In the industrial sector, the significance of welding wires, especially those used in CO2 welding processes, cannot be overstated. Welding wires are fundamental to numerous construction and manufacturing applications, offering efficiency and precision that few other materials can match. However, like all products, not all welding wires are created equal, and it is paramount to choose wisely to ensure high-quality outcomes. This article will delve into the true essence of CO2 welding wires, providing insight into their utility and guiding you on making the right purchase decisions.
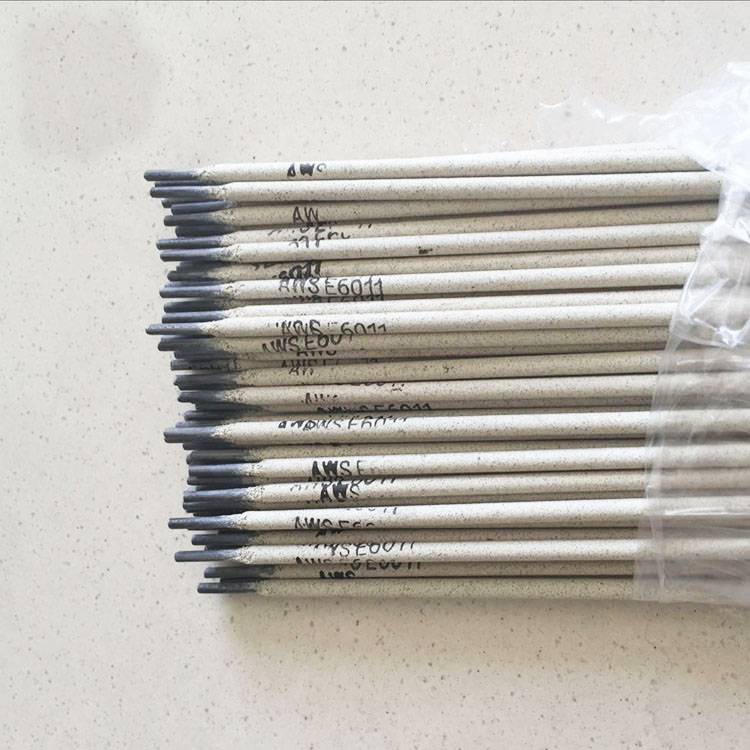
CO2 welding wires have grown to be a staple in industries ranging from automotive to shipbuilding, thanks to their unique capability to deliver deep penetration welding with relatively low heat input. This is particularly advantageous in reducing base metal distortion, thereby preserving the structural integrity of components being welded. When using CO2 as a shielding gas, these wires help create a stable arc that enhances the weld quality, making them particularly suitable for heavy-duty industrial applications.
From an expert's perspective, selecting the right CO2 welding wire involves understanding its compatibility with the material to be welded, the desired mechanical properties, and the environmental conditions under which the welding will take place. These wires typically consist of mild steel or alloyed variants and come in different diameters, which should be chosen based on the thickness of the material being welded and the required weld penetration. Using the wrong diameter can often lead to issues such as insufficient weld penetration or excess spatter, which can compromise the weld's strength and appearance.
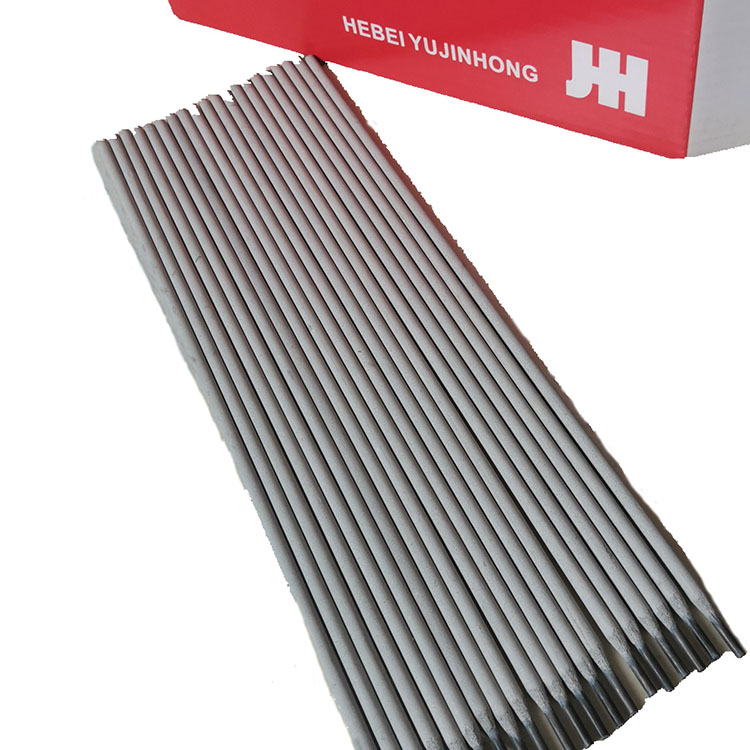
A pivotal consideration is the manufacturer's expertise and reputation. Opting for a trusted brand ensures that the wires have undergone stringent quality control processes, which translates to consistent performance. Look for certifications and user testimonials that vouch for the wire's reliability. Brands that invest in research and development often pioneer innovations that improve efficiency and sustainability in welding processes.
Reliability and trustworthiness in a product come from not just its performance but also how it's marketed. Transparent information about the composition and mechanical properties of the welding wire allows users to make informed decisions. Furthermore, an authoritative source will offer guidance on proper storage to prevent moisture absorption which can lead to oxidation and affect the wire’s usability. Established suppliers often provide resources and training to maintain high standards in welding practices, emphasizing the critical nature of handling and storage of CO2 welding wires.
welding wires co2
The professional community recognizes that while hardware is critical, technique plays an equally crucial role in achieving optimal results.
Continuous user experience sharing contributes to a deeper understanding of CO2 welding wires’ practical applications. Learning from seasoned welders provides practical insights into troubleshooting and optimization techniques, which align with the dynamically evolving needs of modern industry demands.
Moreover, in the context of sustainability and waste reduction, there is a growing emphasis on developing welding wires that not only provide superior results but are also environmentally responsible. Manufacturers are developing new alloys and coatings that reduce the environmental footprint of welding processes. As industries strive toward greener practices, selecting CO2 welding wires made with recycled materials or those that offer minimal fume production can align with broader sustainability goals.
To remain competitive, industries must adapt to technological advancements, and CO2 welding wires are a dynamic aspect of this evolution. Automation and precision engineering continue to shape modern welding practices, increasing the demand for wires that are compatible with robotic applications and advanced welding equipment. The consistency and feedability of these wires in automated systems enhance overall output and reduce operational costs, reflecting the economic advantage of investing in quality wires.
In conclusion, choosing the right CO2 welding wires necessitates a balance of quality, compatibility, expertise, and environmental awareness. As the market continues to evolve, staying informed and selecting high-caliber wires will ensure the longevity and success of any welding application, cementing trust in your operations and creating a solid foundation for future industrial innovations.