Selecting the right welding rod can significantly impact the quality of your welding projects.
The welding rod 3.2 mm diameter, often considered versatile, offers several advantages for different welding applications. Here, we explore its benefits, providing insights grounded in professional expertise and experience, offering a reliable guide for both novice and experienced welders.
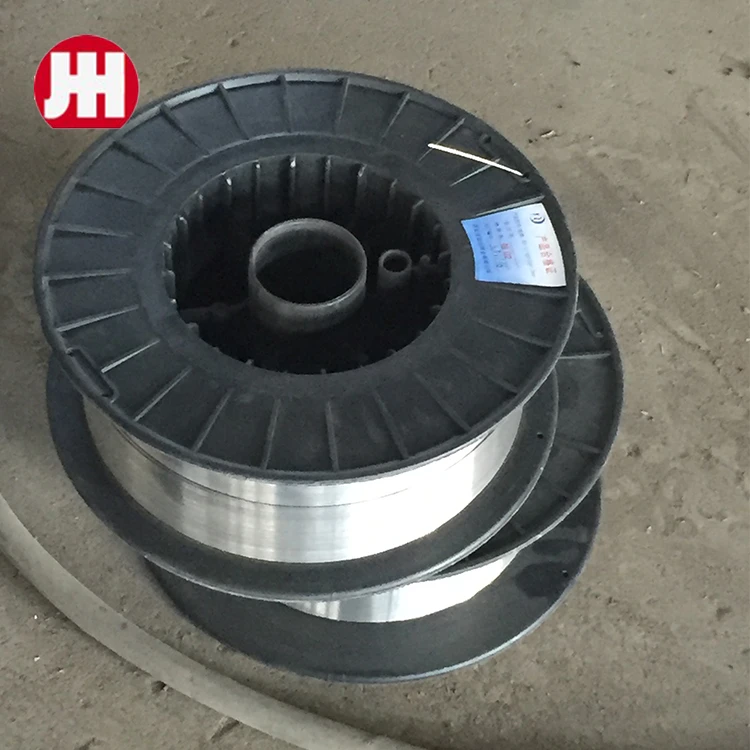
Firstly, understanding the composition and application of the 3.2 mm welding rod is crucial. Typically, these rods come with a variety of base materials like mild steel, stainless steel, or special alloys, each catering to distinct welding requirements. For instance, mild steel rods are suitable for welding materials with similar composition due to their excellent ductility and strength. Their reliability is particularly appreciated in structural applications where joint integrity is paramount.
Furthermore, the 3.2 mm diameter makes it an ideal choice for medium to heavy-gauge metal and is perfect for welding tasks requiring a balance between precision and strength. Its size provides an excellent current carrying capacity that melts the rod evenly, creating seamless joints. The resulting welds are smooth and exhibit fewer defects like slag inclusions or undercuts, promoting structural durability.
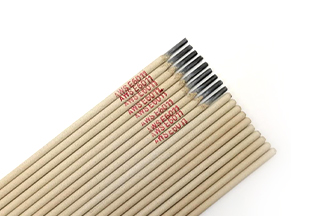
Another significant advantage is the rod's adaptability across various welding positions, including horizontal, vertical, and overhead welds. This flexibility is essential for projects involving complex structures or awkward angles, as it ensures consistent quality in every joint. Professional welders often rely on 3.2 mm rods for repair work or when achieving a polished finish is non-negotiable.
In terms of expertise, using a 3.2 mm rod requires understanding optimal amperage settings. Typically operating within a range of 90-140 amps, these rods offer a smooth arc that promotes easy control, minimizing sputtering. For individuals honing their craft, mastering the amperage settings with a 3.2 mm rod can significantly enhance welding proficiency, leading to better outcomes in diverse applications.
welding rod 3.2
Moreover, the selection of the right electrode coating is imperative. Coatings such as cellulose, rutile, or basic flux have different effects on penetration and mechanical properties of the finished weld. For those seeking deep penetration, cellulose-coated rods are preferable, whereas rutile coatings are ideal for smooth, aesthetically pleasing welds due to their easy slag removal and steady arc.
Trustworthiness of the 3.2 mm welding rod is also linked to its widespread use across multiple industries. From construction to automotive, the rod is a preferred choice due to its adaptability and robustness. Many industry practitioners endorse these rods for critical welding tasks due to the reliability they offer. Incorporating feedback from various industry experts into your approach when selecting this rod size can reduce error rates and increase joint reliability.
Experienced welders often emphasize the importance of proper storage and handling of welding rods to maintain their effectiveness. Moisture and contamination can compromise rod integrity, adversely affecting weld quality. Storing rods in a dry, sealed container will prevent absorption of moisture, ensuring consistent performance.
To conclude, the 3.2 mm welding rod stands out as a resourceful tool in a welder's arsenal, balancing versatility, reliability, and control. By leveraging the knowledge shared by industry experts and backed by extensive experience, one can achieve superior weld quality and project success. Selecting the right rod composition, adjusting the appropriate settings, and maintaining storage standards are critical factors that contribute to a successful welding experience.