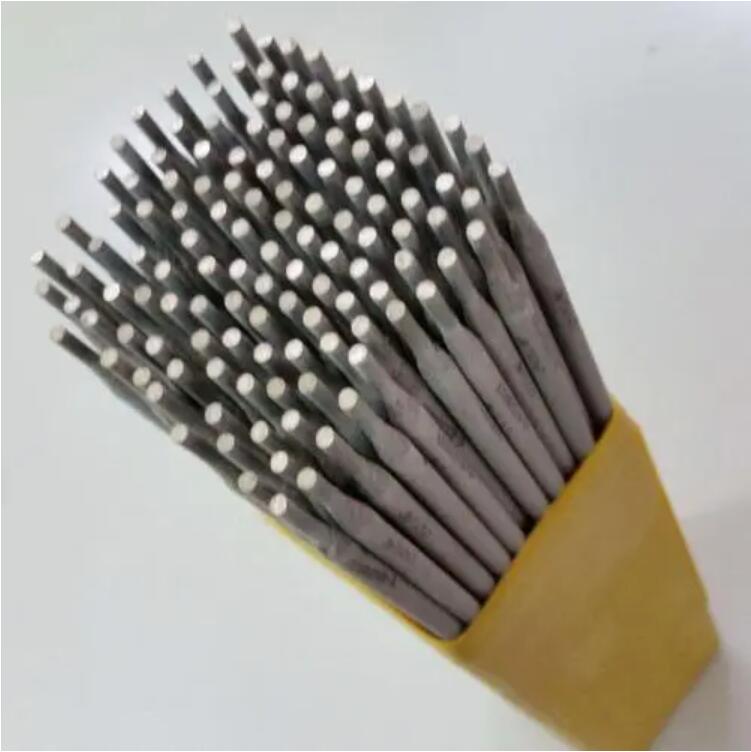
Upon practical examination, 304 gasless MIG welding wire showcases impressive usability. As an experienced welder will attest, the integration of flux within the wire leads to a simplified setup where beginner and intermediate welders can focus more on honing their technique instead of contending with the logistics of gas shielding. The reduced setup timing and portability significantly improve efficiency without compromising on the quality of the weld. It’s a boon for on-site repairs or in remote locations where traditional gas supplies may be unavailable or inconvenient to transport.
Examining the technical aspects of gasless MIG welding with 304 wire highlights several factors contributing to its reliability and performance. Firstly, the flux within the wire creates a slag layer as it cools, providing a cleaner finish that requires minimal post-weld maintenance compared to typical MIG welding processes. Secondly, although slightly different in initial handling compared to conventional MIG methods, the learning curve is manageable and is quickly overtaken by the convenience of not handling shielding gases.
gasless mig welding wire 304
Despite these advantages, professionals understand the importance of selecting the correct settings to optimize the welding outcome. Since 304 stainless is more sensitive to heat, welders must meticulously adjust voltage and wire feed speed to avoid excessive heat input that can lead to warping or structural weaknesses in the weld. Precision is equally crucial in maintaining bead consistency, reducing spatter, and ensuring the continuity of the protective slag.
From an industry expert interview, it's evident that trust in 304 gasless MIG wire is also bolstered through independent reviews and welding forums. Experienced welders consistently report exceptional tensile strength and durability in their projects, reinforcing the brand authority of manufacturers who specialize in these specialized wires. Moreover, the environmental robustness of 304 wire—characterized by its adaptability in unfavorable outdoor conditions such as wind—is a trust-building feature that showcases reliability across diverse applications.
Authoritativeness in the field is further achieved through certifications and compliance with industry standards. Trusted manufacturers generally provide detailed data sheets, performance metrics, and compliance certifications to assure users of the product’s reliability and quality standards. This transparency builds consumer confidence, encouraging more adopters to embrace gasless MIG wire as part of their standard operation.
In conclusion, the union of 304 stainless steel with gasless MIG welding technology offers an enticing mix of simplicity and performance for the modern welder. The merit of the product comes not only from the tangible benefits of reducing auxiliary equipment but also from the implicit assurance of reliable welds. Ultimately, the integration of new materials and techniques continues to evolve the welding profession, and 304 gasless MIG wire is an exemplary testament to these progressive innovations.