MIG aluminum welding wire is a transformative tool in the realm of welding. Designed specifically for gas metal arc welding (GMAW), it caters to professional welders who require both precision and strength in their work.
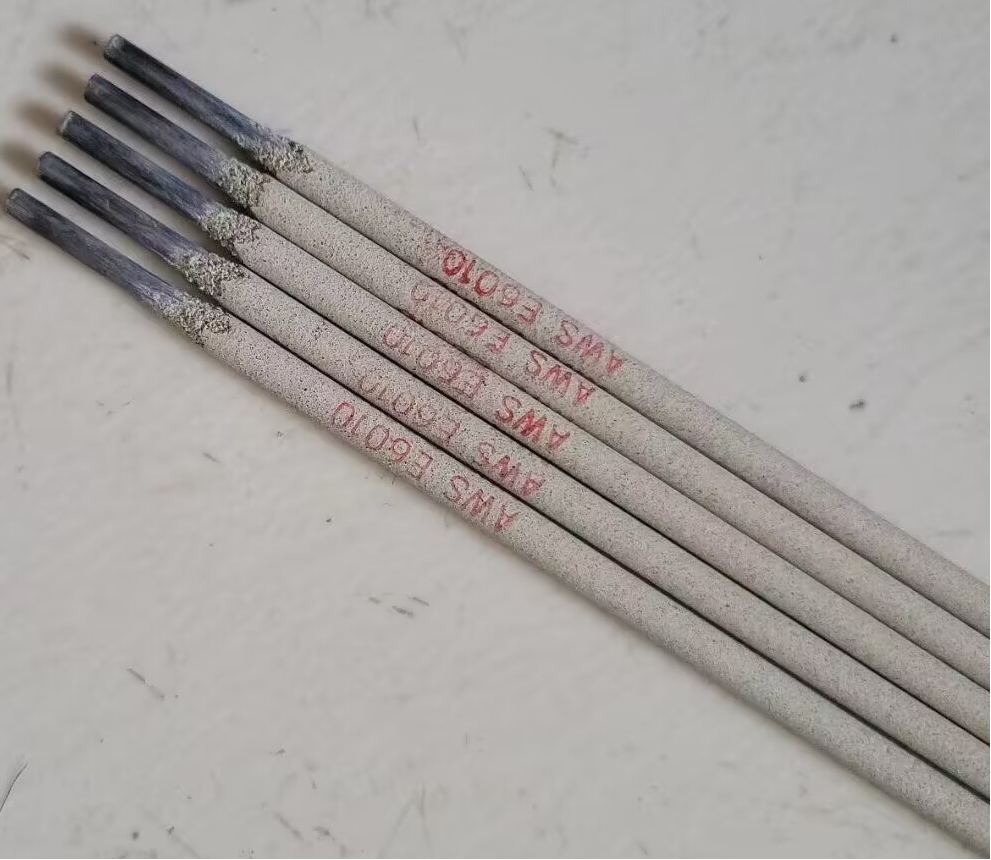
The primary appeal lies in its ability to handle aluminum—a notoriously fickle material that is both lightweight and prone to warping. Aluminum's properties necessitate wire that has a precise composition and uniform diameter, ensuring smooth, uninterrupted welding while minimizing defects.
Choosing the right MIG aluminum welding wire is pivotal. For those deeply entrenched in metal fabrication, the expertise begins with understanding wire types, sizes, and applications. For instance, the element magnesium in certain aluminum wires serves as a key player, enhancing strength. A popular choice like the ER4043 wire is renowned for its lower melting point and fluidity, making it ideal for general-purpose applications, while the ER5356 caters to projects requiring higher strength with good post-weld cracking resistance.
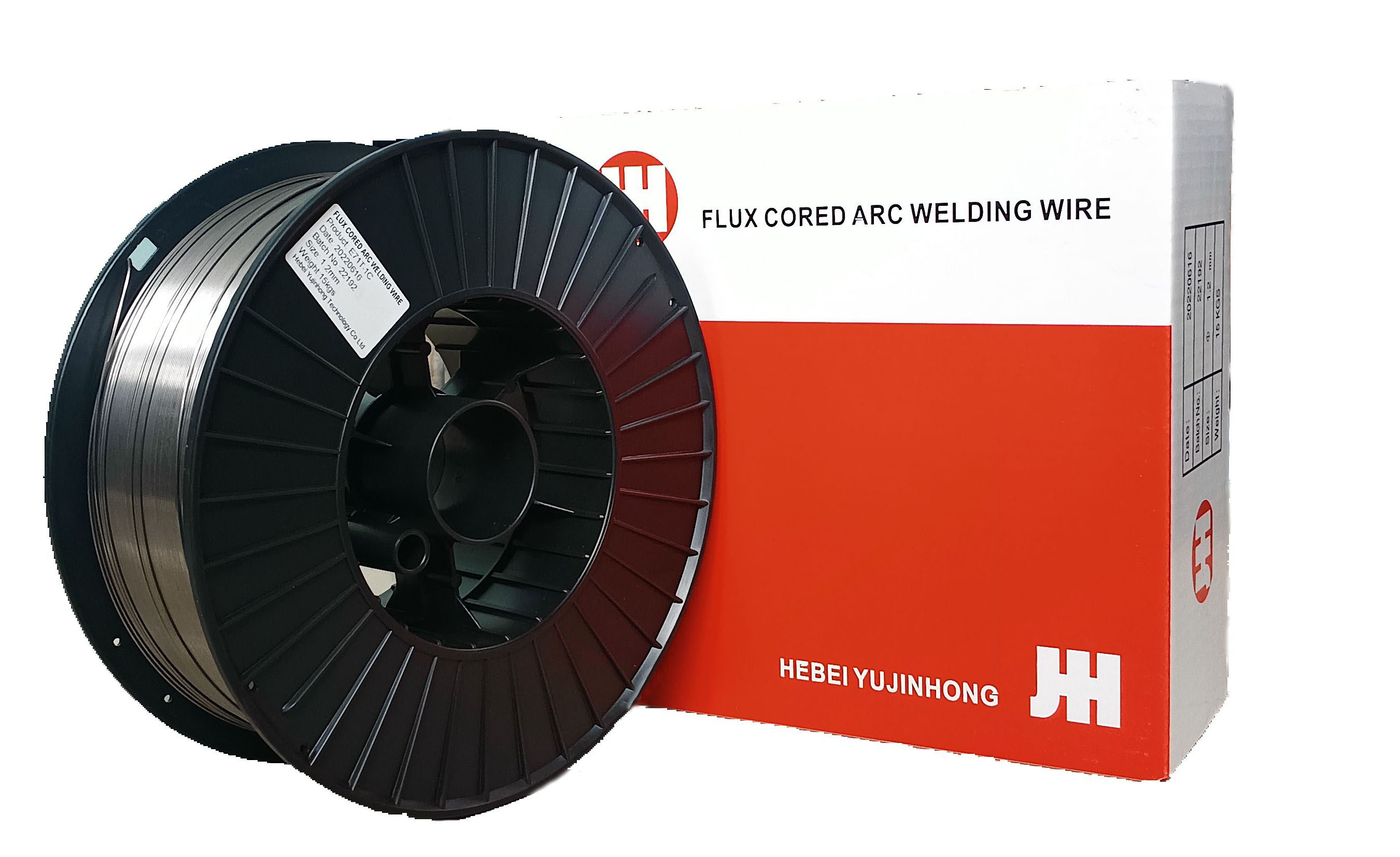
Experience shows that using high-quality wire reduces downtime in correcting weld imperfections. Therefore, welders often opt for wires from reputable manufacturers, understanding the link between quality and performance. The expertise in these scenarios involves assessing a product's deoxidizers, tensile strength, and pack-spool designs that impact feedability. Wire that feeds consistently without issues can significantly reduce wastage and project delays.
mig aluminium welding wire
The authority of MIG aluminum welding wires comes from rigorous testing and certifications that attest to their capabilities. The American Welding Society (AWS) classification provides assurance regarding its performance for various projects, whether it is automotive, aerospace, or marine. Many manufacturers maintain transparency by detailing these standards and the contexts in which their wires excel, bolstering trust among consumers.
Trustworthiness is further reinforced through user reviews and real-world applications. Welders often share insights and experiences on platforms like forums and videos, demonstrating the wire's performance in diverse conditions—from tackling thin aluminums of bicycle frames to challenging structures in shipbuilding. These testimonials provide valuable perspectives, guiding newcomers and seasoned professionals alike.
Furthermore, training and safety aspects associated with aluminum welding cannot be ignored. Proper technique and knowledge in dealing with aluminum’s thermal conductivity are vital. MIG aluminum wires are best handled in setups with clean environments to prevent contamination, and with parameters such as voltage and wire feed speed finely tuned to achieve optimal welds.
In conclusion, the right MIG aluminum welding wire acts as a tool of transformation. With the perfect blend of experience, expertise, authority, and trustworthiness, it allows professionals to create strong, reliable, and aesthetically pleasing welds. This is not merely about sticking metal together; it is about precision crafting superior products that stand up to rigorous demands. As the industries evolve and require more sophisticated welding solutions, the role of expertly engineered MIG aluminum wires will only grow, continuing to push the boundaries of what is possible in metal fabrication.