Choosing the right welding electrodes is crucial to achieving high-quality welds, and when it comes to using 4.0mm x 400mm welding electrodes, several factors contribute to their effectiveness in varying applications. Based on extensive real-world experience and authoritative resources in the welding industry, this article provides a comprehensive overview of the characteristics and applications of these specific electrodes, tailored to enhance your understanding and decision-making process.
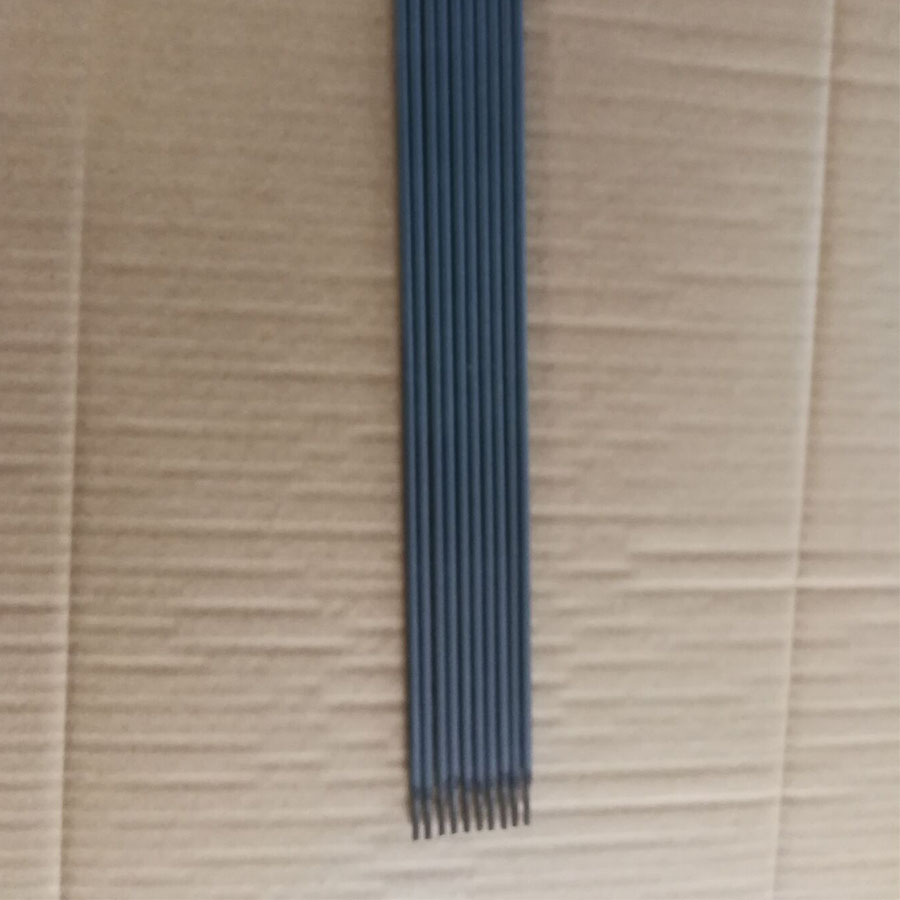
4.0mm welding electrodes are popular for heavy-duty welding tasks, providing robust and consistent results. The length of 400mm allows for extended welds before requiring an electrode change, optimizing productivity. These electrodes are commonly used in industries ranging from construction to shipbuilding, where strong and reliable joints are paramount.
The primary materials used in these electrodes usually include carbon steel or stainless steel, each suitable for different welding requirements. Carbon steel electrodes, for instance, are prized for their excellent tensile strength and ductility, making them ideal for structural applications. They are particularly notable for their capacity to withstand significant load stresses, which is essential in the construction of skyscrapers or bridges.
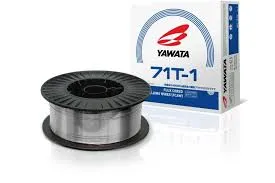
On the other hand, stainless steel electrodes offer enhanced corrosion resistance, crucial for welding projects exposed to harsh environments. Their application is widespread in industries such as chemical processing and marine operations, where long-lasting durability against moisture and corrosive substances is required. These electrodes facilitate smooth welding processes, reducing the risks of cracks and weak joints, thanks to their stable arc characteristics and low spatter generation.
welding electrodes 4.0mm*400mm
Professional expertise in electrode handling and usage is a cornerstone of achieving optimal results. Proper storage is pivotal to maintaining electrode quality; storing them in a dry, temperature-controlled environment prevents moisture absorption, which can compromise weld integrity. Furthermore, selection of the appropriate amperage, based on the electrode's diameter and material, is vital for effective penetration and minimal defects.
Authoritative resources emphasize the importance of choosing the correct welding machine parameters. A suitable current setting ensures consistent arc stability and quality weld beads. For 4.0mm electrodes, typical operating current ranges are advised between 150 to 200 amps; however, precise settings may vary based on the specific material being welded and the desired bead profile.
The experiential knowledge of seasoned welders reveals that electrode manipulation technique significantly influences the final weld quality. Employing a correct angle, maintaining a consistent speed, and ensuring adequate arc length are critical skills for producing strong, aesthetically pleasing welds. Practicing these techniques enhances efficiency and minimizes the need for secondary operations, such as grinding or re-welding, thereby saving time and resources.
In conclusion, the successful application of 4.0mm x 400mm welding electrodes hinges on a comprehensive understanding of their material properties, appropriate storage, handling practices, and precise technique. Possessing expertise in these areas not only strengthens the weld's structural integrity but also enhances the welder's craftsmanship and reputability within the industry. Trust in these principles is paramount, reflecting the authoritative insights derived from both field experience and professional literature, and consequently fostering the reliability and performance of the welding task at hand.