Metal welding rods are critical components in the welding industry, offering strength and versatility in various applications. Navigating the realm of metal welding rods can be complex due to the numerous options available. This discussion will delve into their characteristics, application processes, and selection criteria, focusing on delivering an experience-rich, expert-backed narrative that underscores authority and trustworthiness.
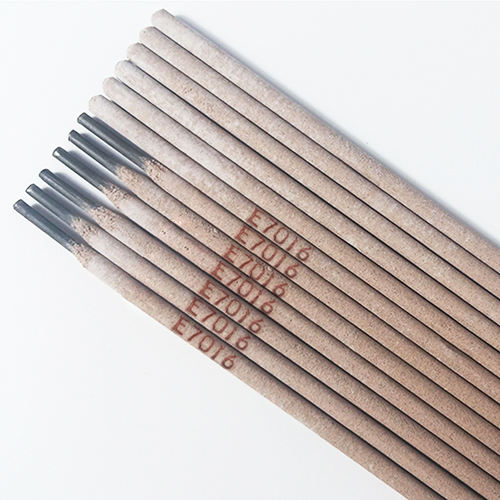
Understanding metal welding rods begins with recognizing the pivotal role they play in welding processes. Welding rods, or electrodes, are consumable materials that facilitate the joining of metal surfaces. Typically composed of a core wire and a flux coating, they not only conduct current to the workpiece but also provide filler metal to the joint, offering stability to the weld.
A key aspect of utilizing welding rods efficiently is understanding their classification. AWS (American Welding Society) classifies rods based on their material and positional capabilities. For instance, an E6010 welding rod indicates an electrode with a tensile strength of 60,000 psi and its usability in all positions due to the '1' in its classification. This knowledge empowers welders to choose the appropriate rod type for specific projects, ensuring optimal results.
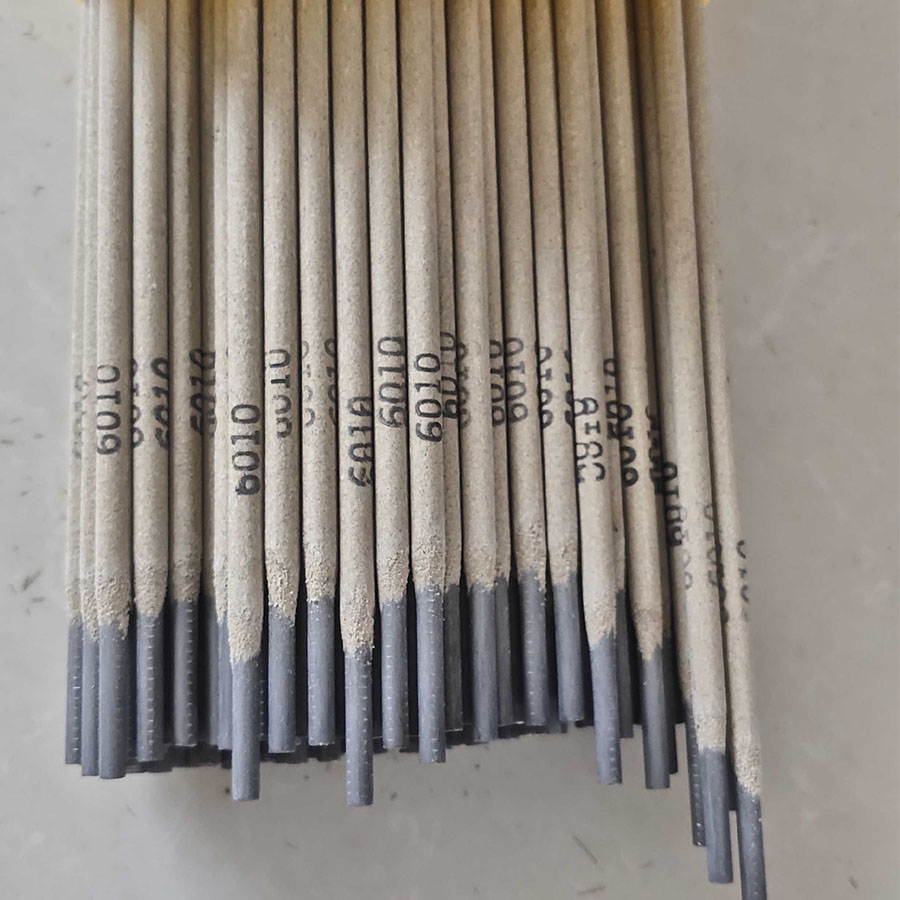
The proper selection of a welding rod hinges on factors such as base metal compatibility, welding position, and desired weld properties. For instance, mild steel welding often employs E6013 or E7018 rods depending on requirements for penetration and finish. Stainless steel welding, on the other hand, may require E308 or E316 rods to match the mechanical properties and corrosion resistance of the base materials.
metal welding rod
Beyond material selection, the operator’s skill level and the intended use environment profoundly influence the performance of welding rods. Professional welders with experience in different positions and environments can exploit the benefits of specific rod types to achieve seamless, robust joints. Moreover, expertise in tackling issues such as rod sticking, excessive spatter, or porosity defines the difference between novice and master welders.
The authoritative use of welding rods is further enhanced by understanding their maintenance and handling protocols. Proper storage—away from moisture and contaminants—safeguards the rods from damage, which could otherwise lead to weld defects. Keeping open packages sealed and maintaining an inventory rotation can preserve rod integrity, ensuring consistent results.
Trust in the application of welding rods is also a factor of adherence to safety standards and protocols. Welding is an inherently hazardous process that necessitates proper protective gear, such as helmets and gloves, shielding operators from the risks of molten metal and intense ultraviolet light. Compliance with industry safety regulations not only protects welders but also instills confidence in the quality of workmanship.
In conclusion, choosing and using metal welding rods requires a balanced blend of experiential knowledge, technical expertise, and strict adherence to guidelines. Each aspect, from classification to storage, plays an integral role in achieving and sustaining high-quality welds. Thus, investing in understanding the nuances of welding rods and refining skills consistently can propel both novices and seasoned practitioners toward exceptional proficiency and craftsmanship in the art of welding.