In the world of welding, choosing the right electrode can significantly influence the quality, durability, and strength of a joint. The welding electrode 7016 stands out in the array of options available to seasoned welders, exhibiting specific characteristics that cater to particular welding needs and applications.
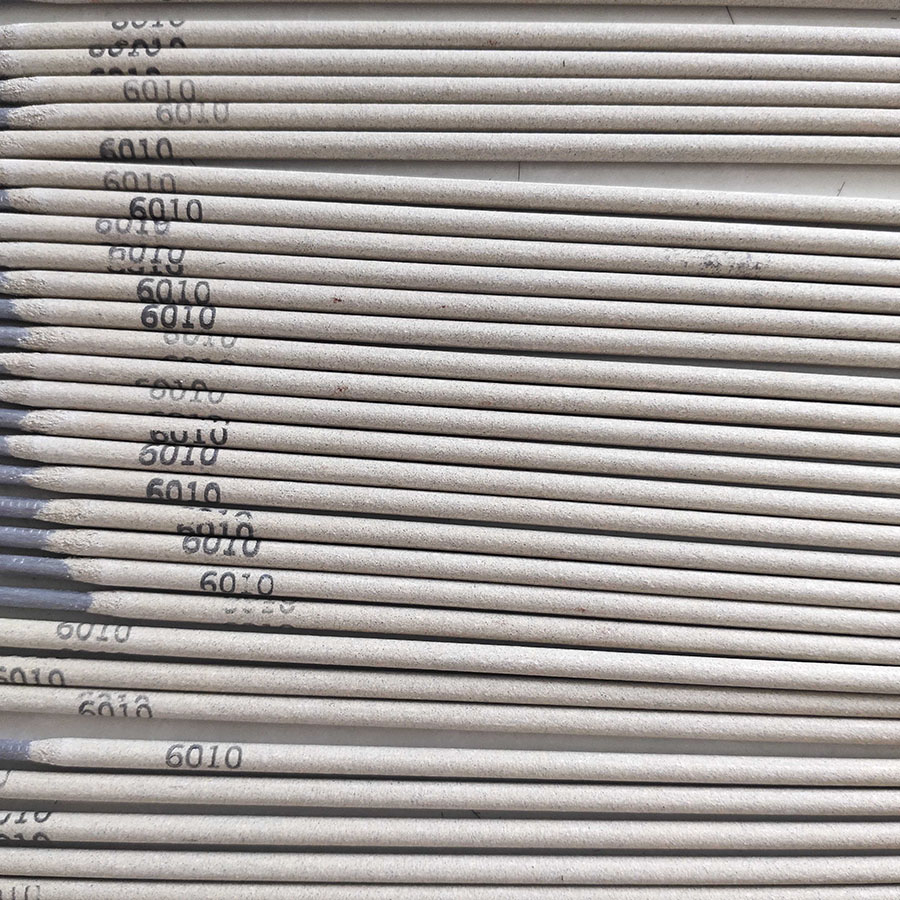
Welding is as much an art as it is a science, and the importance of using the correct electrode cannot be understated. The 7016 electrode is a low hydrogen potassium type that is engineered for all-position welding, particularly suited for situations where low spatter, smooth arc action, and minimal clean-up are required. This makes it the ideal choice for structural welding, where precision and efficiency are paramount.
One of the standout features of the 7016 electrode is its low hydrogen content. Why is this important, you ask? Hydrogen is a small atom that can easily diffuse through metal. The presence of hydrogen in welding can lead to hydrogen embrittlement, a phenomenon that results in the weakening of the welded joint. This condition can cause the metal to become brittle and crack over time, which is particularly detrimental in constructions or setups where stress tolerances are already high. The use of a low hydrogen electrode like the 7016 greatly mitigates this risk, ensuring that the welds maintain their integrity over their intended lifespan.
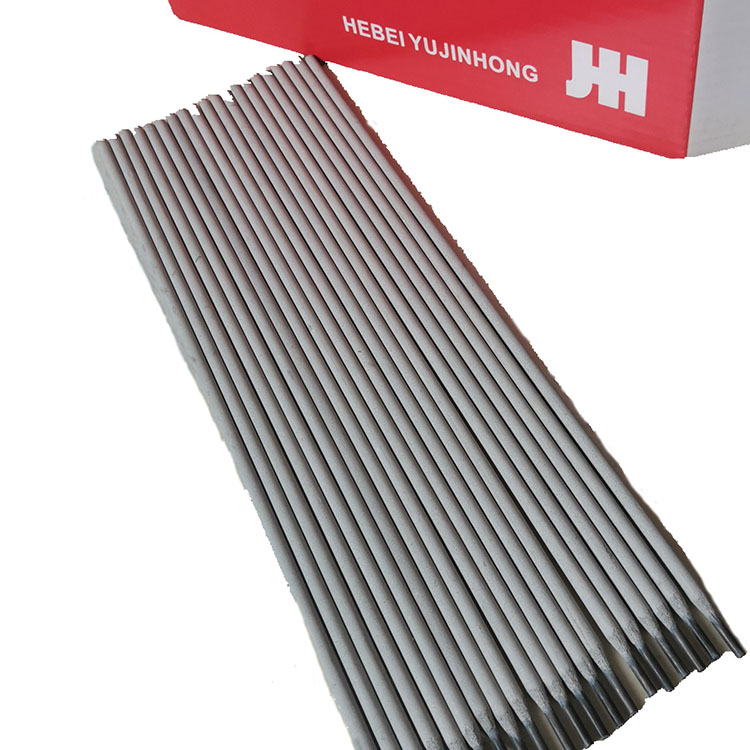
The 7016 electrode also exhibits excellent mechanical properties, making it versatile across a wide range of steel applications. It is especially effective with high-tensile strength steel, where the mechanical demands are rigorous. Its composition allows for deep penetration and a strong weld profile, even in less-than-ideal conditions. Whether you're dealing with a complicated joint configuration or any uncertainty in the metal's surface conditions, the 7016 provides a reliable solution.
From a practical perspective, the ease of use associated with the 7016 electrode cannot go unnoticed. Because it supports all-position welding, it offers flexibility and adaptability, essential characteristics in a field environment where conditions are ever-changing. This feature is particularly beneficial for on-site work, where welders face the unpredictability of their working angles and need an electrode that can perform under varying conditions.
welding electrode 7016
The electrode also boasts a relatively stable arc, which contributes to reducing the amount of spatter generated. This means less time spent on post-weld cleanup, leading to increased efficiency and less resource expenditure—an undeniable benefit in both time and cost for businesses and individual contractors alike.
In terms of its expertise and authoritativeness in the welding arena, 7016 has earned a reputation for reliability and performance. Its formulation is often the result of rigorous testing and standards compliance, ensuring it meets high industry requirements for safety and performance. It is typically recommended by industry professionals and standards bodies when a robust, high-quality weld is required.
Of course, welding is not devoid of challenges, particularly when factors such as ambient weather conditions or surface contamination come into play. However, the 7016 electrode excels in creating strong bonds, even in less than ideal conditions. This reliability builds trust among welding professionals, solidifying the 7016's place as a staple in their toolkit.
In conclusion, the 7016 welding electrode stands as a testament to the importance of engineering and material sciences in creating durable, efficient, and safe welding solutions. Its low hydrogen content, adaptability to different welding positions, and robust mechanical properties make it a preferred choice among professionals who value reliability and quality in their welding operations. Using the 7016, welders not only secure stronger joints but also reinforce their reputation for delivering safe and resilient construction.