In the rapidly evolving landscape of welding technology, staying ahead requires not only advanced tools but also the incorporation of innovative materials that meet modern industry demands. Among these, CO2 solid welding wires from China have emerged as a pivotal component in the manufacturing sector. Their contribution to efficiency, quality, and sustainability in welding applications has been widely recognized, yet it is the deeper understanding of their properties that underscores their importance.
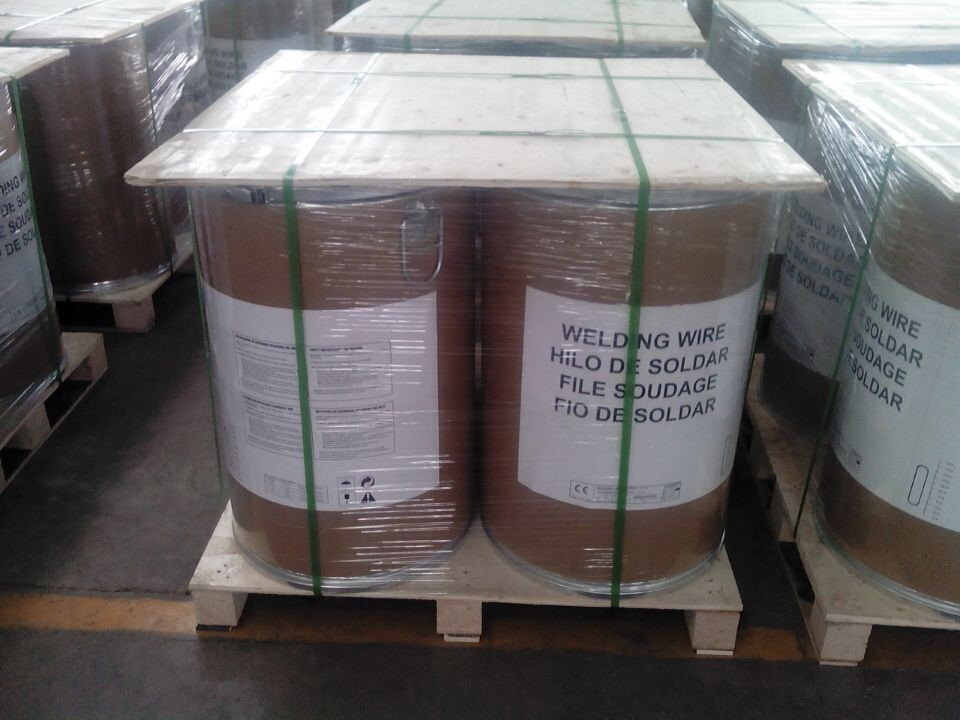
China, as a global leader in manufacturing, has been at the forefront in developing cutting-edge welding solutions. The CO2 solid welding wire represents a significant advancement, marrying the technological insights of modern metallurgy with practical application needs. These wires have gained substantial traction due to their cost-effectiveness and superior mechanical properties, making them indispensable for industries ranging from automotive to heavy machinery.
The notable advantage of CO2 solid welding wire lies in its composition and the resultant welding performance. These wires are typically made from low-carbon steel and undergo stringent quality checks to ensure consistency in diameter and chemical makeup. This precision in manufacturing translates to stable arc performance and excellent weld bead appearance, which are critical for high-speed welding operations. It facilitates a uniform heat input, minimizing the risk of deformities and enhancing the overall aesthetic of the welded joint.
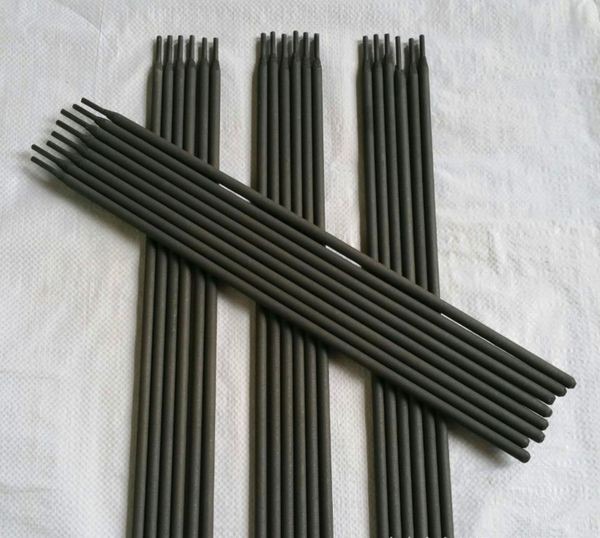
Expertise in utilizing these wires also extends to understanding their operational benefits. They are designed to be used with CO2 shielding gas, which is more cost-effective compared to argon blends. This not only reduces operational costs but also aligns with sustainability goals by minimizing environmental impact. Moreover, the reduced spatter during the welding process decreases cleanup time and material wastage, thereby optimizing production efficiency.
From an expert perspective, the choice of welding wire is not just about immediate welding results but also about long-term reliability and durability of the welds. CO2 solid welding wires from China are engineered to provide superior tensile strength and resistance to various stress factors. Their ability to maintain integrity under dynamic stresses makes them suitable for critical structural applications, where failure is not an option.
china co2 solid welding wire
Moreover, the expertise in China’s manufacturing processes ensures these welding wires adhere to international standards. They undergo rigorous testing for factors such as tensile strength, elongation, and corrosion resistance, which assures users of their reliability. As such, manufacturers and builders can rely on these wires for constructing infrastructures that demand the highest safety and durability standards.
When considering authoritativeness, it’s essential to note the extensive network of field professionals and industry partnerships that support the distribution and innovation of these products. Collaboration with global industry leaders has driven the development of product variations that cater to specific needs such as increased toughness for use in colder climates or enhanced ductility for dynamic load-bearing applications.
Trustworthiness in this context is founded on transparency and support. Manufacturers provide comprehensive documentation and support services, ensuring end-users have the necessary information and technical assistance to maximize the utility of their products. This includes detailed welding procedures, technical data sheets, and even workshops or training programs to facilitate proper usage and handling.
In conclusion, the CO2 solid welding wire from China epitomizes the synergy between advanced technological innovation and practical application efficiency. Its impact on the welding industry is profound, providing cost-effective, reliable, and high-performance solutions that meet contemporary welding demands. For stakeholders in industries relying on robust and sustainable welding practices, these wires are not just a material choice but a testament to modern engineering excellence. They represent the future of welding, offering a blend of performance, trust, and authoritative expertise that aligns perfectly with both current industrial requirements and future aspirations for sustainable manufacturing.