The 7018 welding rod stands out as one of the most versatile and widely used electrodes in the welding industry. Known for its reliability and high-quality results, this electrode is often the choice of professionals working on critical and major projects. Its unique chemical composition and operation profile make the 7018 rod an essential tool for achieving optimum weld integrity and performance.
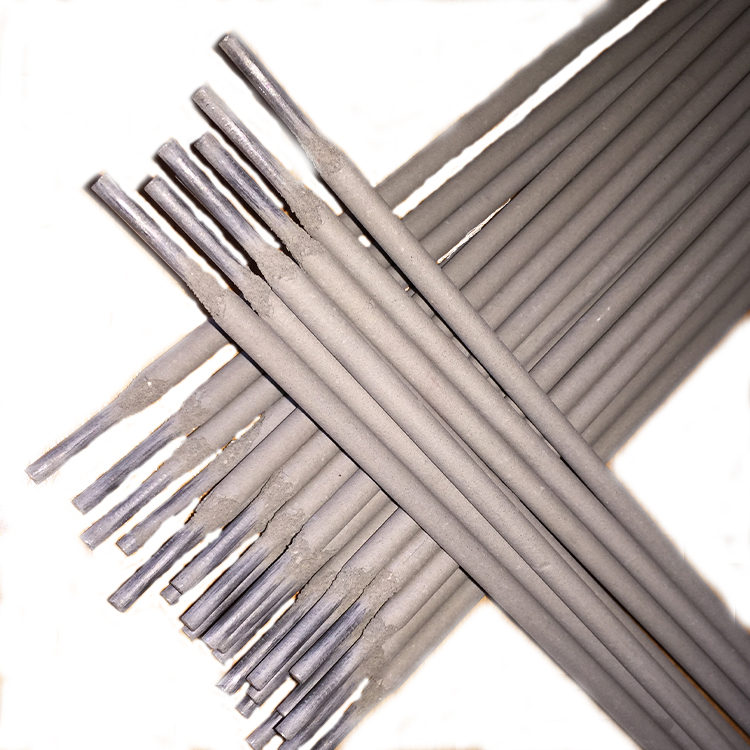
Crafted for both beginner and experienced welders, the 7018 welding rod shines in its ability to produce uniform welds with excellent appearance and minimal effort. Its composition primarily consists of an iron powder coating with low hydrogen content. This low-hydrogen characteristic is crucial, as it reduces the potential for hydrogen-induced cracking, a common issue in structural steel applications. This property makes the 7018 rod a preferred choice when working with medium to high carbon steels, where cracking is a concern.
The rod's versatility extends beyond its chemical composition; it is also known for its ability to provide a smooth, stable arc. When using a 7018 welding rod, the resulting welds have a high deposition rate, translating into efficient work progress and reduced production time. Its smooth arc characteristics also enhance the weld's surface, leaving minimal slag, which is easily removable, thereby reducing post-weld cleaning and enhancing productivity.
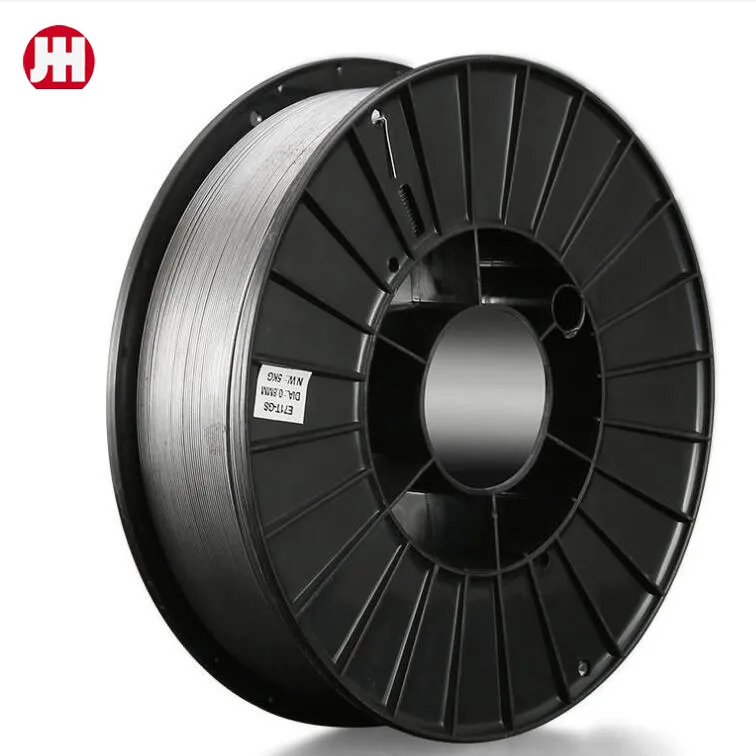
In terms of mechanical properties, welds made with 7018 welding rods exhibit exceptional tensile strength and ductility. Standard specifications cite a minimum tensile strength of 70,000 psi, making this electrode suitable for applications requiring robust structural integrity. Such qualities make the 7018 rod indispensable in industries such as bridge construction, shipbuilding, and pipeline integration, where uncompromising structural standards are the norm.
User expertise is another cornerstone of the 7018 welding rod's application. Despite its wide usage, optimal results require welders to adhere to specific handling and storage protocols. To preserve its low hydrogen properties, 7018 electrodes must be stored in a moisture-proof environment and, ideally, kept in a rod oven before use. This practice prevents the electrode from absorbing atmospheric moisture, which could compromise the weld's integrity.
welding rod 7018
Furthermore, effective handling techniques demand maintaining an appropriate travel speed and angle to ensure consistent bead quality. When using the 7018 rod, it is crucial to keep a short arc length to prevent porosity and ensure deeper penetration. Mastery in handling this welding rod also involves practicing stringer or weave beads depending on the project requirements, allowing for flexibility and adaptability in various welding scenarios.
The trustworthiness of the 7018 welding rod also comes from the extensive body of research and technical endorsements it has received. It consistently meets stringent industry standards, including the American Welding Society (AWS) specifications. Such certifications and tests ensure that users can rely on 7018 electrodes for critical applications where safety and quality cannot be compromised.
One should note that the 7018 welding rod also demands proper equipment calibration. Using it typically requires a direct current (DC) power source with the electrode positive (DCEP), although some variations accommodate alternating current (AC). Ensuring the equipment is correctly configured will maximize welding efficiency and quality.
Beyond its technical specifications, the 7018 welding rod carries testimonials from seasoned professionals in the field. Many experts attest to its unparalleled performance in challenging environments, praising its ability to produce consistently high-quality welds across different metals and thicknesses. The electrode's reliability has made it a staple in training programs where upcoming welders learn the importance of precision and quality in real-world applications.
The 7018 welding rod exemplifies the synthesis of innovation in electrode engineering and practical application expertise. Its widespread acceptance and consistent performance make it an authoritative tool in the welding community. Whether in standard manufacturing or cutting-edge infrastructural projects, this rod continues to set the benchmark for welding excellence.