Understanding and Selecting ER70S-6 MIG Welding Wire A Comprehensive Guide
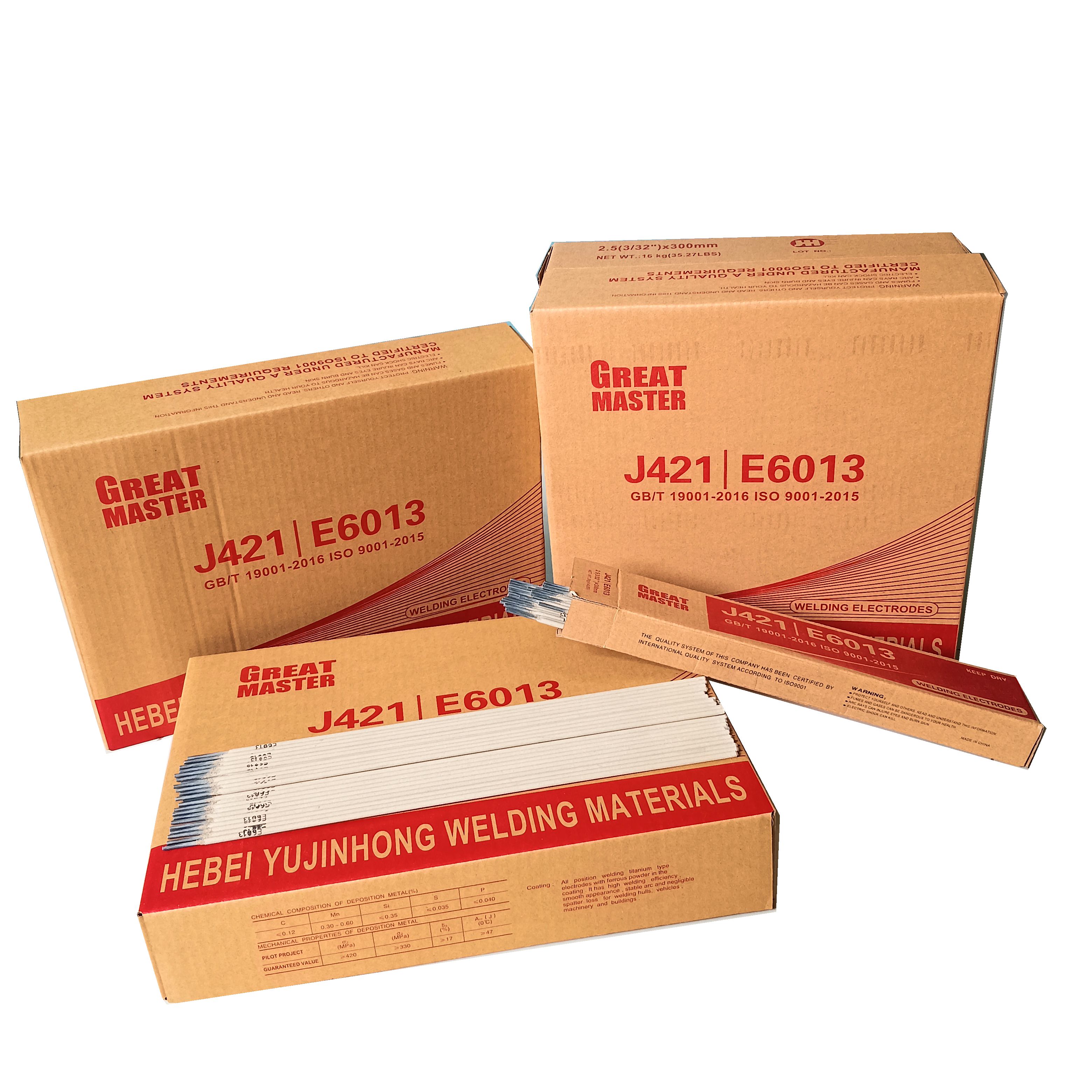
Choosing the right MIG welding wire is essential for achieving optimal welds, particularly in demanding industrial applications. ER70S-6 is one of the most commonly used types of MIG welding wire due to its versatility and ability to deliver high-quality results. This guide explores the distinctive features, applications, and advantages of ER70S-6 wire, providing key insights into its role in the welding process.
ER70S-6 MIG welding wire is characterized by its chemical composition, primarily consisting of manganese and silicon. These components enhance the wire's performance, making it suitable for welding on dirty or rusty steel. The integrated deoxidizers work efficiently to clean the metal surface during the welding process, reducing splatter and ensuring a cleaner bead appearance. This reduction in splash directly correlates with post-weld cleanup time, significantly streamlining industrial operations.
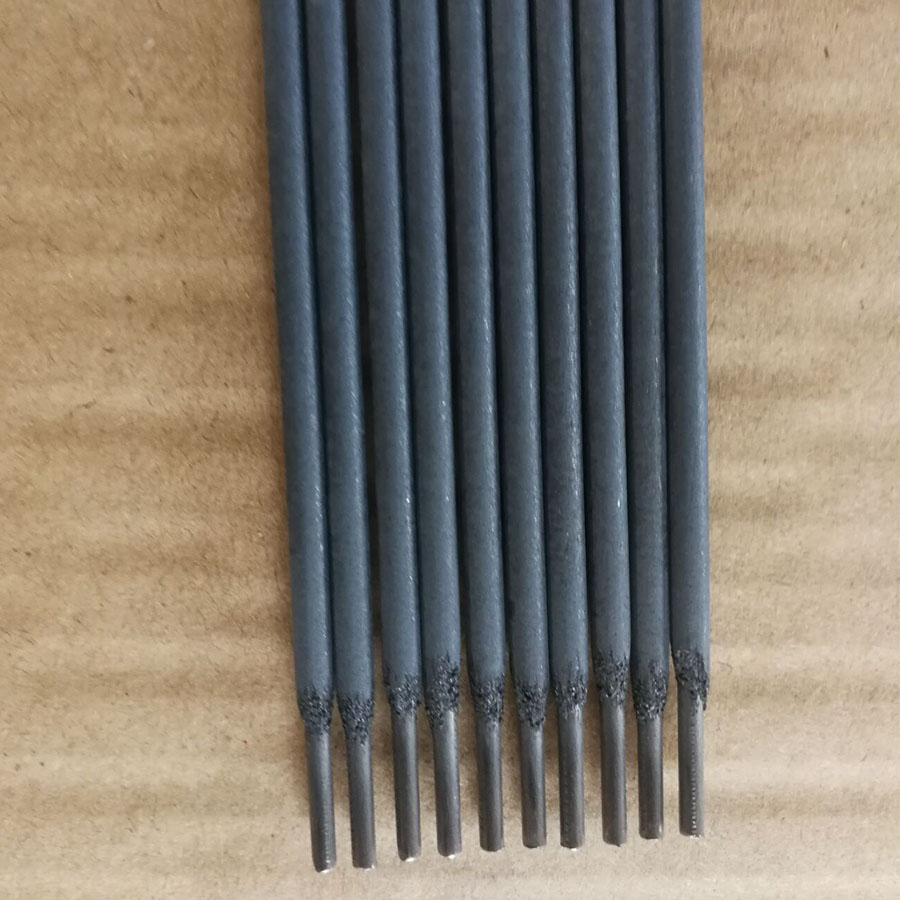
One of the standout features of ER70S-6 is its ability to deliver excellent weld quality even in less-than-ideal conditions. This wire is acclaimed for its compatibility with a variety of shielding gases, including pure CO2 and Argon-CO2 mixtures. The flexibility in gas selection not only contributes to improved arc stability but also broadens the scope of its application across various welding environments.
In fabricating industries and construction sites, where steel is often coated in rust or mill scale, ER70S-6 is highly favored. Its increased levels of silicon and manganese allow welders to work on these challenging surfaces without compromising the integrity of the weld. Additionally, ER70S-6 improves overall mechanical properties, such as tensile strength and impact resistance, critical for structures exposed to stress and dynamic loads.
The operational efficiency of ER70S-6 is evident through its user-friendly attributes. Welders experience a smooth feeding experience as the wire is engineered to provide consistent and reliable performance across different welding machines. This consistency plays a key role in minimizing downtime associated with wire tangling or inconsistent arc lengths.
As an experienced welder or project manager focusing on quality and economic feasibility, using ER70S-6 can contribute positively to both aspects. Cost-wise, this wire proves to be economical due to its ability to minimize defects and rework. Moreover, the properties of ER70S-6 reduce the likelihood of porosity and cracking in the weld, thereby increasing the overall lifespan of the welded structure.
er70s-6 mig welding wire
Experienced welders vouch for ER70S-6 not just for its performance across diverse applications but also for its adaptability with varying welding positions. This adaptability ensures that ER70S-6 meets the demand for horizontal, vertical, flat, and overhead positions, making it a versatile choice in assembly lines and onsite fabrications.
Despite its many advantages, the misuse of ER70S-6 can lead to undesirable welding outcomes. Over time, improper storage conditions can lead to moisture absorption, causing issues such as hydrogen-induced cracking. To mitigate this risk, it's essential to store the wire in a dry and controlled environment and practice proper handling techniques.
For industries concerned with quality assurance and maintaining high standards, ER70S-6 meets the specifications of the American Welding Society (AWS), ensuring that welds perform consistently under rigorous conditions. This compliance indicates the wire's capability of maintaining desirable mechanical properties across various fabrication processes, contributing to its reputation as a reliable welding partner.
Implementing a strategic evaluation for selecting ER70S-6 involves considering factors such as thickness and type of base metal, joint design, and the welding position. A meticulous assessment guarantees that the wire's properties align harmoniously with project requirements, enabling the achievement of robust and durable welds.
Incorporating ER70S-6 MIG welding wire into your operations not only enhances the quality of welds but also optimizes efficiency. From automotive sectors to heavy machinery manufacturing, the benefits of adopting ER70S-6 are extensive, contributing to superior joint performance, reduced processing time, and improved end-product durability.
Conclusively,
ER70S-6 MIG welding wire exemplifies a fusion of reliability, adaptability, and economy. Its acclaimed performance, upheld by years of expert usage and industrial endorsement, positions it as an indispensable tool for professionals keen on achieving excellence in welding applications. Choosing ER70S-6 wire is a strategic decision fostering operational success and quality output in metalworking industries.