A welder is an extension of the equipment, and tools and products are available that streamline the job and make the welding process easier. Using equipment with fewer points of failure and simplified maintenance can speed up welder training, help welders confidently build their skill set, and ultimately increase productivity and efficiency.
Configure the Right MIG Gun. Selecting and, in some cases, configuring a MIG gun for the needs of a specific application can result in greater productivity, enhanced operator comfort, and improved weld quality. Knowing the application and the specific welding parameters of the job (wire size, amperage, arc-on time), a welder can select a gun that meets the job needs. Not only do these variables impact amperage, but they can affect the ergonomics that will best suit the gun. Depending on the requirements, the gun may require a different neck (fixed or rotatable in multiple lengths and angles) or handle style (straight or curved) to achieve both comfort and quality.
Use the Correct Consumables.
The benefits include longer contact tip life, less rework, and simplified maintenance.
A longer tip life means that:
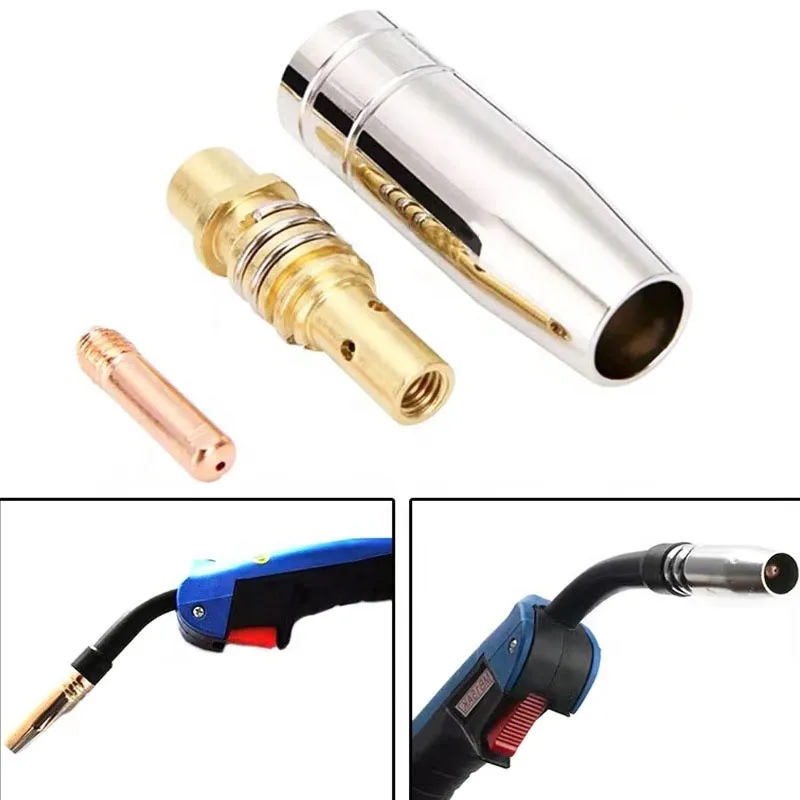
Implementing a compatible consumable system has considerable advantages. It will enhance productivity, lower costs, and boost welder confidence all while streamlining inventory management and minimizing errors.
- Contact tip replacement frequency is reduced.
- Contact tips are 60% buried within the diffuser for less exposure to the heat of the weld.
- Mating tapers on both tip-to-diffuser and diffuser-to-neck connections allow for good electrical conductivity.
- Shielding gas cools the contact tip tail.
Meanwhile, welders will benefit from less rework and ease of maintenance because:
- Coarse-threaded contact tips speed up tip replacement.
- The steel-retaining ring on the diffuser helps keep the threaded nozzle in place during use and cleaning.
Additionally, the same system was specifically designed to address liner trim length errors, resulting in error-proof liner replacement without any measuring required. The dual-locked liners are locked and concentrically aligned to both the contact tip and the power pin, optimizing wire feeding and eliminating welding liner misalignment gaps.
Advanced Welding Liner Technology. Because one of the most common issues with a gun is feedability, the industry is beginning to manufacture welding liners with an updated profile and galvanized coating that make it easier for the wire to feed through the torch. Even stainless steel and aluminum wires, which are notorious for being hard to feed, can move through the liner with ease. The shape of the liner shields the wire material against challenging welding environments where humidity and dampness can negatively affect the feed. Lastly, the enhanced coil profile reinforces the liner’s rigidity, optimizing wire support.
Automatic Welding Parameter Setup. When welders need to dial in weld parameters like wire diameter and material thickness, there is a technology that automatically sets the proper wire feed speed and voltage. Not only is this a time-saver, but it also helps ensure the right settings for effective welding. This gives an operator of any skill level more confidence right from the start for welding that’s truly made easy.
Small adjustments can have a ripple effect that amounts to big gains and losses. Such is the case in MIG welding, too, where tiny tweaks to the liner length and cross-checks on consumables can help eliminate cumbersome and costly delays and rework. To augment those key adjustments, equipment innovations double down on the ease-of-use factor and facilitation of quality welds. Combine the two, and welders of all experience levels will be able to fine-tune their craft for optimal output.