In the realm of metal fabrication, the selection of electrodes for welding is a crucial decision that directly impacts the quality and durability of the welds. Successfully navigating through the complexities of electrodes welding requires not just a working knowledge of the materials and techniques but also hands-on experience and expert insights.
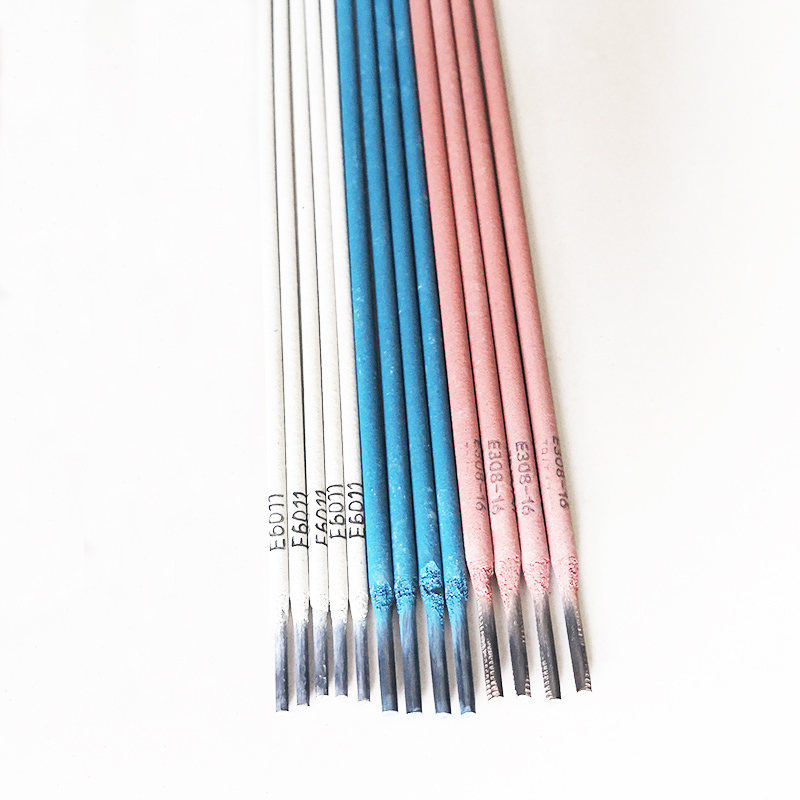
For seasoned welders, the choice of welding electrode is akin to a craftsman's choice of tool—each type is suited for specific tasks and materials, contributing to both the efficacy and efficiency of the process. In particular, the E6010 and E7018 electrodes are frequently the stars of the show in many welding projects, each possessing unique characteristics tailored to distinct welding environments and applications.
E6010 electrodes are celebrated for their ability to penetrate deeply and perform admirably on rusty or dirty metals, thanks to their cellulose-based flux coating. They produce a forceful, deeply penetrating arc that cuts through impediments, making them invaluable in maintenance and repair roles. Moreover,
E6010 is a direct current electrode, ideal for welding in challenging positions.
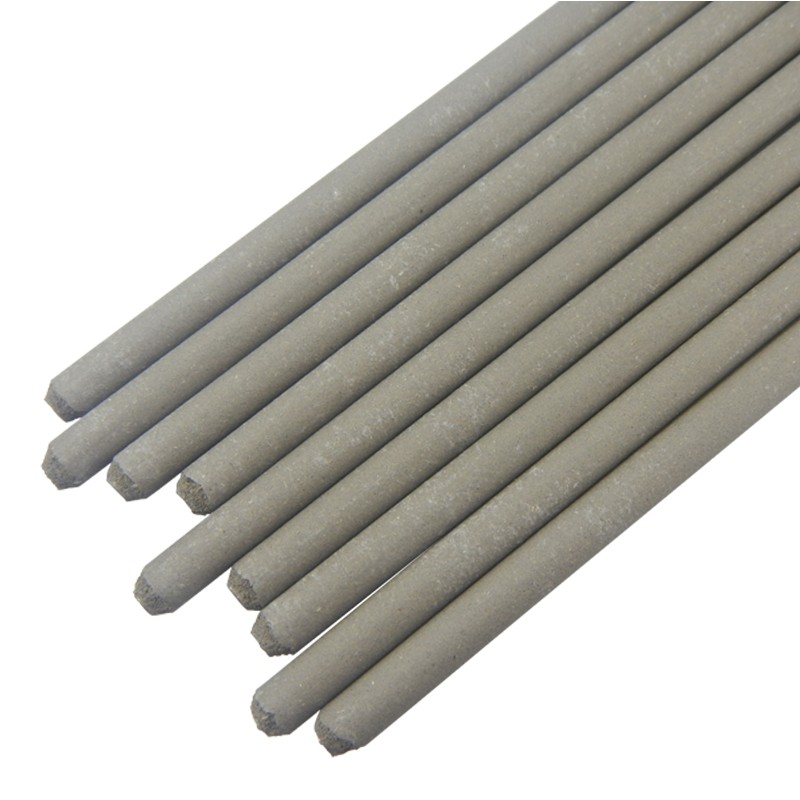
On the other side of the spectrum, the E7018 electrode stands out because of its low-hydrogen content, which significantly reduces the risk of hydrogen-induced cracking, a common enemy in structural welds. Industries that demand high strength and low defect incidence, such as construction and shipbuilding, often rely on E7018 for its excellent mechanical properties and smooth, stable arc. Additionally, the E7018 requires a careful approach to storage, necessitating an oven to maintain optimal moisture content, reflecting its specialized nature.
electrodes welding
Beyond the technical specifications, a professional’s expertise in wielding these electrodes translates into a palpable difference in the quality of the welds produced. The rhythm of welding, the angle of attack, and the speed of travel all contribute collectively, honed by years of practice and guided by both theoretical and practical training. Mastery over these aspects not only ensures superior weld integrity but also optimizes production timelines, reducing overhead costs in the long run.
However, the authority one commands in electrodes welding is a product of sustained learning and adaptation to new technologies and materials. The welding industry is dynamic, with innovations in electrode coatings and compositions being introduced to achieve even greater efficiency and environmental compliance. Engaging with authoritative sources like welding institutes and professional seminars helps in staying abreast of these advancements, enhancing one's authority and proficiency.
Trustworthiness in electrode welding, meanwhile, is built on a foundation of consistent, high-quality outcomes. This trust is forged between a welder and their clients or employers through certifications, demonstrated competency, and adherence to safety standards. Furthermore, participation in quality assurance programs and regular performance evaluations further cements this trust, affirming one's commitment to excellence.
In conclusion, while electrodes welding may seem deceptively straightforward at a glance, it is an art as much as a science, demanding a blend of experience, expertise, authority, and trustworthiness. Each weld is a testament to the skill and knowledge of the welder, standing strong against the scrutiny of industry standards and the test of time. Embracing this philosophy not only paves the way for individual success but also drives innovations and advancements within the welding industry as a whole.