Steel MIG welding wire stands as a crucial component for industries that rely on precision and durability in their welding processes. With over a decade of experience in the welding industry, I've witnessed firsthand the evolution and significance of using high-quality welding wire, particularly when it comes to steel.
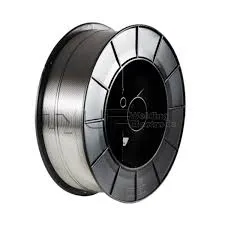
MIG (Metal Inert Gas) welding, also known as GMAW (Gas Metal Arc Welding), is a process that has become a staple in various industries, including automotive, construction, and manufacturing. The wire used in this process acts as both the electrode and the filler material, making its quality paramount to the success of the welding operation. As an expert in welding solutions, I have seen how the right choice of steel MIG welding wire can significantly enhance the structural integrity and finish of a weld.
The demand for high-quality steel MIG welding wire has surged due to its wide-ranging advantages, such as ease of use and versatility. While other types of welding techniques might require more skill and practice to master, MIG welding offers a more accessible entry point for novices without sacrificing effectiveness for veteran welders. The consistent feeding, paired with a shielding gas, ensures that the welding process is smooth and produces a clean, strong joint.
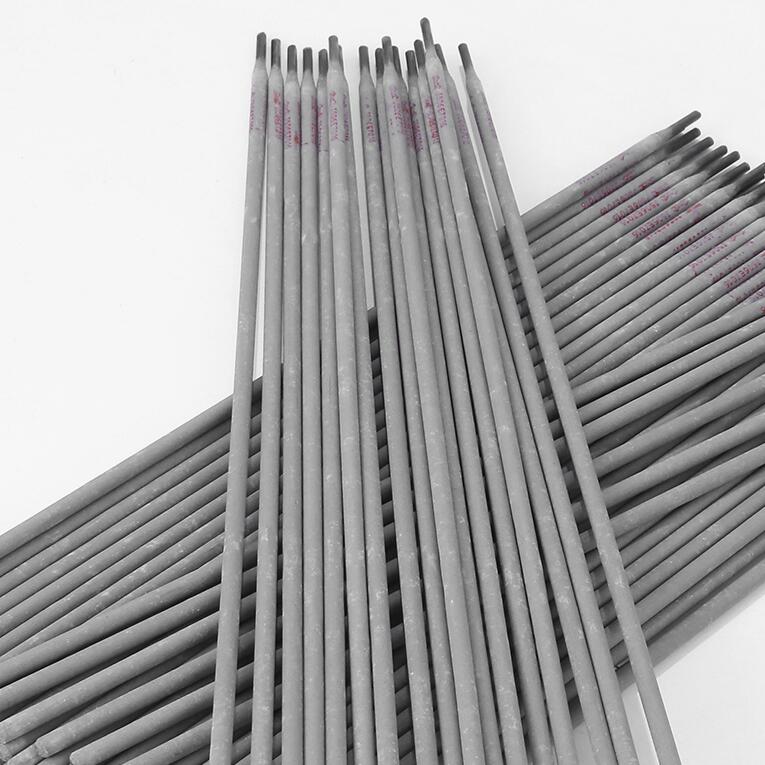
Steel comes with its own set of challenges, such as dealing with issues of strength and corrosion resistance.
Selecting the appropriate steel MIG welding wire can mitigate these challenges. Among the various options available, ER70S-6 is one of the most commonly used steel welding wires due to its ability to handle surface rust or mill scale on steel and its excellent feedability. The wire contains higher levels of deoxidizers, such as manganese and silicon, allowing for a cleaner bead with minimal spatter and good all-position welding.
steel mig welding wire
When assessing authority in the field of MIG welding, it is essential to rely on manufacturers with proven track records of testing and innovation. Quality steel welding wire is typically subjected to rigorous testing to ensure it meets industry standards. Certifications from authoritative bodies, such as the American Society for Testing and Materials (ASTM) or the American Welding Society (AWS), can be indicators of trustworthiness and reliability in the products offered.
Trust is built not only on the wire’s performance but also on the continued support and guidance from suppliers. Look for suppliers who offer comprehensive support, including material safety data sheets (MSDS), detailed product specifications, and access to technical customer service. This kind of support is vital for tackling any challenges you may face during the welding process, ensuring a seamless integration with your existing welding systems.
Moreover, manufacturers are continually innovating to improve the properties of steel MIG welding wire. Recent advancements focus on enhancing wire surface coatings to improve conductivity and feedability, reducing the potential for wire burn-back or bird-nesting in the feeder system. These innovations ensure that your welding work remains efficient and cost-effective, minimizing downtime and rework.
In summary, the choice of a steel MIG welding wire is not merely a purchase; it's an investment in the quality, efficiency, and durability of your welding operations. The right wire not only simplifies the welding process but also enhances the overall quality and longevity of your welded structures. As you navigate the plethora of options available, placing a premium on quality, certification, and supplier support will ensure you make the best choice for your specific welding needs.