Selecting the right material for welding projects is crucial, and understanding why 304 stainless steel MIG wire stands out is essential for achieving superior results. As a widely used alloy, 304 stainless steel offers a blend of characteristics that make it ideal for a range of applications. With a unique set of properties, this specific MIG wire ensures both efficiency and durability.
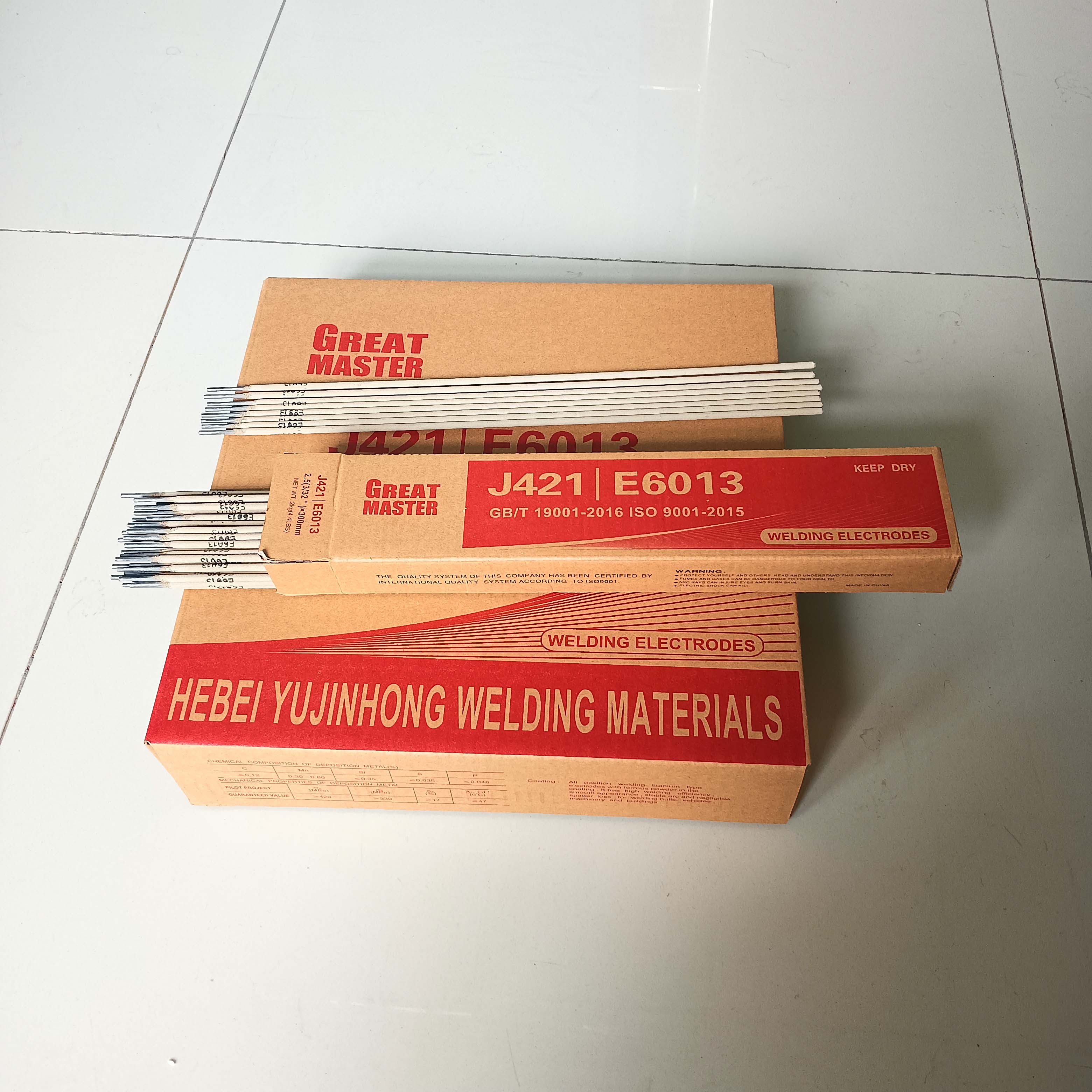
304 stainless steel is known for its excellent corrosion resistance and making the corresponding MIG wire an exceptional choice for environments prone to moisture and varied temperatures. This feature is driven by the presence of chromium, a pivotal element that forms a protective layer over the steel, preventing rust and decay even in harsh conditions. For industries ranging from food processing to chemical manufacturing, using 304 stainless steel MIG wire means a longer lifespan for the welds, reducing maintenance costs and downtime.
Moreover,
the weldability of 304 stainless steel is another reason experts recommend sticking to this material. The wire's compatibility with a wide range of welding parameters ensures adaptability and ease of use, catering to both professionals and enthusiasts. Whether you're working on heavy-duty construction projects or delicate fabrication tasks, the smooth and consistent feed of 304 stainless steel MIG wire guarantees minimal spatter and clean weld beads, translating to less post-weld cleanup and a more aesthetically pleasing finish.
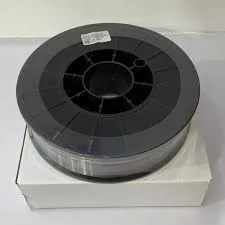
The tensile strength of 304 stainless steel is nothing short of impressive, providing a robust joint that withstands significant stress and impact. This strength is vital in applications where the welded joints are subjected to dynamic loads. Hence, industries such as automotive and aerospace, which demand stringent adherence to safety and performance standards, often prefer 304 stainless steel MIG wire to ensure that their products meet these criteria.
304 stainless steel mig wire
From a technical perspective, the reduced thermal expansion of 304 stainless steel is advantageous during the welding process. It minimizes warping and distortion, enhancing the quality of the work. This attribute is particularly beneficial in precision-driven industries, such as medical device manufacturing, where even minor imperfections can lead to critical failures.
The authority of using 304 stainless steel MIG wire is backed by years of practical application and research. Both welding specialists and metallurgists have extensively documented its benefits, reinforcing the wire’s status in the metal fabrication community. Standards organizations such as the American Welding Society (AWS) and the International Organization for Standardization (ISO) provide comprehensive guidelines on how to best utilize this material, adding an extra layer of trustworthiness for those considering its use.
In summary, 304 stainless steel MIG wire is an indispensable resource in the welding world, offering unmatched corrosion resistance, ease of use, and strength. For anyone looking to ensure quality and reliability in their welding projects, this specific alloy remains a trusted companion. Not only does it hold up under pressure, but it also delivers efficiency and peace of mind, allowing users to focus on what matters most crafting exceptional results.