Tubular welding wire with a 1.2mm diameter is an indispensable tool in the field of metal fabrication and construction, where precision and efficiency are paramount. Leveraging the benefits of tubular welding wires offers numerous advantages over traditional solid wires, making them an increasingly preferred choice among professionals who demand high-quality welds and operational efficiency.
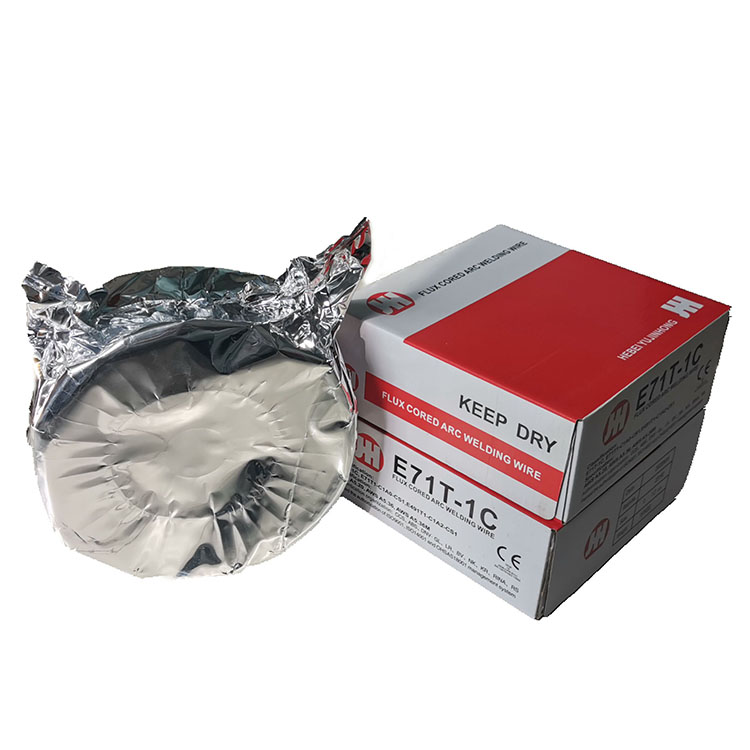
A primary advantage inherent to tubular welding wire is its ability to facilitate enhanced welding processes. This type of wire is often used in flux-cored arc welding (FCAW), a method renowned for its versatility and adaptability in various environments, including outdoor, windy conditions where shielding gas protection would be compromised. The design of the 1.2mm tubular wire, comprising a metal sheath filled with flux, ensures the weld is protected and mechanically reinforced, yielding robust and reliable joints.
From an experiential perspective, professionals who utilize tubular welding wire in day-to-day operations testify to its superior deposition rates and lower splatter, attributes that directly translate to time efficiency and material savings. These characteristics are particularly advantageous in large-scale projects where weld integrity and speed are crucial. Additionally, the penetration depth achieved with tubular wires is often greater, allowing for welding on thicker materials without requiring multiple passes, thus reducing labor costs and material consumption.
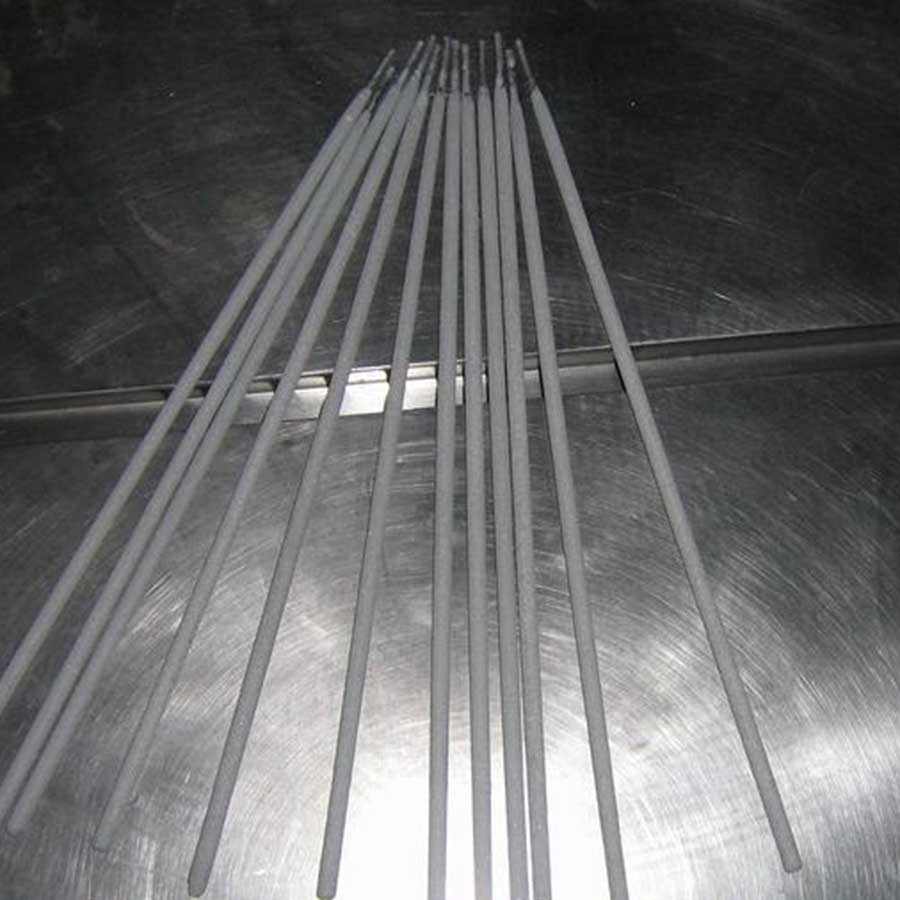
The 1.2mm size makes the tubular welding wire ideally suited for a range of applications, including structural steel, shipbuilding, and heavy equipment manufacturing. Its size allows for fine control over the welding arc, which is essential when working on intricate designs or seeking to minimize heat distortion to preserve the structural integrity of delicate components.
tubular welding wire 1.2mm
In terms of expertise, understanding the unique properties of tubular welding wires involves recognizing their composition and applications. The inner core of these wires contains a flux that serves multiple purposes aiding in arc stability, improving filler metal transfer, and facilitating slag formation which protects the weld pool. Mastery in handling these wires involves proficiency in adjusting parameters such as voltage, current, and travel speed to achieve optimal weld characteristics for specific material types and thicknesses.
Authoritativeness and trustworthiness in the use of tubular welding wire are established through robust industry standards and certifications. Leading manufacturing brands rigorously test their welding wires to adhere to international standards like AWS (American Welding Society) specifications, ensuring compatibility and performance across various equipment and conditions. Professionals relying on these wires can trust in the consistency and quality brought forth by compliance with such standards, offering peace of mind when undertaking critical welding operations.
Furthermore, ongoing advancements in manufacturing technology have allowed for the improvement of tubular welding wires, such as enhancements in the formulation of the flux core to reduce emission of harmful fumes and improve arc performance. These innovations reflect the industry’s commitment to safety and environmental responsibility, aligning with regulatory requirements and workplace health standards.
In summary, the choice of 1.2mm tubular welding wire is a testament to a commitment to precision, efficiency, and quality in the welding domain. Its construction and performance capability not only meet the rigorous demands of modern fabrication but also ensure that professionals can trust in consistent outcomes, enhancing their project outcomes and supporting the integrity of their craftsmanship. Whether addressing the needs of industrial manufacturing or complex infrastructures, tubular welding wires continue to serve as an essential component in the advancement of welding technologies and practices.