Spot welding wire, a critical component in the realm of automated manufacturing processes, serves as a cornerstone in producing high-quality metal joints. This specialized wire is designed to withstand the rigors of the spot welding process, ensuring reliable and consistent results in a variety of applications, from the automotive sector to intricate electronic assemblies.
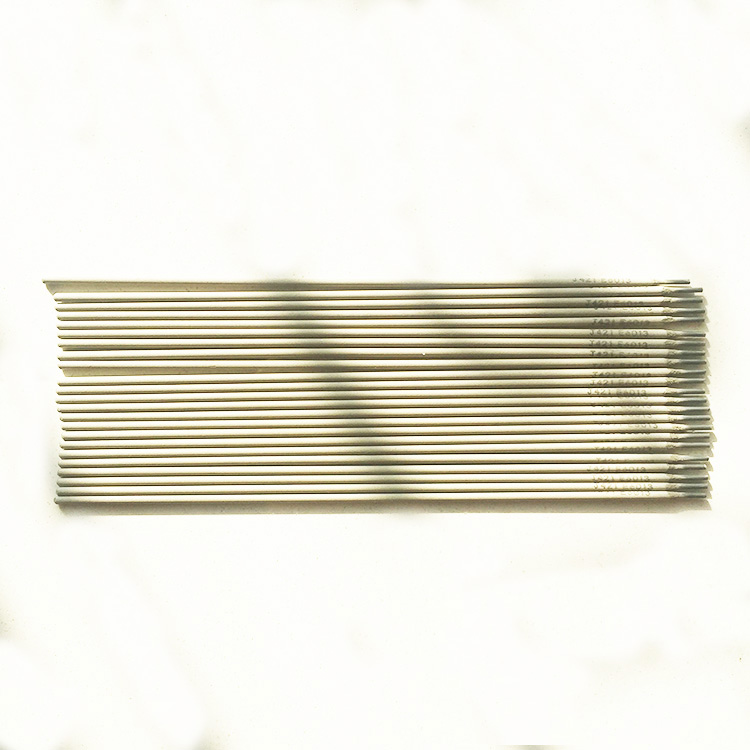
Drawing from extensive industry experience, the choice of spot welding wire fundamentally determines the strength, durability, and precision of the welds produced. It is imperative to select the appropriate wire type based on the material being joined, the welding equipment, and the specific requirements of the end application. Commonly used materials include copper, brass, and specialized alloys, each offering distinct advantages for various welding needs. Copper offers excellent thermal and electrical conductivity, making it ideal for high-speed and high-volume production lines, particularly in the automotive industry. Brass and other alloys introduce added corrosion resistance and tensile strength, suitable for challenging environmental conditions or for joining dissimilar metals.
In terms of expertise,
understanding the nuances of wire diameter and coating can significantly impact welding efficiency and quality. Wire diameter affects the amount of heat generated during the welding process; smaller diameters reach higher temperatures more quickly but can also burn through thinner materials if not controlled properly. Coatings such as zinc or tin can enhance electrical conductivity, improve corrosion resistance, and reduce wear on the welding equipment, promoting longer operational life and reducing downtime for maintenance.
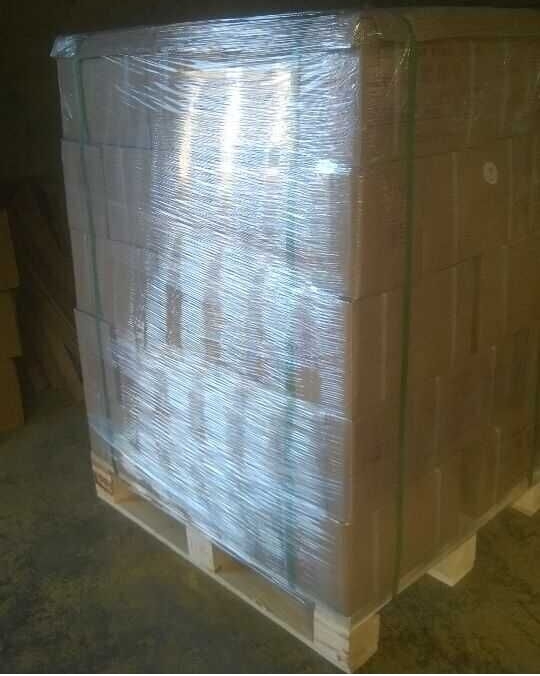
The authoritativeness of spot welding wire is evidenced by its critical role in automotive assembly lines which require precision and reliability. Automotive manufacturers highly regard certain brands that consistently deliver high-quality wire, ensuring that welds hold under extreme conditions such as high stress, temperature fluctuations, and exposure to the elements. The ability of a spot welding wire to maintain its integrity over the lifespan of a vehicle is a testament to its quality and performance.
spot welding wire
Trustworthiness in selecting spot welding wire is built through rigorous testing and adherence to industrial standards such as those outlined by the American Welding Society (AWS) or the International Organization for Standardization (ISO). Compliance with these standards ensures that the wire can withstand specific load and fatigue conditions, providing peace of mind to manufacturers and end-users alike. Reviews and testimonials from reputable users in the industry can further reinforce the credibility of a particular wire brand or type, guiding new users toward making informed purchasing decisions.
Beyond these technical considerations, the economic impact of utilizing high-quality spot welding wire cannot be overlooked. While premium wires may entail higher initial costs, their ability to minimize defects, reduce machine wear, and increase production speeds can lead to a significant increase in overall operational efficiency and cost savings in the long run. Companies that invest in superior spot welding wires often find that the reduction in rework and improved product quality more than justifies the upfront expense.
In conclusion, the selection and application of spot welding wire are pivotal in achieving superior weld quality and manufacturing efficiency. Leveraging real-world experiences, a robust understanding of material properties, strict adherence to authoritative standards, and a commitment to quality can collectively enhance the reliability and performance of the final products.