In the intricate world of welding, the choice of consumables is pivotal to achieving high-quality results. Among the numerous options available, the MIG flux core welding wire stands out for its exceptional versatility and convenience, particularly for professionals seeking to optimize their welding outcomes. Drawing from years of experience in the welding industry, the following insights underscore the profound impact of this wire type on both performance and productivity, establishing it as a preferred choice for many experts.
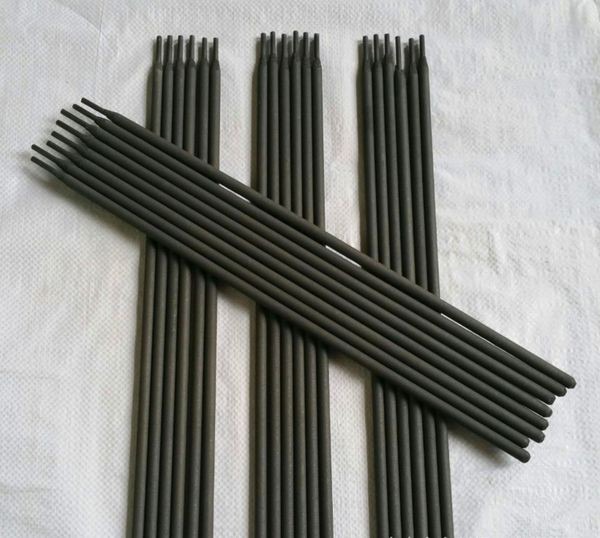
The MIG flux core welding wire is engineered to deliver superior welds even in conditions that might challenge other consumables. Its design integrates a flux-filled core, which not only facilitates the throughput of the welding process but also enhances the consistency with which weld deposits are made. This particular configuration allows the wire to self-shield the arc, effectively reducing the need for an external shielding gas. Consequently, welders can operate smoothly even in outdoor or drafty environments where gas dispersion could otherwise compromise weld integrity.
For professionals keen on minimizing downtime and maximizing efficiency,
the MIG flux core welding wire emerges as an indispensable tool. Its user-friendly nature significantly reduces the preparatory work typically required with traditional MIG welding. By eliminating the dependency on a shielding gas, welders can swiftly transition between projects and adapt to exigent on-site conditions. This flexibility not only enhances workflow but also aligns with industry demands for scalable solutions.
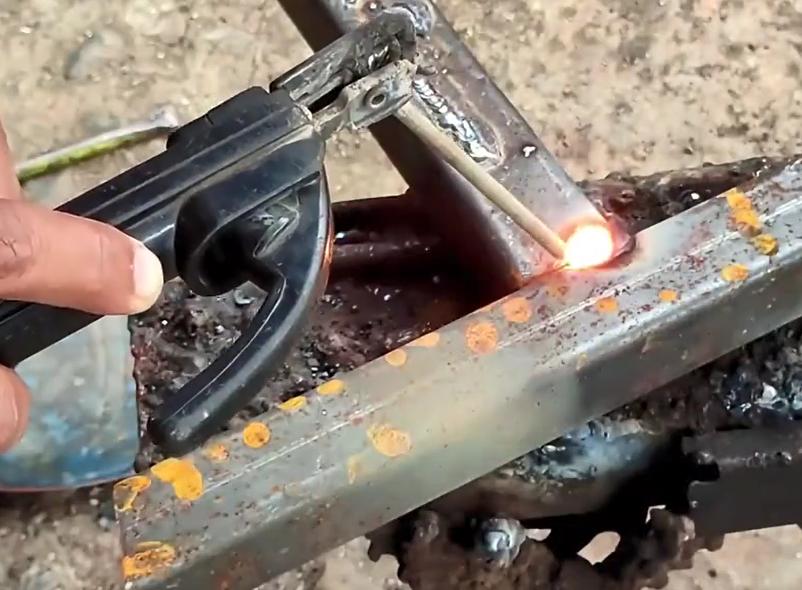
When assessing the long-term benefits of employing the MIG flux core welding wire, it's essential to consider its impact on material penetration and bead appearance. The wire's formulation is meticulously crafted to optimize heat concentration, ensuring deeper penetration and stronger bonds between metal surfaces. This feature is particularly advantageous when working with thicker sections of steel, where robust welds are paramount. Additionally, the flux core's properties aid in reducing splatter, leading to neater bead appearances and reduced post-weld cleaning time.
mig flux core welding wire
An often overlooked yet crucial aspect of choosing the MIG flux core welding wire is its applicability across diverse materials and thicknesses. This adaptability renders it invaluable for professionals who must navigate a range of welding scenarios, from automotive fabrication to structural projects. By accommodating various base metals, such as carbon steel and stainless steel, the wire offers a comprehensive solution to ensure welders are well-equipped to tackle any challenge with confidence.
In terms of expert recommendations, leveraging the MIG flux core welding wire is particularly beneficial in scenarios where welding needs to be conducted outside a controlled factory environment. Its capacity to withstand environmental variables like wind and moisture makes it a go-to choice for fieldwork. Moreover, its inherent properties facilitate lower consumption rates, enabling cost-efficiency without compromising quality—an aspect that resonates deeply with businesses focused on optimizing resource use.
Furthermore, bolstering trustworthiness, the MIG flux core welding wire's performance is backed by rigorous industry testing and certifications. It conforms to international standards, which guarantees its reliability and safety, enhancing trust among clients and end-users. Professionals opting for this wire can be confident in its capability to meet both present-day industrial challenges and future welding advancements.
In conclusion, for both seasoned welders and novices aiming to refine their technique, the MIG flux core welding wire offers a seamless blend of efficiency, adaptability, and quality assurance. Its distinctive characteristics not only streamline the welding process but also align with the evolving expectations of modern manufacturing environments. As welding technologies continue to advance, embracing tools like the MIG flux core welding wire will be crucial for staying at the forefront of the industry, ensuring both superior results and sustained operational success.