The 3/16 welding rod, a key component in the arsenal of any welding professional, showcases precise craftsmanship and enduring quality that defines it as a pinnacle of reliability in welding projects. As the backbone of numerous welding applications, the 3/16 welding rod stands out with its versatility and strength, crucial attributes that cater to a wide range of industrial and personal welding needs.
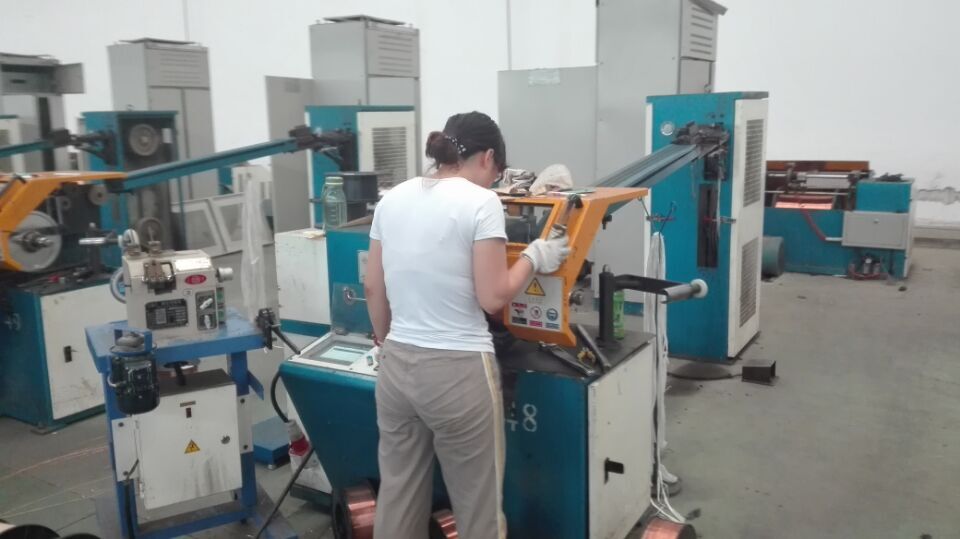
Expert welders often prefer the 3/16 welding rod for its consistent performance in joining metals with varying levels of thickness and composition. This welding rod is commonly crafted from materials such as mild steel and low-alloy components, enhancing its adaptability to various metal bonding scenarios. The 3/16 diameter represents an ideal balance between thickness and manageability, offering precision in welds that require a robust yet flexible approach.
In practical applications, the 3/16 welding rod ensures optimal heat distribution and penetration, key factors that determine the integrity and durability of the weld. Skilled professionals recognize the significance of these attributes, as they directly impact the structural soundness of their projects. The rod's dimensions allow for ample deposition rates, creating strong, reliable joints that withstand mechanical stresses and thermal expansion.
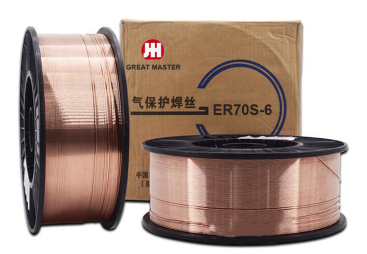
From construction projects to automotive repairs, the 3/16 welding rod finds its place in diverse settings, including the fabrication of frames, beams, and pipelines. Its ability to accommodate both AC and DC currents further enhances its utility, making it a favored choice among welders seeking to execute complex tasks efficiently. This dual compatibility enables professionals to switch between welding conditions seamlessly, optimizing their workflow and ensuring precision in every application.
3 16 welding rod
A testament to its expertise, the 3/16 welding rod aligns with various welding processes such as Shielded Metal Arc Welding (SMAW), a widely utilized method known for its flexibility and ease of use. Within the SMAW process, the rod's coating plays a significant role in stabilizing the arc and shielding the metal from contaminants, contributing to cleaner and more consistent welds. This protective coating, often composed of a tailored blend of minerals and binding agents, ensures minimal slag formation, reducing post-weld cleaning and enhancing productivity.
Analyzing the 3/16 welding rod through an authoritative lens reveals its indispensability in professional circles. Manufacturers adhere to stringent quality control measures, ensuring each rod meets established standards and specifications. This commitment to excellence not only guarantees the reliability of the rods but also strengthens the trust welding professionals place in them. As a result, the 3/16 welding rod has earned a reputation for being a go-to resource for achieving superior weld quality across diverse project scopes.
Understanding the technical specifics and real-world application scenarios of the 3/16 welding rod empowers welders with knowledge that transcends traditional practices. With practical experience, welders gain a deeper appreciation for the nuances of how the rod behaves under different conditions, leading to more informed decisions that enhance the overall success of their projects. Trust in the 3/16 welding rod is built upon this foundation of expertise and experience, making it a critical asset for professionals dedicated to achieving excellence in their craft.
Ultimately, the 3/16 welding rod emerges as not only a tool but a testament to the skill and dedication of the professionals who wield it. Its storied reputation within the industry underscores the integral role it plays in advancing the welding discipline, symbolizing the fusion of art and science that defines modern welding. As technology evolves, the core principles that guide the use of the 3/16 welding rod remain steadfast, continuing to inspire confidence in those who rely on its exceptional performance and reliability.