Metal cored welding wire stands as an innovative advancement in the field of welding technology, offering compelling advantages over traditional solid wires. This type of welding wire is filled with metal powders or granules, which enhance the welding process and finished weld characteristics. With the continued evolution in manufacturing and construction techniques, utilizing metal cored wire is no longer a fringe choice but a strategic decision made by industry leaders aiming to achieve efficiency and superior weld quality.
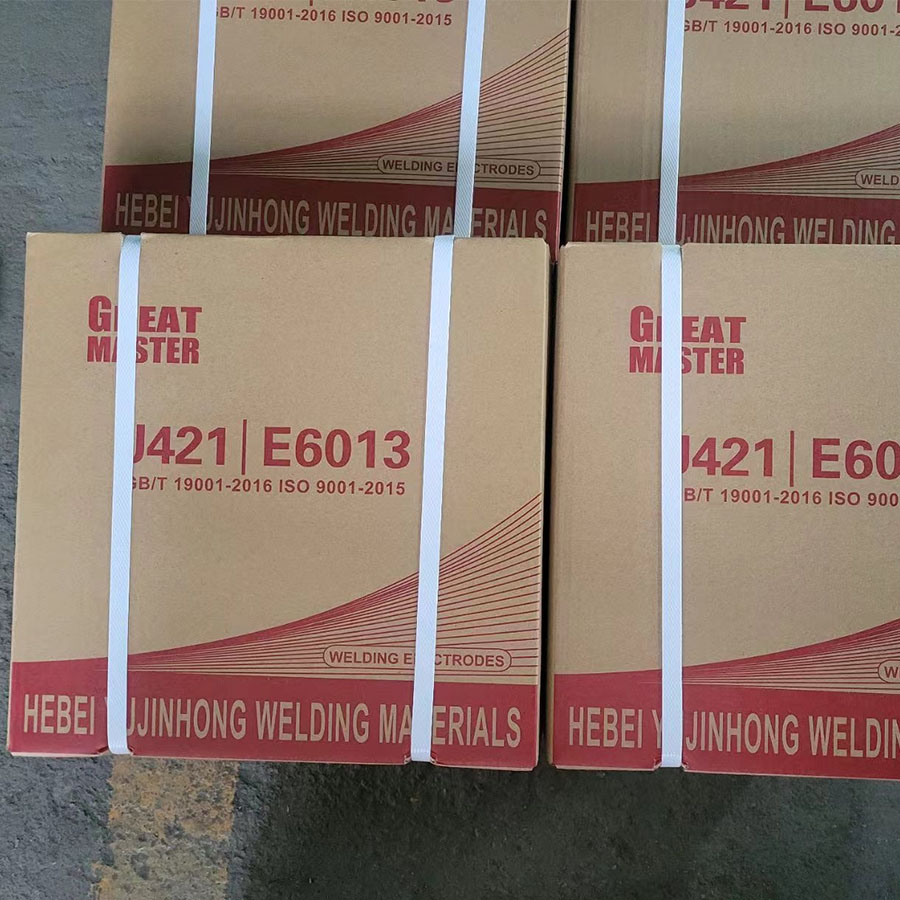
One of the primary benefits of metal cored welding wire is its remarkable deposition rate. Compared to conventional solid wire, metal cored wire can significantly increase productivity by depositing more metal at a faster rate. This ability to maximize the deposition rate while maintaining control over heating input ensures that metal cored wire is highly advantageous in applications where time efficiency is paramount without compromising the integrity of the weld.
The versatility of metal cored welding wire also lies in its adaptability to different welding positions and environments. Unlike traditional wires that may require adjustments or specific positioning, metal cored wires are adept at producing consistent welds in various situations. This flexibility is particularly beneficial in complex or constrained environments common in automotive, pipeline, and structural steel projects.
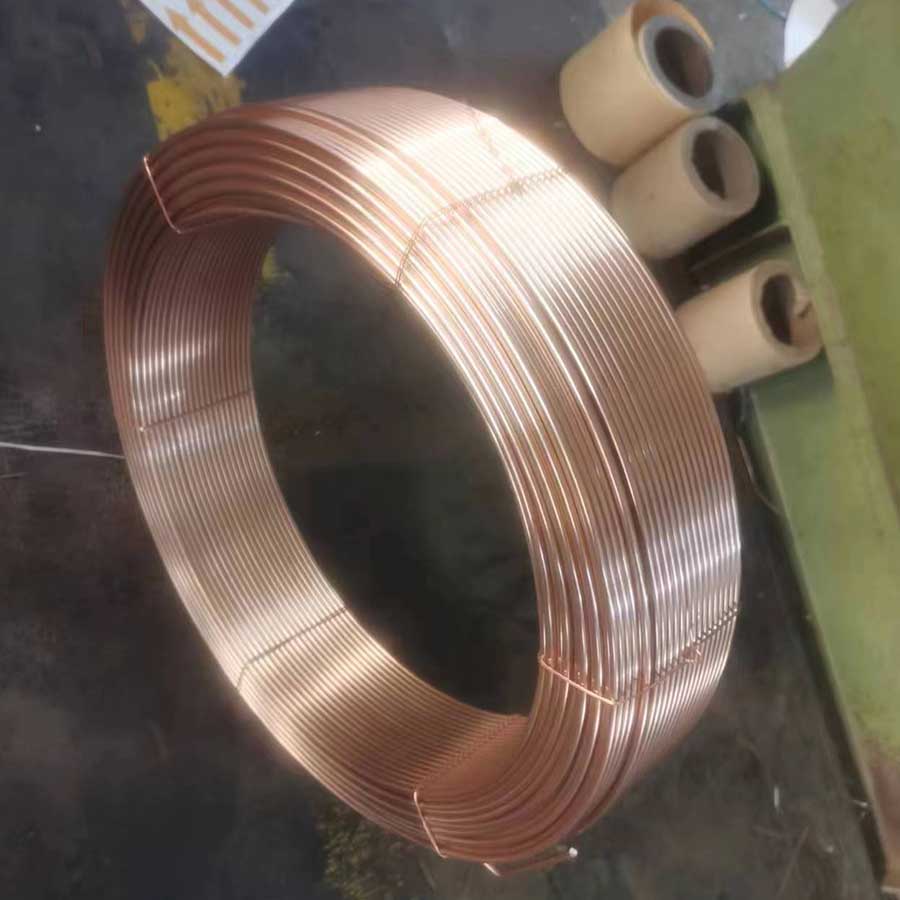
In terms of mechanical properties, metal cored wires deliver exceptional fusion characteristics and create more robust bonds between metal surfaces. The inclusion of metal powders allows for a broader range of alloy elements to be incorporated into the weld, which can lead to enhanced toughness, higher tensile strength, and improved impact resistance. These properties are crucial when the welded components are subject to extreme conditions or require long-term durability.
Moreover, metal cored welding wires provide an improvement in arc stability and reduced spatter. A stable arc is critical for ensuring the precision and cleanliness of the welding operation, thus reducing the need for secondary cleaning or grinding post-weld. With less spatter, manufacturers can achieve a cleaner working environment, which is not only aesthetically beneficial but also crucial for minimizing the need for extensive post-weld clean-up and reducing overall production costs.
metal cored welding wire
In discussing the cost-effectiveness of metal cored welding wire, it is important to factor in the comprehensive lifecycle savings it offers. While the initial investment may be higher than for standard solid wires, the efficiency gains in speed, quality, and reduced post-weld treatment lead to substantial cost savings over time. By improving the throughput and reducing the labor hours needed per project, companies can realize a quicker return on investment.
Expert welders and engineers often tout the ease of use associated with metal cored wire.
Its design allows for smoother feeding through the welding machine without frequent interruptions or equipment malfunctions. This reliability during operation is critical for maintaining steady progress in large-scale projects and avoiding costly downtime.
The authority of the metal cored welding wire in specialized applications cannot be understated. As industries push the boundaries of innovation, requiring more durable and flexible materials, metal cored wires are frequently specified in demanding scenarios ranging from offshore construction to high-strength pipeline fabrication. This specification often results from rigorous testing and validation, making metal cored wires a trusted solution when quality and performance are non-negotiable.
In building trustworthiness, the traceability and consistency of metal cored welding wire manufacturing ensure users can reliably predict performance outcomes. Leading manufacturers comply with stringent standards and quality control processes, giving users confidence in the repeatability of their welding operations, which is invaluable when producing critical components where precision is crucial.
In conclusion, metal cored welding wire represents an essential asset for modern welding practices, offering distinct advantages in efficiency, flexibility, mechanical strength, and operational fidelity. Its application extends across various sectors, effecting meaningful improvements in production workflows and end-product quality. As such, it stands not only as a product of choice but as a catalyst for enhanced welding performance, aligned with industry demands for innovation and quality assurance.