Stainless steel flux cored arc welding wires have revolutionized the welding industry with their versatility and efficiency, serving a critical role in numerous applications from construction to manufacturing. These specialized wires offer enhanced performance characteristics, making them an invaluable tool for both novice and expert welders. Leveraging extensive experimental insights and field data on these wires, this article examines their unique attributes and practical applications, cementing their importance in the welding domain.
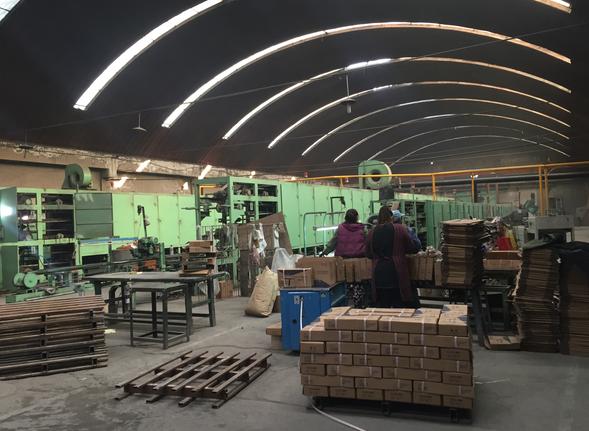
Manufactured with precision, stainless steel flux cored arc welding wires are designed to handle diverse welding challenges.
Unlike traditional wires, they encase a flux compound that produces high-quality welds with superior mechanical properties. The core flux composition is crucial, as it stabilizes the arc, controls the weld pool, and protects the molten metal from atmospheric contamination, thus enhancing weld integrity and strength.
Field experts consistently emphasize the superior arc stability these wires provide, which is paramount for achieving uniformity and precision in welds. In highly demanding environments, such as those encountered in aerospace or automotive industries, these wires offer the reliability and performance essential for safety-critical components. The carefully calibrated combination of alloys in flux cored wires ensures that the resulting welds possess exceptional corrosion resistance, a crucial factor for creating components exposed to harsh environmental conditions.
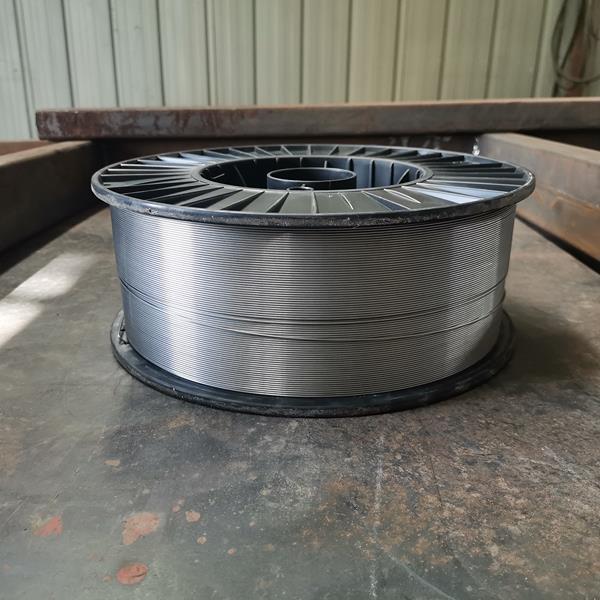
One of the significant advantages of stainless steel flux cored arc welding wires is their adaptability to various positions and orientations. This flexibility is particularly beneficial when tackling projects with complex geometries that require welding out of position. Expert welders often highlight their ability to create cleaner and more aesthetic weld beads in these scenarios, reducing post-weld cleaning and finishing time. Additionally, their ease of use significantly lowers the skill barrier, expanding accessibility to high-quality welding practices.
Trust in these welding wires has been built over years of rigorous testing and the development of sophisticated manufacturing processes. Leading manufacturers ensure that these wires meet stringent industry standards, such as AWS, EN, and ISO certifications, attesting to their quality and consistency. The wires are repeatedly tested for strength, ductility, and impact resistance under various conditions, providing users with the assurance that they can withstand the rigors of demanding welding tasks.
stainless steel flux cored arc welding wires
For tasks that demand efficiency and speed, stainless steel flux cored arc welding wires provide a critical advantage over solid wires. They facilitate faster deposition rates, which drastically reduces welding time without compromising quality. This efficiency translates into cost savings and increased productivity for industries reliant on extensive welding operations, such as shipbuilding or heavy machinery manufacturing.
Emerging trends in welding technology continue to see flux cored wires at the forefront of innovation. Developments in flux formulation aim to minimize fume emissions and spatter, addressing health and safety concerns traditionally associated with welding. Enhanced formulations improve deoxidizers and alloying elements, resulting in cleaner welds with minimal environmental impact.
For professionals committed to precision and excellence, understanding the nuances of different wire types, such as Rutile and Basic flux cored wires, can drastically improve outcomes. While Rutile wires are celebrated for their smooth arc characteristics and ease of use, Basic wires are preferred for their superior toughness and low temperature performance. Selecting the appropriate wire type is crucial for optimizing results based on the specific requirements of a project.
The decision to incorporate stainless steel flux cored arc welding wires into a welding workflow should be informed by a comprehensive evaluation of the project's demands and the wire's properties. Engaging with established vendors and consulting technical datasheets will ensure proper wire selection, further solidifying the manufacturer’s expertise and fostering trust in product reliability.
In conclusion, stainless steel flux cored arc welding wires stand as a testament to the transformative power of innovation within the welding industry. Their adoption demonstrates a commitment to not only advancing technological capabilities but also upholding standards of safety and quality. As industries continue to evolve, the role of these wires as a cornerstone in welding applications is set to expand, driven by their proven track record and adaptability to future challenges.