Cast iron welding electrodes are indispensable tools in the field of metal repair and fabrication. These electrodes have been meticulously engineered to provide a reliable solution for welding cast iron, a material known for its complex properties and susceptibility to cracking when improperly handled. Drawing from years of expertise and industry authority, this article dives into the nuances of using cast iron welding electrodes, sharing insights that ensure successful and enduring welds.
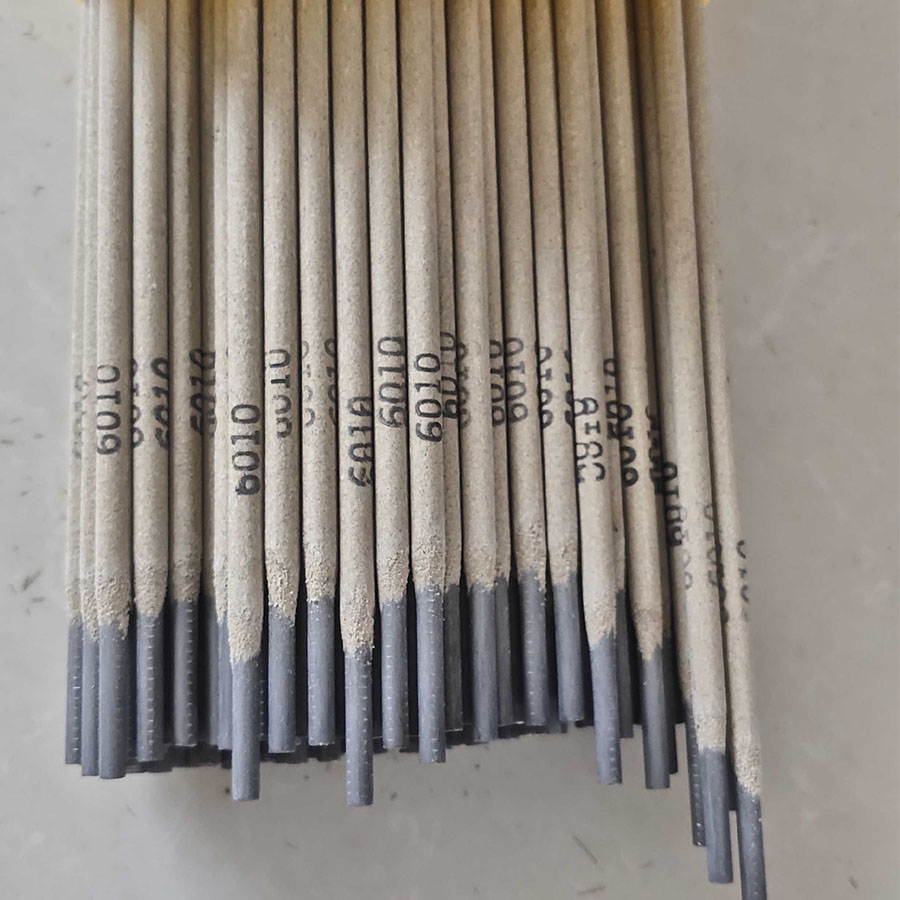
Cast iron possesses a unique combination of carbon, silicon, and iron, which gives it its advantageous properties, such as excellent machinability, wear resistance, and ability to dampen vibrations. However, these same properties render it challenging to weld. When heat is applied, the material expands at varying rates, often leading to stress concentrations and cracks. The right choice of welding electrode plays a pivotal role in mitigating these issues.
Expert welders often emphasize the need for pre-heating the cast iron workpiece to a temperature between 500°F and 1200°F. This practice reduces thermal shock and minimizes the risk of cracking. Selecting an appropriate cast iron welding electrode is the first step in this meticulous process. Nickel-based electrodes, for instance, are highly revered for their ability to produce strong, ductile welds that accommodate the differing thermal expansion characteristics of cast iron. Nickel 99 and Nickel 55 electrodes are among the most preferred due to their high nickel content, which enhances their compatibility with cast iron.
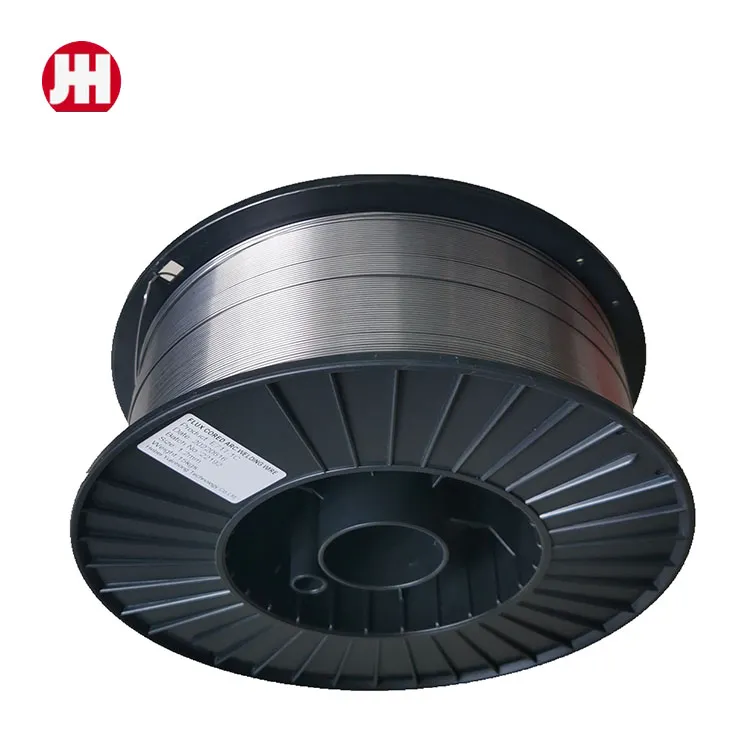
Beyond material compatibility, electrode selection hinges on the specific type of cast iron. Gray iron, with its flaky graphite microstructure, is more forgiving and often successfully welded with nickel or even steel electrodes. Conversely, nodular or ductile iron, characterized by spherical graphite inclusions, demands a more careful approach, often necessitating nickel electrodes to preserve its mechanical properties.
The welding technique greatly influences the outcome. Stringer beads are often recommended over weaving, as they introduce less heat into the workpiece, reducing the risk of distortion and residual stresses. Further, peening the weld beads immediately after deposition is a proven technique to counteract shrinkage stresses, enhancing the integrity of the weld. This involves gently striking the weld with a small hammer, compressing the weld metal as it cools, thus preventing the formation of tension-induced cracks.
cast iron welding electrode
Cooling practices are equally critical. Slow, controlled cooling in sand, lime, or covered by a heat-insulating blanket allows the cast iron to contract uniformly, again minimizing thermal stress. This gradual approach can mean the difference between a weld that stands the test of time and one that fails prematurely.
Authoritative voices in metallurgy stress the importance of thorough inspection post-welding. Non-destructive testing methods such as ultrasonic testing or magnetic particle testing can reveal subsurface defects that might escape the naked eye, ensuring the integrity of the weld before the part is put to service.
In terms of credibility, manufacturers of cast iron welding electrodes often provide detailed specifications and guidelines, offering insights into their optimal use. Consulting these resources and adhering to industry best practices enhances the welder’s ability to achieve a satisfactory outcome. Certifications from organizations such as the American Welding Society (AWS) can provide additional assurance of an electrode's suitability for cast iron.
Ultimately, the successful application of cast iron welding electrodes hinges on a combination of theoretical knowledge and practical expertise. Each step, from electrode selection to post-weld inspection, requires attention to detail and an understanding of the underlying metallurgical principles. By marrying these elements, welders can achieve repairs and fabrications that exhibit both strength and durability, preserving the functionality of cast iron components across a myriad of applications.