Choosing the right welding rod can make a significant difference in the quality and durability of your welding projects. Welding rods, often known as filler metals, play a crucial role in the welding process by acting as a bonding agent that helps join two metal pieces together. With numerous options available in the market, understanding the nuances of each type can enhance not only the quality of the weld but also the efficiency of the welding practice.
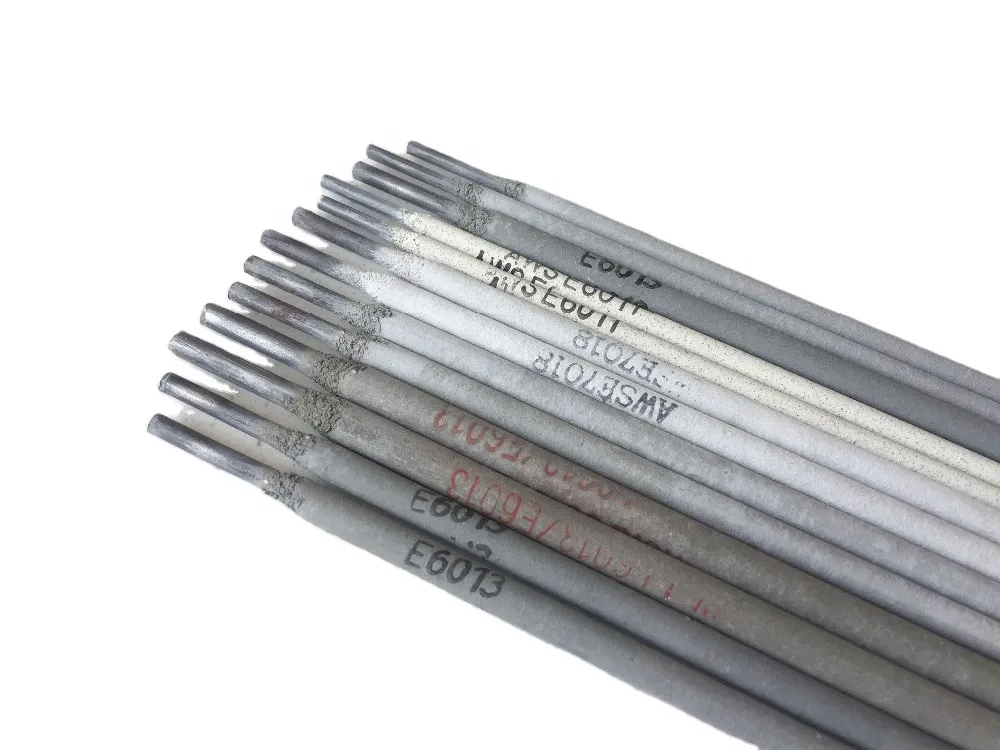
Selecting a welding rod begins with understanding the base metals you are working with. For instance, if you are joining mild steel to mild steel, the E6010 or E6011 rods are often recommended due to their deep penetration and fast freeze characteristics. These rods work exceptionally well for out-of-position welding, making them versatile choices for different projects.
The welding environment also dictates the choice of the welding rod. In fieldwork scenarios where wind and outdoor conditions are a factor, an E6011 rod is often preferred over others because of its ability to maintain stability despite external environmental challenges. On the other hand, if you're working indoors in a controlled environment, E7018 is an excellent choice due to its low hydrogen component, which produces cleaner welds with minimal cracking.
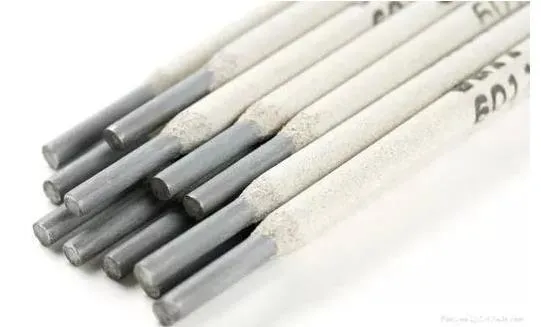
Experience teaches that the diameter of the welding rod matters significantly. Thicker rods are suitable for heavier plates, providing more filler metal necessary for robust welds, whereas thinner rods are ideal for delicate structures. A 1/8-inch rod is typically considered a general-purpose size, adaptable to various thicknesses and metal types, ensuring a sturdy weld without excess metal buildup.
welding rod
The choice of welding rod also affects the overall appearance and finish of the weld. Aesthetics might be secondary to functionality, but in projects demanding visually appealing welds—such as artistic metalwork or high-visibility construction projects—choosing the right rod that minimizes spatters and generates smooth beads is crucial. For such tasks, rods like ER70S-6 for MIG welding or even E7014 for stick welding are recommended for achieving smooth and clean finishes.
Furthermore, the type of current available may also influence your choice. Alternating current (AC) compatible rods such as E7018AC are advantageous when specific equipment constraints require the use of AC sources. This versatility offers flexibility, ensuring that you can adapt to various welding setups without compromising on the weld quality.
Thus, selecting the appropriate welding rod involves a balance of understanding the welding materials, working conditions, equipment capability, and desired final appearance. While expertise in welding techniques comes with hands-on experience, guidance from credible resources and industry authorities can further fine-tune one's skill in welding. Trust matters; therefore, always source your rods from reputable manufacturers to ensure consistent quality and performance.
In summary, the art of welding is significantly influenced by the choice of welding rods. Evaluating the material type, environmental conditions, rod diameter, surface finish requirement, and available power sources will steer you towards achieving strong, reliable, and aesthetically pleasing welds. By paying heed to expert recommendations and practical experience, you can master the nuances of welding rod selection and amplify the success rate of your projects.