Navigating the vast world of welding materials and tools, one cannot overlook the significance of flux core welding wire, a critical element that caters to a wide spectrum of industry applications. As an essential consumable for flux-cored arc welding (FCAW), this wire revolutionizes the way welders approach their craftsmanship by offering efficiency, versatility, and cost-effectiveness. Delving into the intricacies of flux core welding wire provides valuable insights that can enhance both novice and seasoned welders' understanding of this indispensable tool.
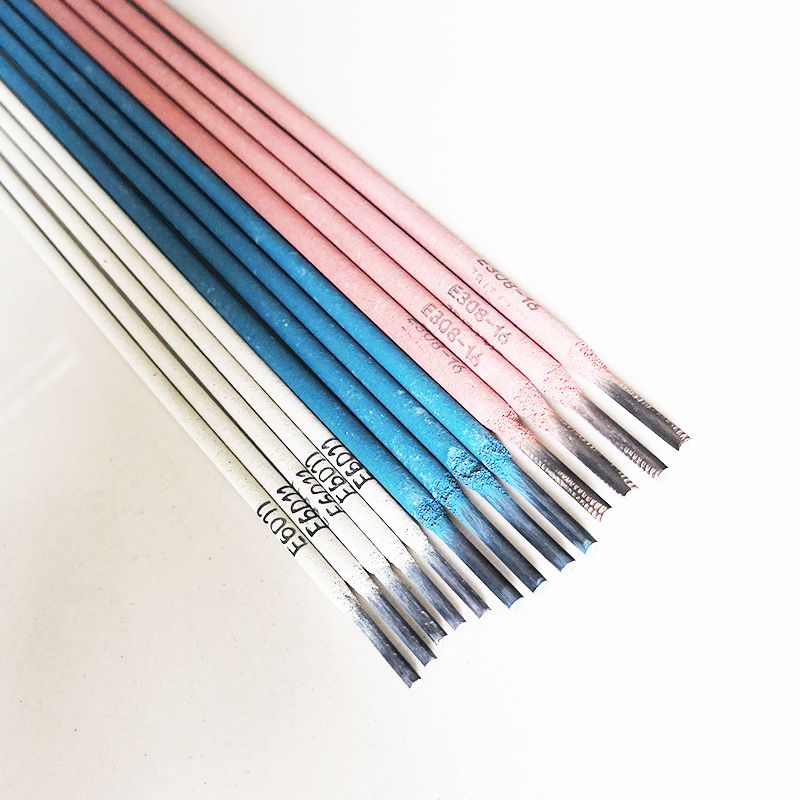
Flux core welding wire stands out due to its unique construction. Unlike solid wire used in MIG welding, flux core wire is hollow and filled with a flux compound. This flux serves a pivotal role; it acts as a shield for the weld pool against atmospheric contaminants. By keeping impurities like nitrogen and oxygen at bay, the flux ensures a clean and robust weld, which is especially crucial in outdoor or drafty conditions where shielding gas might be blown away. The result is a perfect blend of stability and strength—qualities that every welding professional seeks.
Professional welders often laud flux core welding wire for its adaptability across various welding situations. Its ability to penetrate thick materials without the need for an external gas supply makes it ideal for outdoor projects or when welding in confined spaces. This self-shielding feature renders it invaluable in sectors such as construction and shipbuilding, where environmental conditions are unpredictable and demand robust, reliable joints.
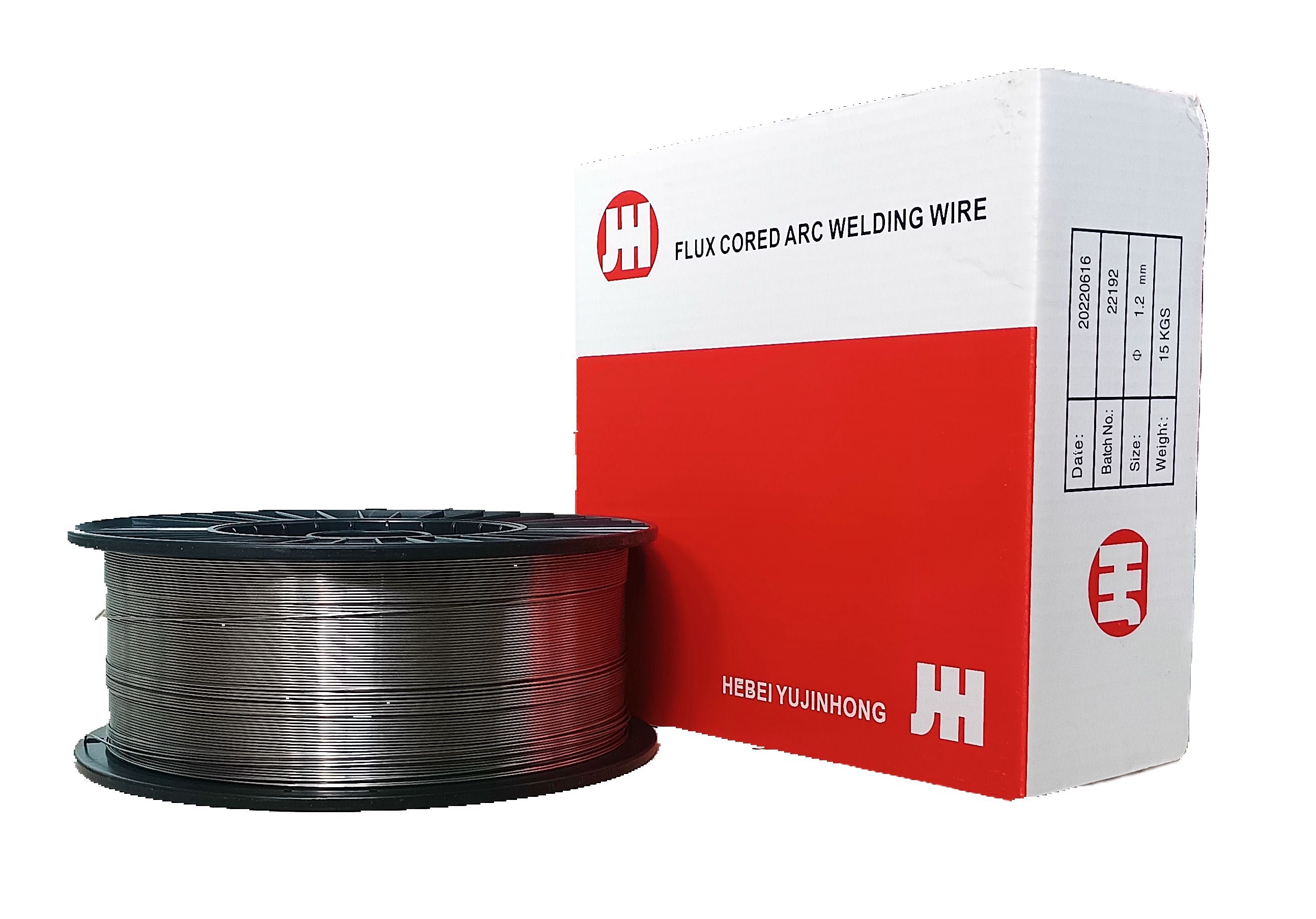
One of the strongest endorsements for the efficacy of flux core welding wire comes from its performance on thinner metals as well. Despite its prowess in tackling heavier structures, this wire variant delivers precision and control when working with lighter gauges, minimizing burn-through risks. This breadth of application underlines its necessity in every welder's arsenal, equipping them to handle a diverse array of tasks with confidence.
flux core welding wire
To maximize the benefits of flux core welding wire, understanding the different types available is paramount. From E71T-1, which is optimal for flat and horizontal welding positions, to E71T-8 recommended for all-position welding, each type offers distinct properties tailored for specific challenges. Selecting the appropriate wire entails considering factors such as material thickness, welding position, and the specific requirements of the task at hand.
From an expertise standpoint, manufacturers continuously refine the formulations of flux core wires to enhance performance attributes such as spatter resistance, weld bead appearance, and overall weld soundness. Engaging with reputable suppliers and staying informed about the latest advancements can provide welders with a competitive edge, ensuring their projects meet industry standards and client expectations.
Investing in high-quality flux core welding wire from trusted brands not only enhances operational efficiency but also promotes weld integrity, supporting longer service life and safety. The reliability of these products stems from rigorous testing and strict adherence to international quality standards, reinforcing their status as a trusty companion for professional applications.
In conclusion, flux core welding wire's distinct advantages make it an indispensable resource in the toolkit of any serious welder. Its versatility, coupled with expert engineering, ensures it remains a cornerstone in welding technology. By embracing this tool's capabilities, welders can guarantee superior results that meet the demanding criteria of modern-day craftsmanship. The judicious selection and application of flux core welding wire stand as a testament to a welder's commitment to quality and excellence.