Tubular welding wires, or flux-cored wires, represent a significant technological evolution in the realm of welding materials. Their innovative design combines the efficiency of solid wires with the versatility and performance-enhancing features of flux, making them indispensable in various industries, including construction, automotive, and shipbuilding.
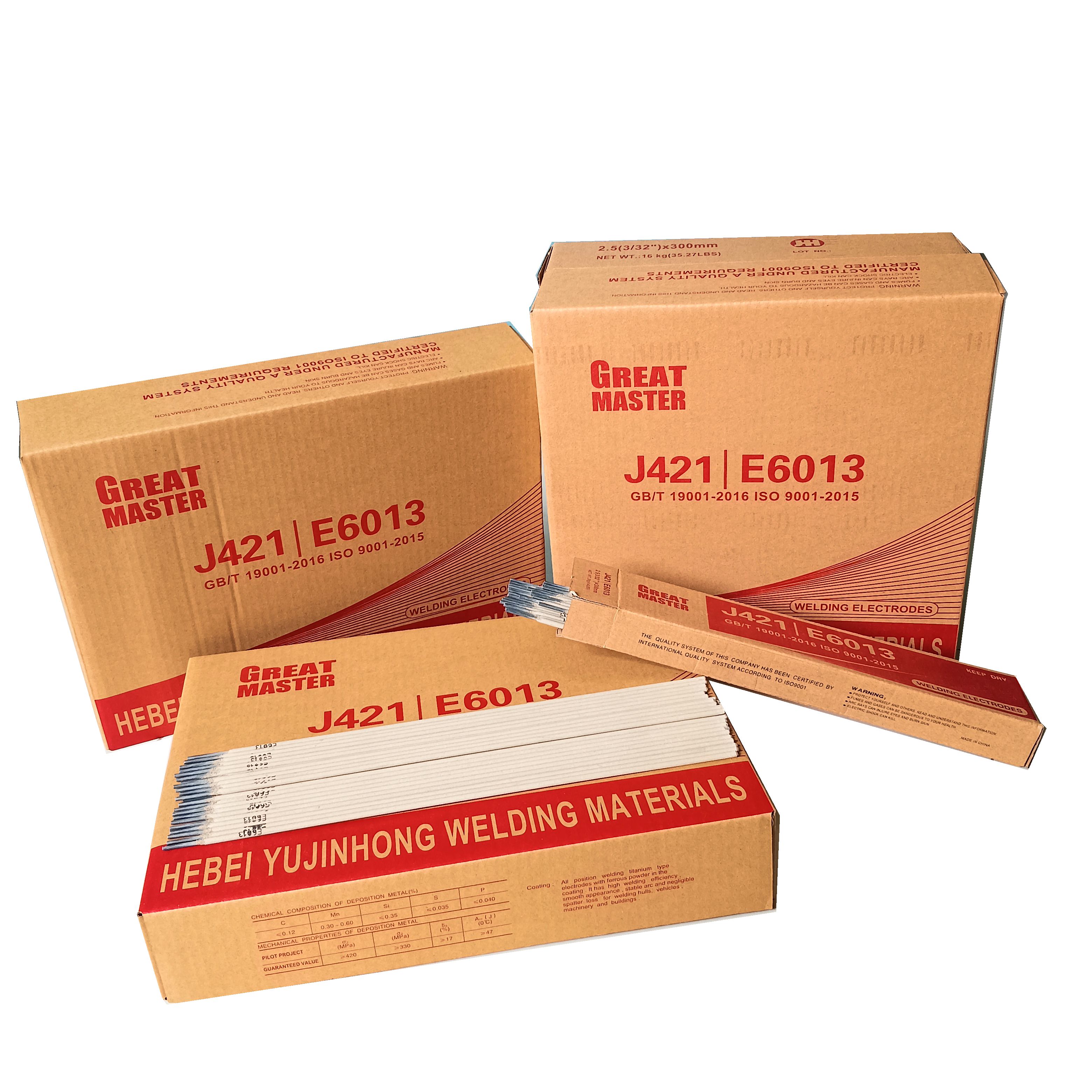
Based on real-world experience among skilled welders, tubular welding wires have made a substantial impact on productivity and work quality. Their cored nature allows for higher deposition rates and increased travel speeds compared to traditional solid wires.
This increased efficiency translates into substantial time savings on extensive welding projects. Experienced welders often highlight the enhanced weld quality that results from the use of these wires. The flux core stabilizes the arc, minimizes spatter, and improves joint penetration, resulting in cleaner, stronger welds with fewer defects.
From an expertise perspective, understanding the variety of tubular welding wires available is crucial. They are categorized mainly into two types self-shielded and gas-shielded. Self-shielded wires do not require external shielding gas, which makes them ideal for outdoor applications where wind might disrupt the shielding gas from a gas cylinder. On the other hand, gas-shielded wires require an external gas supply, usually a mixture of argon and carbon dioxide, which enhances arc stability and reduces oxidation, making them suitable for indoor applications requiring high aesthetics and precision.
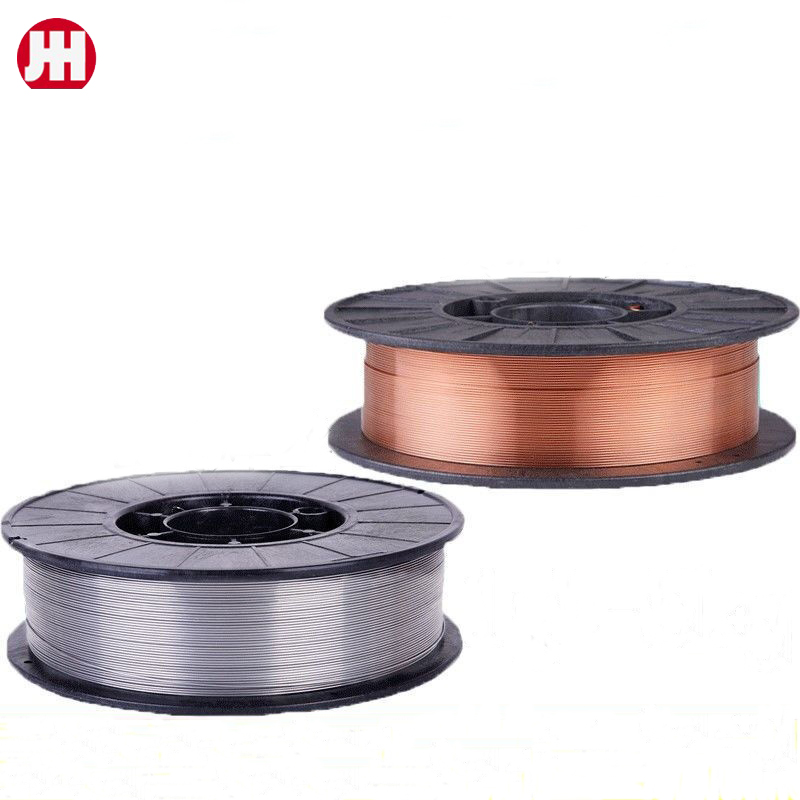
The authoritativeness of tubular welding wires in the welding industry is reinforced by numerous technical studies and endorsements from industry bodies such as the American Welding Society (AWS). Research has consistently shown that these wires are capable of producing higher-quality welds with less operator skill compared to conventional welding materials. Their flexibility in being used on rusty or dirty materials without the need for extensive surface preparation further elevates their authoritative standing among welding materials.
tubular welding wire
Trustworthiness is also a critical aspect of tubular welding wires. Manufacturers adhere to strict quality control processes to ensure consistency in performance. When selecting a tubular welding wire, it is essential to consult specifications and certifications, such as those provided by the AWS or ISO standards, to guarantee that the wire meets the necessary criteria for the specific application. Trust also stems from the shared experiences within the professional welding community, where feedback and empirical results add a layer of reliability to the use of these wires.
The inherent advantages of tubular welding wires lie in their composition and the level of control they offer welders over the welding process. They are composed of a metal sheath and a flux-filled core. The core contains various compounds that serve multiple roles, such as arc stabilization, shielding gas production, and slag formation, which protects the weld pool from atmospheric contamination. This complex design demands professional knowledge to optimize its benefits fully, underscoring the importance of proper training and certification for welders intending to use these materials effectively.
Furthermore, the development in tubular wire technology continues to evolve, with manufacturers investing in research to improve their composition for better performance and adaptability. Advancements such as the development of wires suitable for thin metals, with reduced burn-through risk, and the creation of wires capable of high-strength steel welding while maintaining ductility are on the horizon, promising even more robust solutions for demanding projects.
As a product, tubular welding wires offer a compelling proposition for both seasoned professionals and those new to the trade. Their superior performance characteristics, coupled with their versatility across different environments and conditions, make them an excellent choice for a broad range of applications. This versatility, combined with ongoing innovations in material science, ensures that tubular welding wires remain at the forefront of welding solutions, providing an advantageous edge in any project where quality and efficiency are paramount. Whether tackling a complex industrial framework or engaging in detailed repair work, these wires continue to prove their worth, characterized by reliability and exceptional welding outcomes.