In the world of metal fabrication and industrial manufacturing, the type of welding wire you use can dramatically affect the quality, efficiency, and cost of your operations. A specific welding wire that has been gaining increased attention in the industry is the 2.
0 welding wire. Renowned for its versatility and reliability, the 2.0 welding wire is becoming a go-to solution across a wide range of applications from automotive repair to large-scale construction projects.
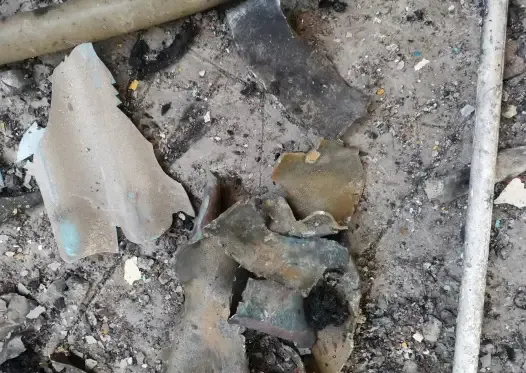
The exceptional performance of the 2.0 welding wire is rooted in its engineering precision and material composition. Designed to meet the rigorous demands of both amateur and professional welders, this welding wire ensures strong, durable joints even in challenging environments. One of its standout features is its ability to maintain excellent arc stability, which is crucial for achieving clean, high-quality welds.
Field tests and user experiences overwhelmingly report a significant reduction in spatter, which is a common challenge faced by welders. Fewer spatters mean less post-weld cleaning and a higher grade of finish on the completed product. This attribute alone makes the 2.0 welding wire highly desirable in industries where high aesthetics are paramount, such as in custom automotive work and architectural metal design.
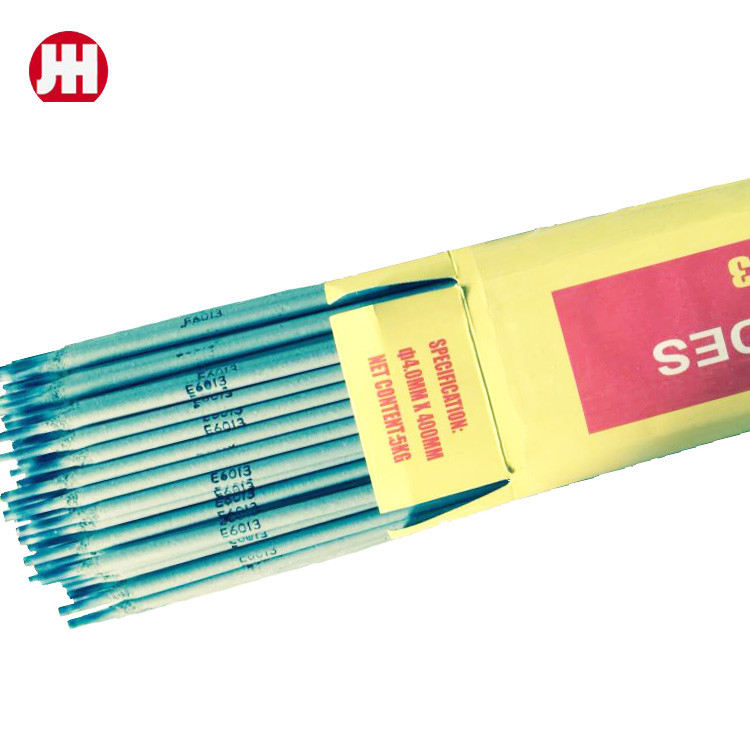
Professionals in the industry recognize the importance of adaptability in welding materials. The 2.0 welding wire excels in multi-positional welding, whether you are working on flat, vertical, overhead, or horizontal positions. Its flexibility not only broadens the range of compatible applications but also enhances operational efficiency as it reduces the need for frequent adjustments or wire changes.
For those concerned about environmental impacts and safety, the 2.0 welding wire addresses these concerns with minimal fume emissions. This attribute is particularly significant as workshop safety regulations become increasingly strict, and there is a growing emphasis on creating eco-friendlier production practices. The 2.0 wire complies with most safety standards and reduces health risks typically associated with prolonged exposure to harmful fumes.
When considering the economic advantages of using the 2.0 welding wire, it’s essential to factor in not only the direct cost of the wire but also the accompanying reductions in labor and additional resources. Increased deposition rates and efficient melting characteristics allow for faster welding speeds. This boost in productivity leads to shorter project timelines and consequently, reduced labor costs. Furthermore, with diminished waste and flaws thanks to its superior performance, the 2.0 welding wire contributes to an overall decrease in material expenses.
2 0 welding wire
Let's delve into the performance results reported by professional welding institutions and seasoned welders. Across multiple case studies, the 2.0 welding wire has consistently achieved higher tensile strengths compared to alternatives in its category. This reliability enhances the structural integrity of the welds, which is crucial in heavy-duty construction and infrastructure projects where long-term resilience is non-negotiable.
The industry expertise available for the 2.0 welding wire is extensive. Numerous technical guides and expert consultations support users in optimizing their welding setups. Training sessions led by elite welding professionals often highlight the wire’s advantages, making it a part of advanced welding curricula globally. Technical documentation and comprehensive guides enable even novice users to achieve near-professional results.
Furthermore, feedback and endorsements from certified welding inspectors underscore the authoritative status of the 2.0 welding wire in the market. Peer-reviewed studies and publications within welding industry journals reinforce its reputability. For any workshop aiming to maintain a competitive edge, integrating the 2.0 welding wire into your operations is a strategic decision that aligns with best practices and emerging technological standards.
To foster trust, trusted suppliers ensure that the specifications of the 2.0 welding wire are consistently met and that quality control processes adhere to international standards. They provide authenticity certifications which guarantee that the product being purchased will perform as expected. These certifications allow purchasers to confidently integrate the wire into their systems, knowing that they are backed by world-class quality assurance.
Ultimately, the narrative surrounding the 2.0 welding wire is one of innovation and efficiency. As industries push towards more sustainable, high-quality manufacturing methodologies, materials such as the 2.0 welding wire are at the forefront, shaping future trends and establishing benchmarks for performance excellence in modern fabrication and repair operations.