Welding wire rod, a critical component in various metalworking industries, plays a pivotal role in ensuring strong, durable welds essential for structurally sound constructions and equipment. Understanding its versatility and applications can significantly enhance both efficiency and results in welding projects. This crucial tool is crafted with precision to meet the evolving demands of technology-driven industries.
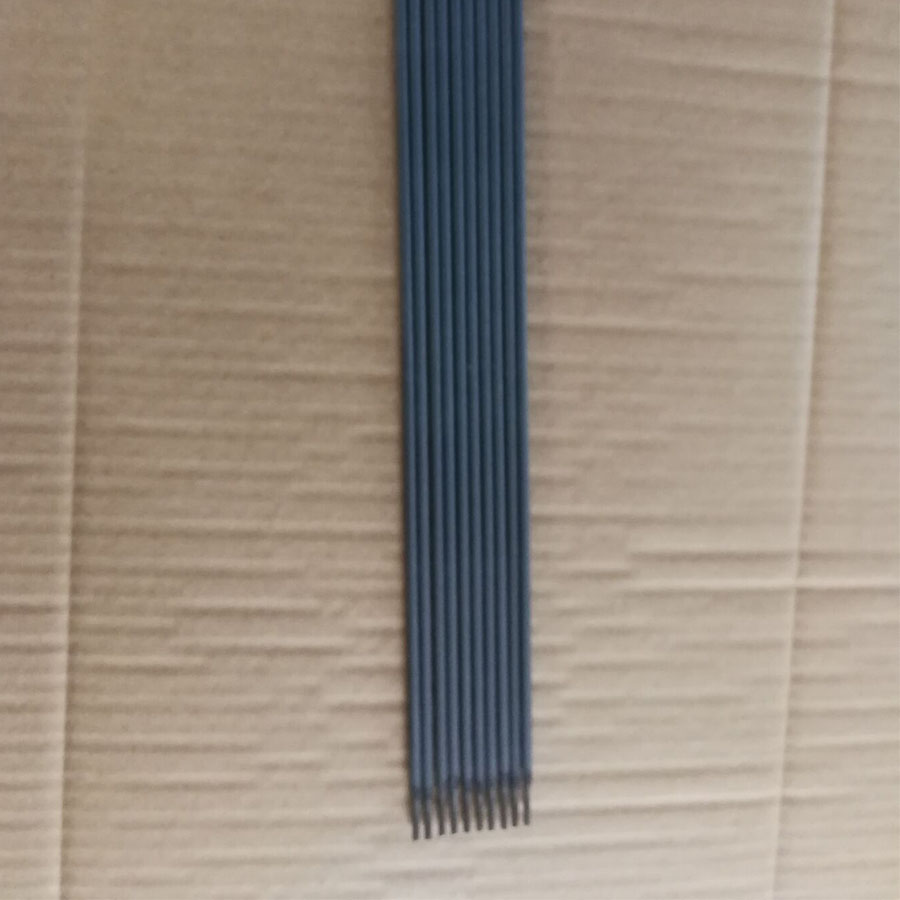
Welding wire rods come in a diverse range of compositions, each tailored to specific types of welding techniques and base metals. The choice of welding wire rod directly affects the strength, ductility, and corrosion resistance of the welded joint. For instance, when dealing with stainless steel projects, alloyed wire rods containing chromium and nickel provide excellent corrosion resistance and high tensile strength, making them indispensable in shipbuilding and manufacturing industries exposed to harsh environments.
Experience in the field consistently reinforces the importance of selecting the correct wire rod for optimal welding performance. Professionals often highlight the need for matching the wire rod's chemical composition with the base material to prevent weakening of the weld joint, which can lead to structural failures. An improperly selected rod can cause brittle welds, accelerating wear and shortening the life span of the welded product. Therefore, experienced welders always emphasize conducting a thorough analysis of the base materials and desired weld properties before selection.
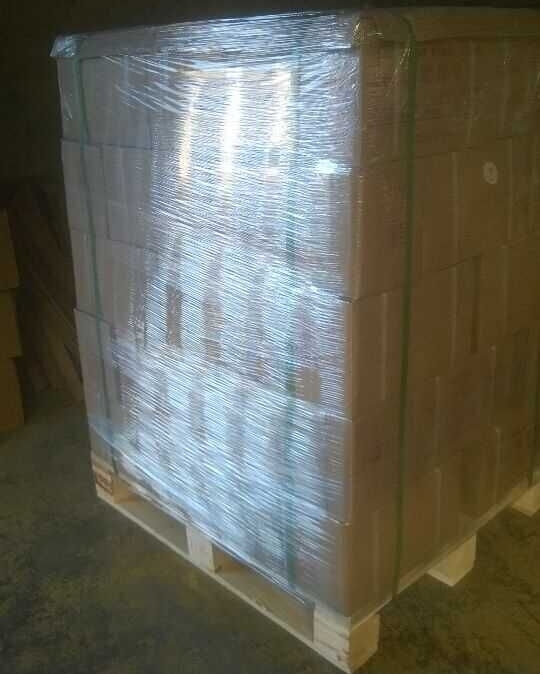
The expertise accumulated over years of practical application reveals another critical aspect the wire rod’s diameter significantly influences welding performance. A thicker rod might be more suitable for heavy-duty, high-heat applications, while thinner rods are efficient for precise, control-intensive tasks such as automotive or thin-sheet metal welding. This knowledge aids professionals in achieving optimal penetration and fusion characteristics, ensuring each project meets stringent industry standards.
welding wire rod
In terms of authoritativeness, companies producing welding wire rods often invest heavily in research and development to innovate high-performance materials capable of withstanding modern-day challenges. Certifications and compliance with international standards such as AWS, ISO, or EN ensure that these products not only meet safety requirements but also deliver unparalleled performance and reliability. Industry leaders share their findings through white papers and seminars, establishing guidelines for choosing and applying welding wire rods effectively.
A key factor contributing to trustworthiness is the reliability of suppliers. Reputable manufacturers maintain strict quality controls to ensure consistent product quality, which is crucial in maintaining the integrity of a broad range of applications, from aerospace engineering to infrastructure development. End users, therefore, must cultivate relationships with trusted suppliers who provide support, warranty, and expert guidance throughout the procurement process, thereby ensuring long-term success in their welding projects.
Additionally, ongoing training and adherence to safety protocols when working with welding wire rods cannot be overemphasized. Proper storage, handling, and equipment calibration are vital to preventing contamination and achieving the desired weld quality. Manufacturers often provide detailed user manuals and conduct workshops to update clients on the latest in welding technology, safety measures, and best practices.
In conclusion, welding wire rods are indispensable in the field of metalworking, influencing the strength and durability of the final product. Leveraging comprehensive experience and expertise in selecting the right type and size, along with the authoritative production standards provided by leading manufacturers, ensures successful welding outcomes. Building trust with credible suppliers further supports a seamless and efficient welding process, safeguarding the quality and longevity of each project. Understanding these facets is essential for anyone involved in welding, from beginners to seasoned professionals, ensuring that every weld meets the high expectations of today’s demanding industries.