For those in pursuit of mastering welding techniques, understanding the nuances of stick, MIG, and TIG welding is essential. Each method caters to distinct needs, materials, and levels of expertise, making the selection of the right technique pivotal for ensuring quality, efficiency, and safety. This enlightening exploration into these three welding methods aims to offer both novice and experienced welders an authoritative guide that enhances comprehension and application.
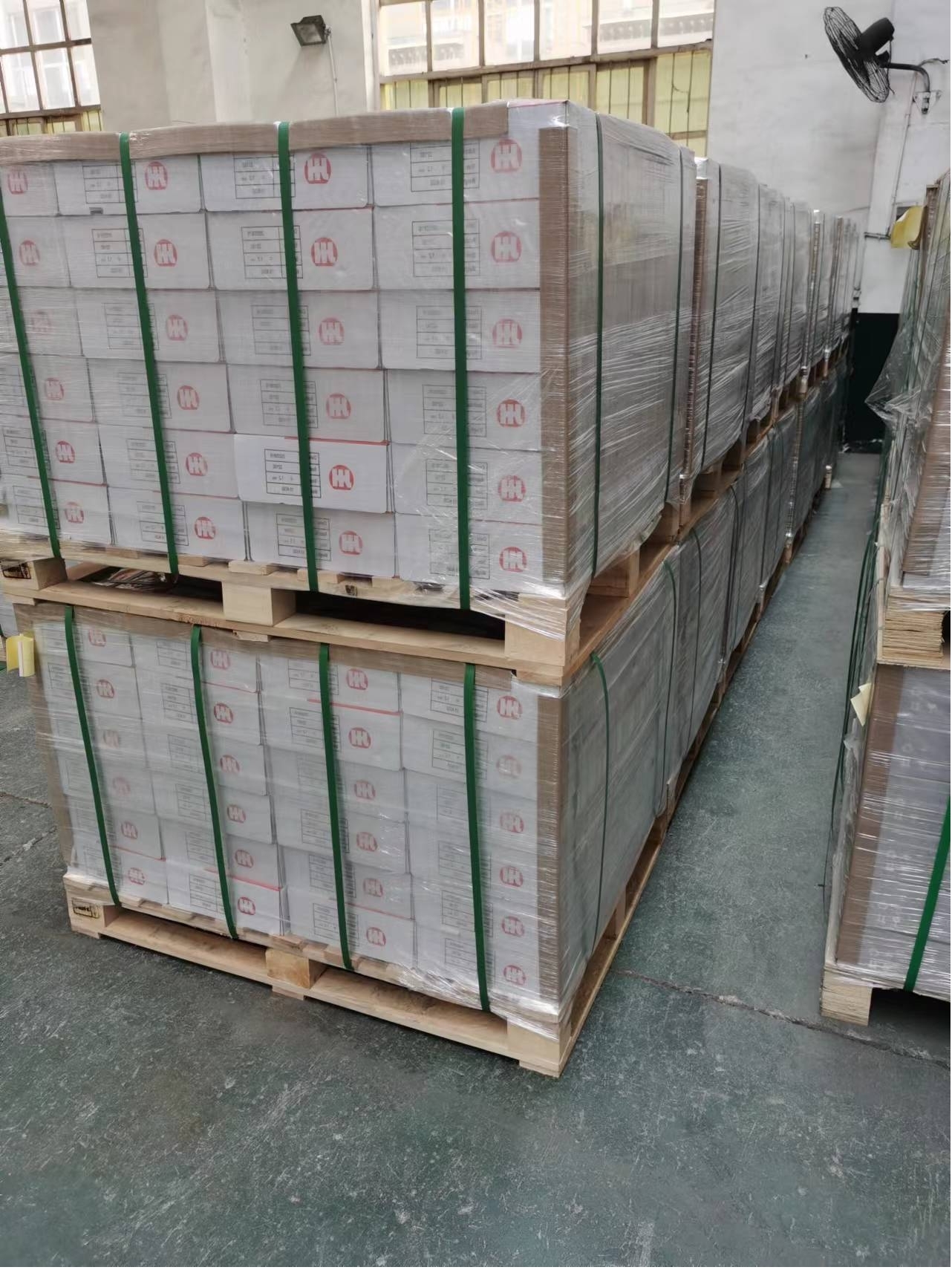
Stick welding, technically known as Shielded Metal Arc Welding (SMAW), is arguably the most straightforward form of welding, yet it comes with its unique set of challenges and benefits. Its portability and versatility make it ideal for outdoor use and various settings where other more intricate equipment might not be feasible. Developed in the early 20th century, it remains a preferred method for industrial and home projects. Electric current flows through a gap between the metal and the arc to produce intense heat. A significant advantage of stick welding is its ability to work well on rusty or dirty surfaces, which results in saving time on cleaning materials before starting the welding process. However, this technique often produces more slag and requires more cleanup, making it less favorable for fine or thin materials.
Metal Inert Gas (MIG) welding, or Gas Metal Arc Welding (GMAW), is synonymous with efficiency and ease of use, which explains its prominence in manufacturing, automotive repair, and hobbyist projects. What sets MIG welding apart is the continuous wire feed and shielding gas, often a mix of argon and carbon dioxide, which envelopes the weld, protecting it from oxygen and other atmospheric elements. This automated feature allows welders to work more quickly and achieve a cleaner weld, which is indispensable in high-speed production environments. The downside, however, is its requirement for a clean surface,
as contaminants can cause welding defects. MIG welding thrives in controlled environments, making it less versatile outdoors unless proper wind protection is utilized.
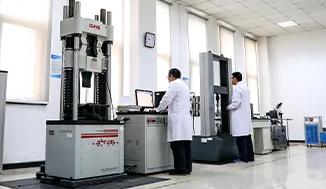
Then there is Tungsten Inert Gas (TIG) welding, or Gas Tungsten Arc Welding (GTAW), celebrated for its precision and the high quality it provides. This technique employs a non-consumable tungsten electrode and is often used when exacting welds on thin metals and non-ferrous materials like aluminum or stainless steel are needed. Though it demands higher skill levels and attention to detail, the outcomes justify the effort, with aesthetically pleasing, corrosion-resistant welds. The control offered over both the heat and the filler material during the welding process is unparalleled, catering to intricate welds on challenging materials. Drawbacks include slower welding speeds and the complexity of managing both the torch and filler rod.
stick mig and tig welding
Selecting the ideal welding technique depends greatly on the specific project requirements, materials involved, and environmental conditions. Stick welding’s robust nature makes it a go-to for outdoor tasks or when working with thicker, less finely prepared materials. Meanwhile, MIG welding’s efficiency excels in production lines where speed and clean surfaces can be maintained. TIG welding’s precision makes it indispensable for artisans and professionals seeking the finest welds on delicate materials.
Continuous training and practice across all techniques are crucial for ensuring both safety and proficiency. Each method has its learning curve, but with guidance from experienced mentors and continuous practice, mastery is attainable. Understanding these welding forms will not only improve craftsmanship but also empower a welder to make informed decisions about equipment purchase and material compatibility.
In conclusion, while each welding method—stick, MIG, and TIG—has its place within the welding domain, the ultimate choice depends on the project’s demands and the welder's expertise. Striking the balance between project needs and welding capabilities is key to achieving the best outcomes. By investing in learning the intricacies of these welding types, welders reinforce their status as skilled artisans, capable of navigating any project challenge with confidence and precision.