The 3.2mm welding electrode E6010 is a critical tool for welding professionals and enthusiasts seeking precision and quality in their welding projects. As an electrode that stands out due to its unique composition and versatility, E6010 promises not only superior penetration but also a smooth arc that enables a wide range of applications. Gaining insight into its properties, applications, and handling can significantly enhance one's welding repertoire and ensure unmatched quality and reliability in their work.
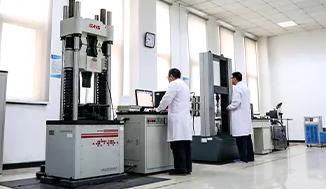
Understanding the E6010's Composition and Properties
At its core, the E6010 electrode is designed for high cellulose sodium flux coating, which contributes to its deep penetration and fast-freezing slag properties. The '60' indicates a tensile strength of 60,000 psi, while the '0' reflects its usability in all positions. These specifications make the E6010 incredibly effective for welding tasks that demand robustness and versatility. With a diameter of 3.2mm, it is the ideal size for projects requiring moderate to heavy penetration, providing the welder with sufficient control over the weld pool.
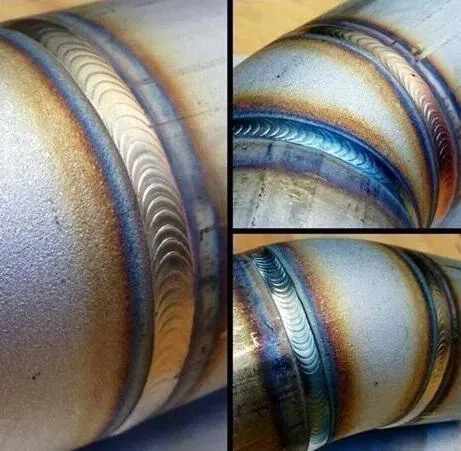
Applications and Benefits
Due to its high penetrating ability, the E6010 electrode is particularly beneficial for welding in situations where joints are not meticulously fit-up, or where there's a presence of rust or mill scale that needs overcoming. It is frequently employed in pipeline welding, shipbuilding, and on construction sites. The ease of slag removal and smooth bead finish also make it a preferred choice for root pass welding.
E6010 is highly valued for its ability to perform well in difficult positions—overhead, vertical, horizontal—making it indispensable for structural work where varied angles are a common challenge. The electrode's capacity to work effectively on both AC and DC power sources enhances its flexibility, accommodating a wide range of power setups that welders might encounter on-site.
Handling and Technique
3.2mm welding electrode e6010
Achieving the best results with a 3.2mm E6010 electrode requires mastering specific techniques and handling practices. Maintaining a short arc length is crucial; it can have a substantial impact on the weld quality and penetration. A longer arc might result in excessive spatter and insufficient penetration, while too short an arc can lead to electrode sticking.
Given the fast-freezing slag nature of E6010, it is vital to employ a whip and pause technique. This technique involves a rhythmic back-and-forth motion—whipping the electrode away slightly and then back into the weld pool—to control the heat input and build up materials efficiently without compromising on the integrity of the weld.
Further emphasizing its usability, E6010 excels in conditions requiring root passes, thanks to its ability to secure strong and durable foundational welds. However, care must be taken to adjust the current to match the specific requirements of the welding task and material thickness. This ensures that the electrode's deep penetrating properties are optimally harnessed without risking overheating or burn-through of thin materials.
Trustworthiness and Authority
When selecting and utilizing a 3.
2mm E6010 welding electrode, quality assurance is paramount. Opt for reputable brands and adhere strictly to the manufacturer's recommendations on operational parameters to ensure reliability and safety. Professional training or certification in welding can also complement one's understanding and effectiveness with this electrode, promoting not only high-standard projects but also workplace safety.
In enhancing your skills with E6010, consider engaging with experienced welders, participating in forums, or attending workshops dedicated to advancing welding expertise. These initiatives can significantly expand your practical knowledge and application of this electrode, resulting in a superior welding craft. Adopting best practices and continuous learning builds credibility and positions you as an authoritative figure in the welding industry.
In conclusion, the 3.2mm welding electrode E6010 is not just a tool but a catalyst in achieving exceptional welding outcomes. Its precise design and versatile application make it a staple in professional and industrial settings. By mastering the techniques and appreciating its comprehensive benefits, users can assure enhanced quality, safety, and satisfaction in every project they undertake.