Understanding the role of welding wire ER70S-6 in the welding process is crucial for professionals seeking both quality and efficiency in their work. With welding being a sophisticated skill requiring precision and expertise, choosing the right materials can make a significant difference in the outcome of any project. ER70S-6 is a commonly used welding wire that more often than not becomes the first choice for many welders across various industries. But what makes it stand out?
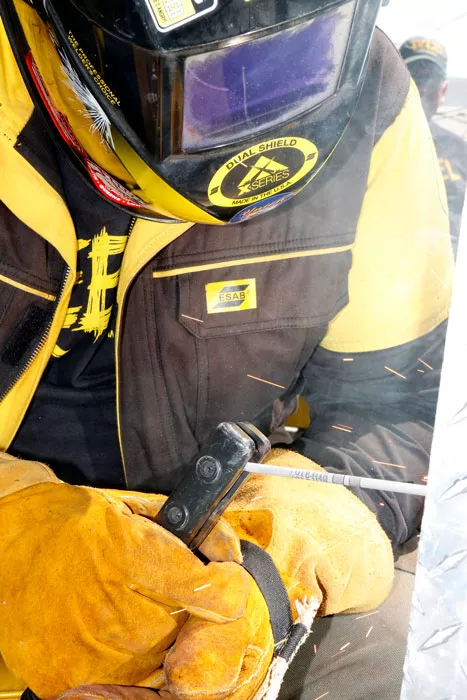
ER70S-6 is a versatile welding wire specially engineered to work well with several types of metals, particularly those known for their low-carbon composition. The designation 'ER' in ER70S-6 reveals its status as an electrode or filler metal, whereas the '70' indicates its tensile strength which is 70,000 psi. The 'S' stands for a solid wire and the '6' is a mark of the chemical composition, mainly highlighting the presence of silicon and manganese.
Expert welders appreciate ER70S-6 for its high manganese and silicon content. This composition helps produce a more fluid weld pool, which can significantly reduce the incidence of porosity — a common issue in welding that can weaken joints and lead to premature failure of the weld. The fluidity allows for a better appearance and smoother finish. It is this chemical combination that confers the wire its ability to manage and clean mill scale on the metal surface effectively, which makes it an ideal choice for less-than-perfect base materials.
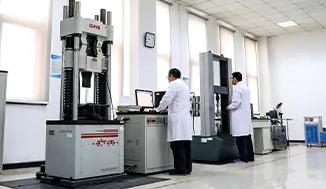
Professionals who have used ER70S-6 often point to its versatility and robust performance as key benefits. This wire is well-suited for both manual and automated welding processes, especially Gas Metal Arc Welding (GMAW) and TIG (Tungsten Inert Gas) welding. It provides excellent control and high feedability, which makes it a preferred choice for high-speed robotic applications too. This adaptability ensures that welders can maintain consistent quality, even when transitioning between processes.
welding wire er70s 6
From an authoritative perspective, manufacturers reiterate the benefits of deploying ER70S-6 in structural steelwork, automotive manufacturing, and even the construction of pipelines. Its excellent mechanical properties and high deposition rates make it suitable for these demanding applications. Additionally, thanks to its compatibility with both CO2 and a combination of Argon/CO2 shielding gases, ER70S-6 offers flexibility mainly because welders can choose gases based on the requirements specific to their projects.
Trustworthiness is a critical factor when selecting materials, and ER70S-6 does not disappoint. Many industry certificates recognize it, ensuring it meets stringent quality standards and receives approval in various sectors. Its reliability is captured by consistent user reviews and case studies that highlight its performance in both standardized and challenging conditions. Users report less post-weld cleaning, reduced spatter, and high weld strength — all confirming its trusted status among professionals.
In forming a cohesive judgment of ER70S-6's capabilities, it is imperative to consider real-world applications and expert testimonials that reaffirm its qualities. The success stories and endorsements from seasoned welders cannot be ignored. These accounts underscore the importance of selecting a wire that not only delivers on promises but also elevates the welding experience, ensuring that each joint is crafted to perfection, predictably and efficiently.
In summary, ER70S-6 stands out as a high-performing,
versatile welding wire. Its chemical composition delivers a superior welding experience embodying professionalism, expertise, and a high degree of trustworthiness. As a staple in many welding shops, its reliability is mirrored in the success rates and satisfaction of welders who depend on its performance for the structural integrity of their projects. Embracing the quality of ER70S-6 is a step toward ensuring unmatched durability and efficiency in welding endeavors.