Welding wire electrodes play a critical role in ensuring the effectiveness and quality of welding operations across various industries. These consumables are essential in creating strong bonds between metal components, thereby contributing to the structural integrity and durability of the final product. Selecting the right welding wire electrode involves a nuanced understanding of materials, types, and applications in which they are best suited.

For professionals looking to optimize their welding processes, understanding the composition and function of welding wire electrodes is imperative. Primarily, these electrodes are chosen based on the welding method being employed, such as MIG, TIG, or flux-cored arc welding. Each of these processes offers distinct advantages and requires specific types of electrodes to achieve optimal results.
The expertise required to choose the right welding wire electrode is built on the understanding of the materials to be welded. For instance, when working with stainless steel, an electrode with a matching or higher grade alloy may be necessary to prevent corrosion and ensure a robust weld. On the other hand, when dealing with aluminum, selecting a wire that provides precise control and a clean finish is paramount, often necessitating an extensive background in metallurgical properties and welding dynamics.
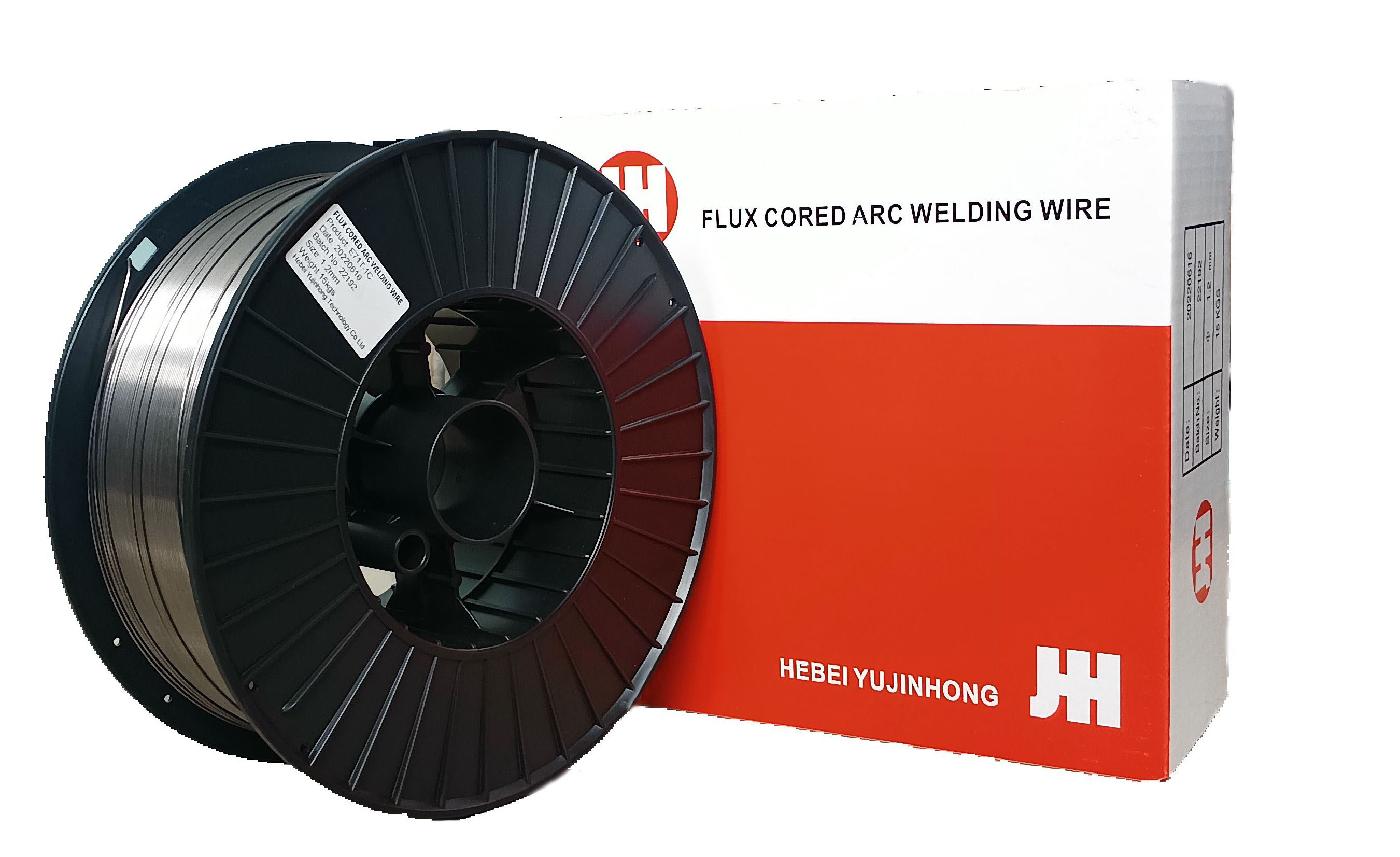
From an authoritative perspective, optimum weld quality is not just about the electrode's material but also about its diameter, coating, and strength. Larger diameter electrodes are often recommended for heavy-duty applications as they can bear higher current, while various coatings can influence penetration and spatter levels. Recognized industry standards, such as those set by the American Welding Society (AWS), offer guidelines that ensure consistency and reliability across welding projects.
welding wire electrodes
Trustworthiness in the selection and use of welding wire electrodes comes from adherence to safety and reliability protocols. Thorough testing and certification from reputed organizations ensure that these consumables meet the stringent demands of varied welding environments. This not only fosters confidence in their performance but also aligns with industry best practices.
To truly elevate the welding process through the use of wire electrodes, practical experience is invaluable. Veterans in the field often possess hands-on insights that are pivotal for fine-tuning welding techniques and achieving superior results. For instance, understanding how different wire feed speeds and voltage settings impact the weld pool can significantly enhance the welding efficiency.
Moreover, establishing a consistent record of successful projects using specific electrodes builds an experiential knowledge base. It allows professionals to anticipate and correct potential issues before they arise, thus preserving project timelines and enhancing the overall quality of the weld. Innovative welding solutions, such as hybrid processes combining different techniques, further exemplify the depth of expertise needed not only to implement but also to understand the advantages and limitations of such advancements.
In conclusion, mastering the use of welding wire electrodes requires a blend of theoretical knowledge, practical experience, and strict adherence to industry standards. It is a domain where continuous learning and adaptation to technological innovations can lead to notable improvements in welding performance and output quality. For those seeking to leverage these tools effectively, the journey is as much about refining one's understanding of the material and processes involved as it is about applying this knowledge to create durable and reliable welds in diverse applications.