Wire welding, particularly Metal Inert Gas (MIG) welding, stands as a vital technique in modern fabrication and metal joining processes. For professionals and hobbyists alike, mastering MIG welding offers an edge in efficiency and versatility.
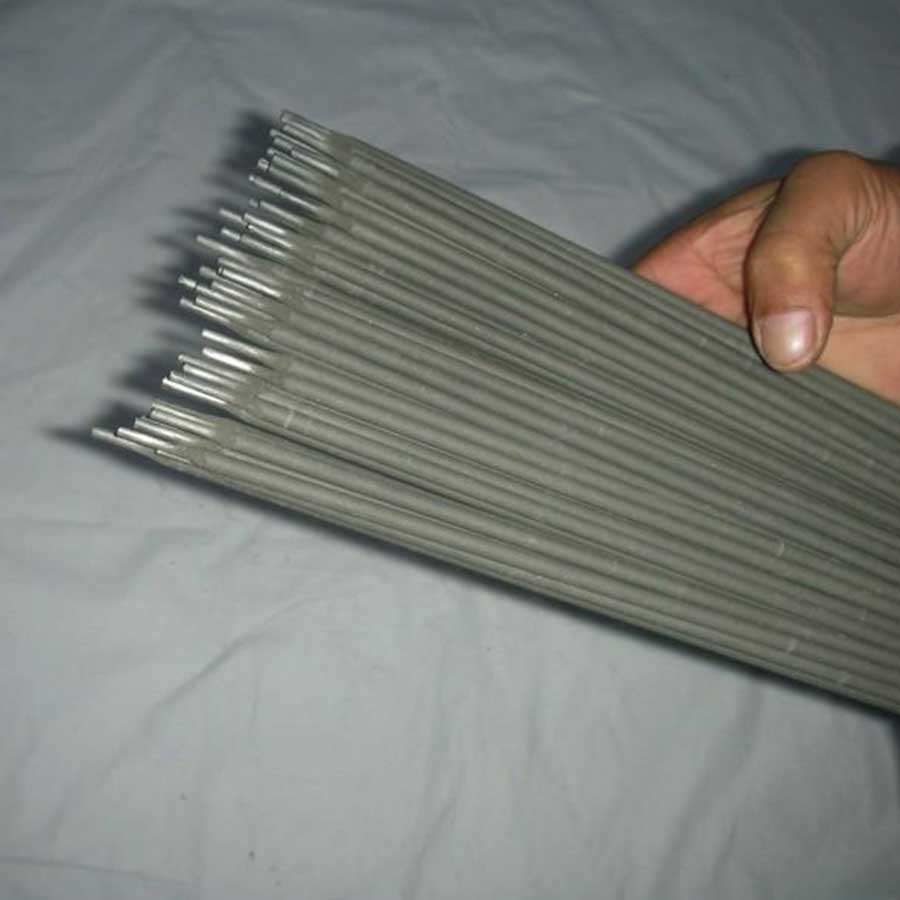
MIG welding, often praised for its speed and ease of use, suits a wide range of applications, from automotive repairs to large-scale industrial projects. This welding process involves a continuous feed of wire acting as both electrode and filler material. Shielding gas flows around the wire to protect the weld from contaminants in the air, creating a clean and robust joint.
In my journey of mastering MIG welding, I've uncovered several insights that transcend basic instructions and manuals. One of the fundamental elements is selecting the appropriate wire type and size. For beginners, the ER70S-6 is a versatile and commonly recommended type, offering compatibility with mild steel and excellent deoxidizers. However, the success of a weld heavily depends on matching the wire diameter with the material thickness—using a wire that's too thin can lead to undercuts while a wire that's too thick can result in inadequate penetration.
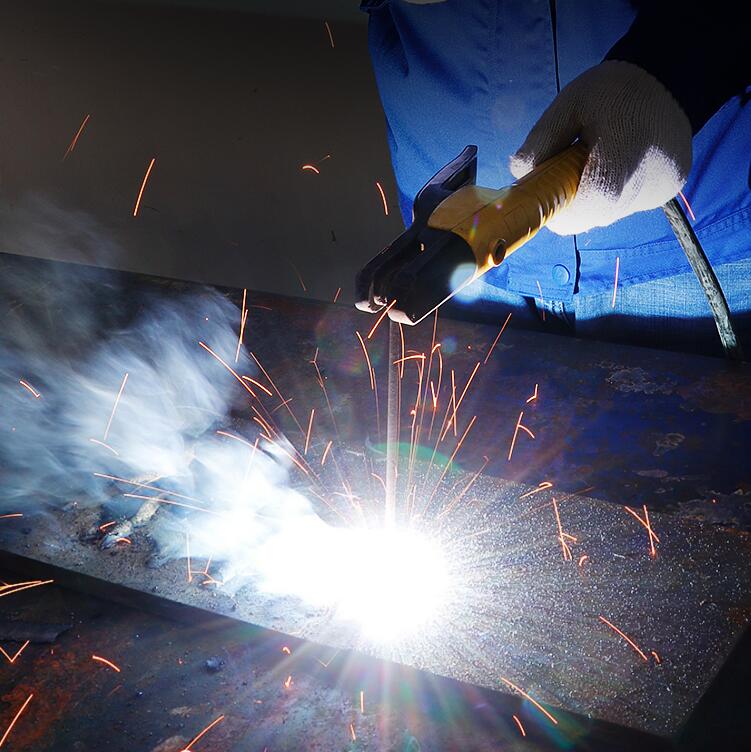
Another critical element is understanding the role of shielding gases. While a common 75% Argon and 25% CO2 mix works excellently for welding most materials, knowing when to switch to pure Argon or a tri-mix of Argon, CO2, and Helium for stainless steel or aluminum can substantially improve weld quality and tensile strength. Each gas combination fundamentally alters arc stability, spatter production, and weld pool fluidity.
wire welding mig
To enhance efficiency and weld quality, investing in a quality MIG welder with variable voltage settings is paramount. Modern designs offer user-friendly interfaces and digital displays for precise setting adjustments, allowing for a seamless transition between thin sheet metal and thick steel applications. My go-to is a model equipped with an inverter technology, which is not only lightweight and portable but also offers superior penetration and arc stability.
When it comes to position, mastering out-of-position and overhead welds extend a welder's versatility. Tackling these angles successfully requires deliberate and steady hand movements, controlling the molten pool, and adjusting travel speed to prevent sagging or burn-through. In my practice, I find using a push or forehand technique optimizes visibility and enhances gas coverage.
Safety, an often understated aspect, is integral to any welding activity. Maintaining personal protective equipment like auto-darkening helmets, fire-resistant gloves, and appropriate clothing cannot be overemphasized. Ventilation is crucial too,
as welding fumes can pose serious health risks. Ensuring a well-ventilated workspace or employing fume extraction systems not only safeguards health but also keeps your work area compliant with occupational health standards.
In sum, while MIG welding is accessible, achieving precision necessitates a confluence of knowledge, skill, and practice. Staying updated with the latest welding technologies and refining techniques continuously improves the efficiency and quality of the work. These practices, drawn from years of hands-on experience and dedicated learning, illustrate the sophistication beneath the simplicity of wire welding MIG—a craft where excellence shapes enduring structures and products.