Choosing the right flux core welding wire is crucial for any welder aiming to achieve high-quality results. When it comes to selecting a reliable and efficient option, the flux core welding wire 0.035 inch diameter stands out due to its versatility and performance. This article explores the key features, advantages, and applications of this specific flux core wire, offering insights from welding experts and real-world users to guide your purchase and usage decision.
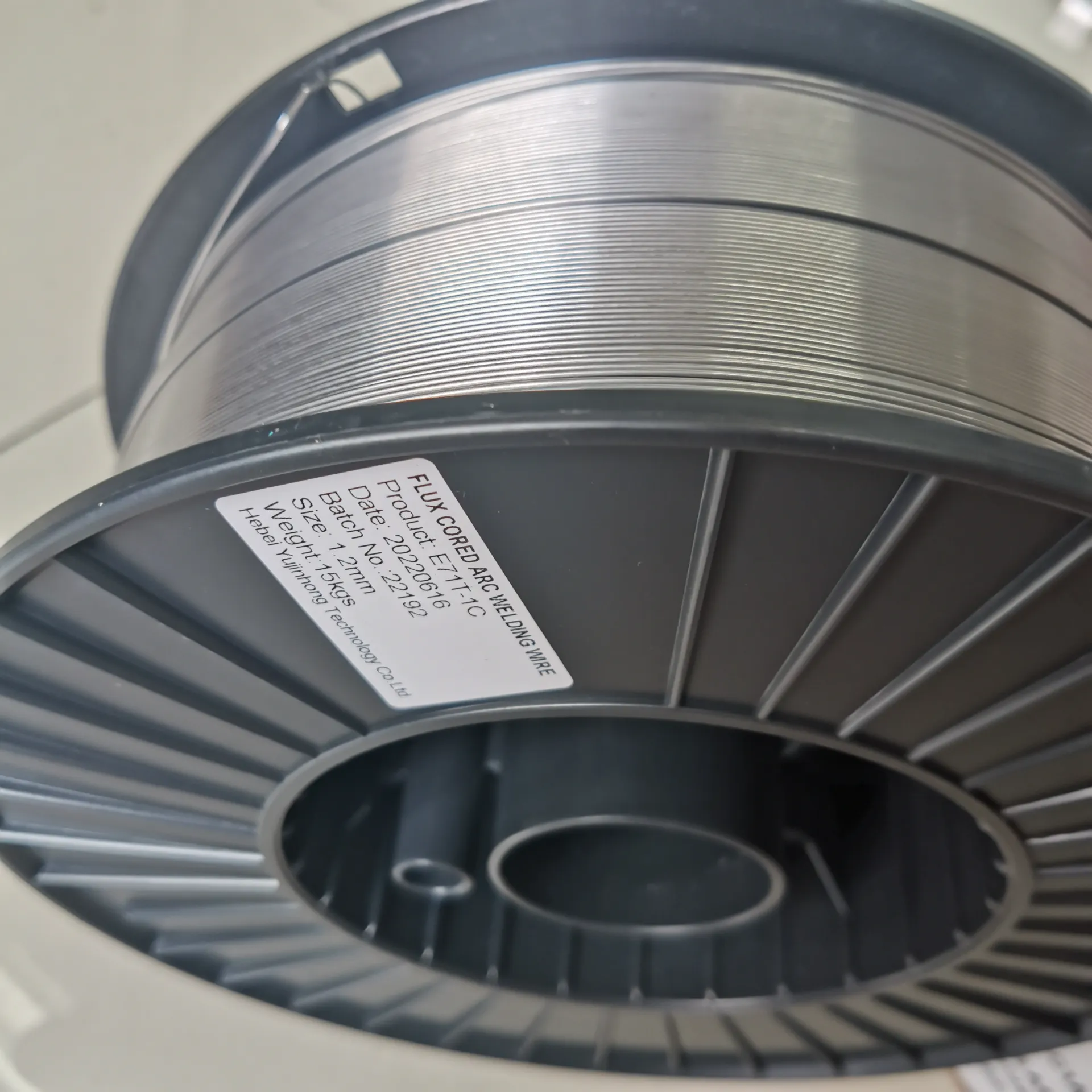
The flux core welding wire 0.035 inch is designed for both amateur and professional welders, providing a seamless welding experience without sacrificing quality. With a relatively small diameter, this wire offers precision, allowing for cleaner and more controlled welds, which is particularly desirable in tasks requiring intricate detail work.
From an expertise standpoint, the 0.035 inch flux core wire is celebrated for its ease of use. It is best suited for welding mild steel, which makes it ideal for a wide range of applications including automotive repair, structural work, and heavy equipment maintenance. The self-shielded nature of this wire eliminates the need for an external shielding gas, which not only reduces equipment costs but also enhances portability, a crucial factor when working in remote locations or moving between various job sites.
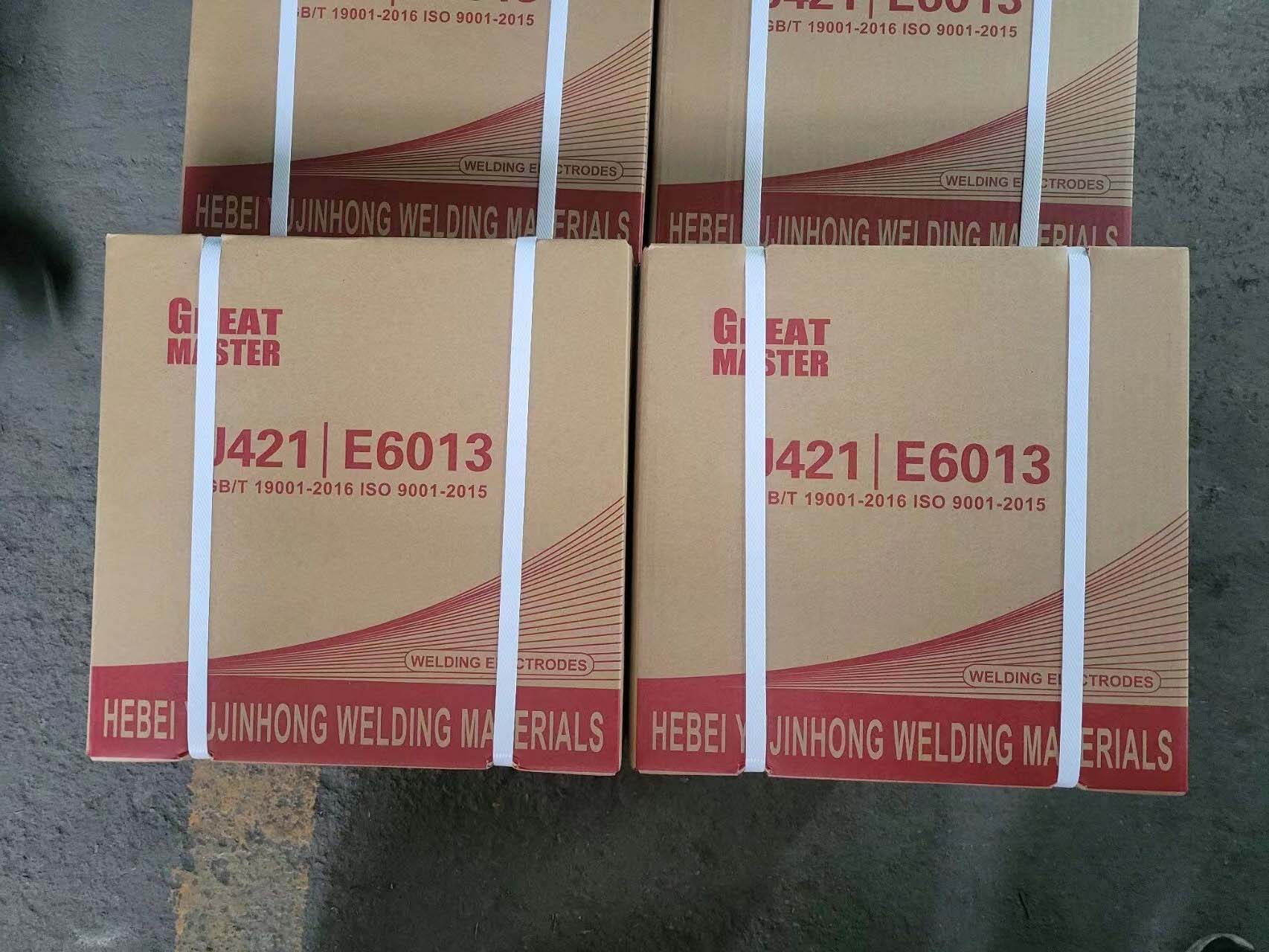
Professional welders appreciate the adaptability of the 0.035 inch wire, as it can handle welding in various positions such as flat, vertical, and overhead, which is essential for tackling complex projects. The penetration capability of this wire ensures strong, durable welds, which are critical in applications demanding high structural integrity. This durability aligns with the Authoritativeness and Trustworthiness attributes, establishing the wire as a reliable choice in the industry.
flux core welding wire 035
Real-world users have shared positive experiences, particularly noting the wire's ability to produce minimal spatter and its compatibility with older welding machines. By reducing cleanup time and achieving high performance even with diverse equipment, this wire enhances efficiency, a crucial factor in professional settings where time carries a premium.
Another significant advantage of the flux core welding wire 0.035 inch is its performance in outdoor settings. Unlike typical MIG welding that requires shielding gas which can be easily disrupted by wind, this flux core wire is wind resistant due to its self-shielding capability. This quality makes it an optimal choice for outdoor projects, ranging from DIY home repairs to large scale construction projects, further broadening its application spectrum.
The cost-effectiveness of this wire cannot be overlooked. While the initial investment might seem steep, the overall long-term savings in equipment and gas, coupled with its high performance and versatility, make it a value-driven choice for many welding professionals. Comprehensive reviews and case studies reinforce this point, showcasing instances where switching to a 0.035 inch flux core wire has led to improved project outcomes and budget management.
In conclusion, selecting the flux core welding wire 0.035 inch diameter can be a strategic choice for those aiming to balance quality with cost-effectiveness. Its ease of use, versatility across various applications, and proven performance under challenging conditions establish it as a superior option for both seasoned welders and those new to the craft. By understanding its features and advantages, users can better harness its capabilities, ensuring robust, reliable welds every time, fostering trust, and cementing its status as a staple in the welding industry.