Choosing the right welding electrode can significantly impact the quality of your welds, especially when working with different types of metals and varying project requirements.
Two of the most commonly used welding electrodes are the 6013 and 7018, each offering unique properties and advantages. This article delves into their characteristics, their best applications, and what experienced welders say about them.
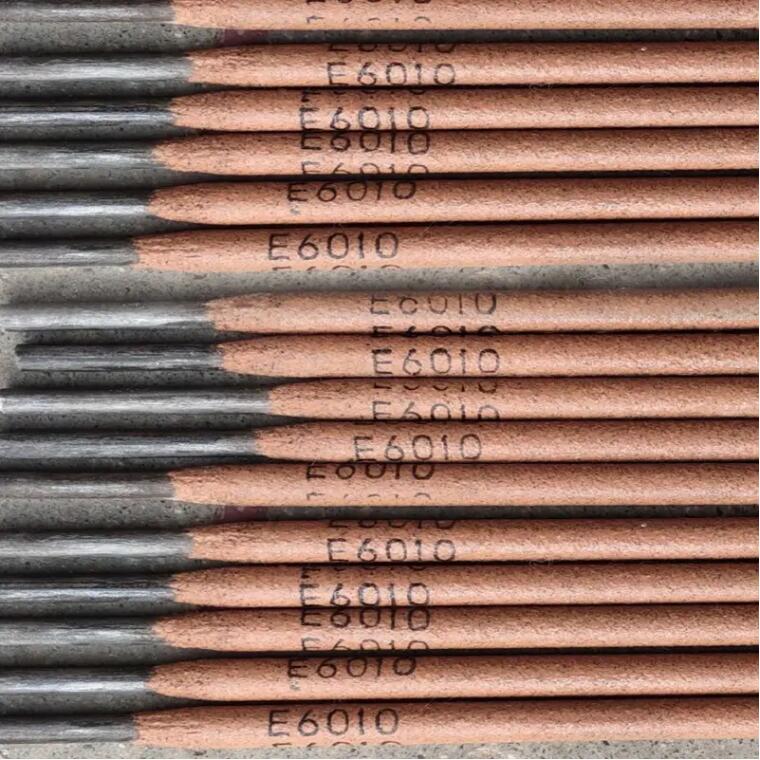
6013 welding electrodes are known for their versatility and ease of use, making them an excellent choice for beginners and professionals alike. Their general-purpose nature allows them to work effectively with mild steel in both AC and DC currents. Widely recognized for producing a smooth, stable arc, the 6013 electrode is ideal for applications requiring a medium to shallow penetration. This makes it particularly useful for light to medium fabrication projects, repairs, and sheet metal welding. The relatively mild slag system facilitates clean and straightforward welds, further establishing the 6013 as a go-to electrode for projects that do not demand high strength or impact resistance.
On the other hand, the 7018 welding electrodes offer superior mechanical properties, making them suitable for more demanding applications. Known as low-hydrogen electrodes, 7018 rods are preferred for structural welding tasks where durability, strength, and excellent impact resistance are paramount. These electrodes produce welds with minimal impurities, thanks to their flux coating that protects against atmospheric contamination. As a result, they are often employed in the construction of bridges, buildings, and pipelines, where high tensile strength and reduced susceptibility to cracking are critical. 7018 electrodes create a weld with smooth beads and a thoroughly protective slag, necessitating more skill but rewarding the welder with superior results.
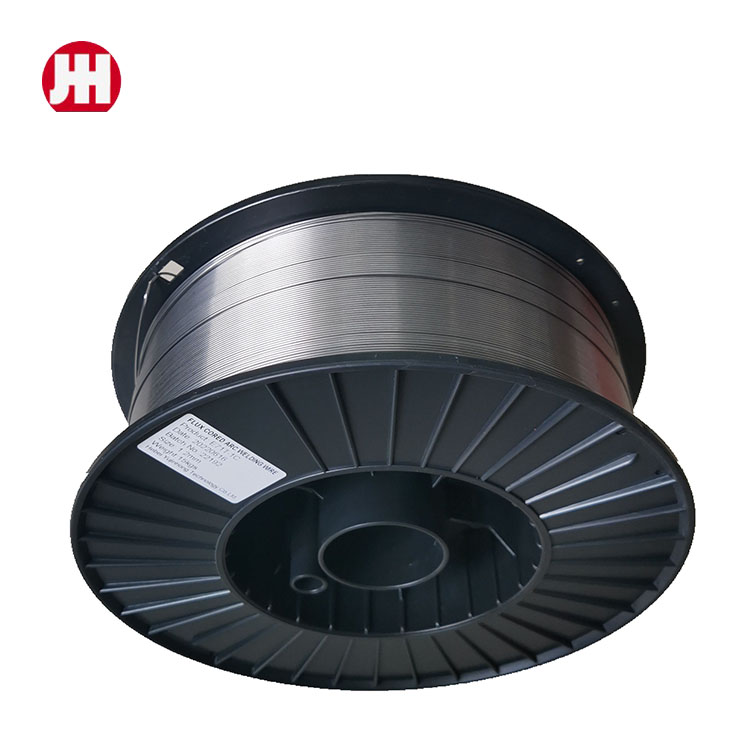
Expert welders appreciate the 7018 for its consistency, high-quality welds, and reliability in environments where failure is not an option. However, they emphasize the importance of proper storage conditions for these electrodes. Due to their low-hydrogen coating, 7018 rods must be stored in controlled environments to prevent moisture absorption, which can lead to hydrogen-induced cracking. Storage in a rod oven can maintain their optimal performance capabilities.
welding electrodes 6013 7018
In operation, both 6013 and 7018 electrodes require adjustments based on the specific project requirements. 6013 electrodes are praised for their forgiving nature, allowing them to perform well under less-than-perfect conditions, which is why they are favored in training environments and for DIY metal projects. Meanwhile, the 7018’s performance demands precise technique and conditions, but it compensates by providing welds with superior fatigue resistance and structural integrity.
A professional welder would advise beginners to hone their skills on the 6013 before moving on to the more challenging 7018, which necessitates a deeper understanding of welding intricacies. Training on 6013 will help novices master basic welding skills, such as electrode angle, speed, and heat management, before advancing to the more demanding terrain of 7018 welding.
Those in the welding industry place the importance of choosing the right electrode based on material composition, joint design, and the required mechanical properties of the end product. Regardless of your choice between 6013 and 7018 electrodes, understanding their characteristics and how they fit the project's specifications will be vital in achieving successful, strong, and durable welds.
In conclusion, selecting the appropriate welding electrode involves weighing considerations such as ease of use, strength requirements, and environmental conditions. Whether you opt for the user-friendly 6013 for routine repairs and light projects or the robust and reliable 7018 for structural applications, leveraging the unique strengths of each electrode will ensure you meet your welding goals efficiently. Prioritizing high standards in storage and handling practices, particularly with 7018 electrodes, further establishes trustworthiness in your welding practices, thereby guaranteeing safety, quality, and longevity in your work.