For welding professionals and hobbyists alike, the right choice of electrodes can differentiate between a perfect weld and a costly mistake. In taking a deeper dive into the nuanced world of electrode welding, you begin to understand not just the process but the craftsmanship required to perfect it. Electrode welding, a fundamental aspect of metalworking, hinges on four pivotal factors the electrode type, the material being welded, the available welding equipment, and the desired outcome of the welding project.
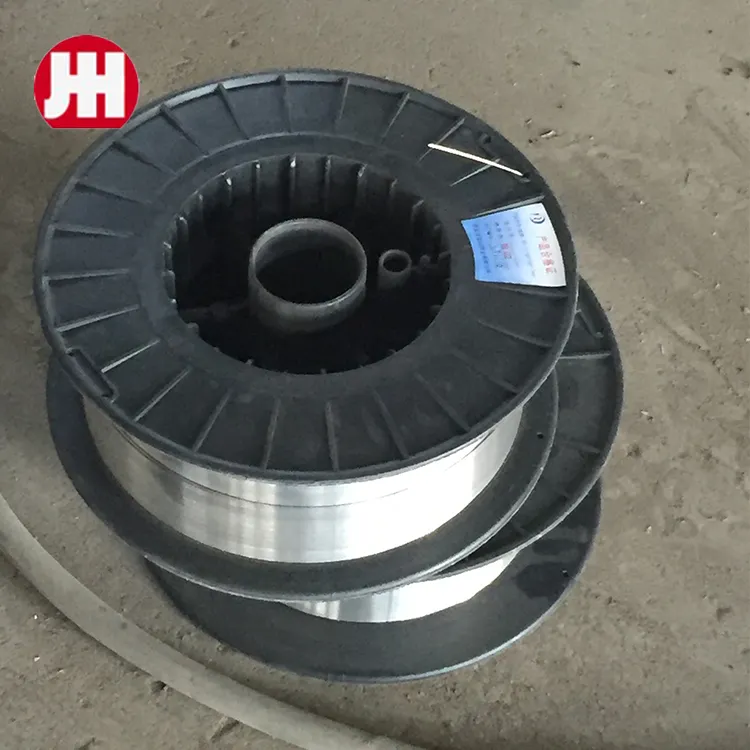
Electrodes are at the heart of arc welding, where their role is to conduct the current to form an electric arc, creating a heat source to melt and fuse metals. In doing so, the selection of the right electrode is paramount. When considering the extensive array of electrodes, it's essential to match the electrode's properties with the base material and the intended welding process. For instance, mild steel electrodes are recognized for their versatility and are widely used due to their ability to form strong welds with ease. However, for more specialized needs, such as welding stainless steel or aluminum, specific alloys are required to handle the unique thermal and structural demands.
The physical and chemical properties of electrodes speak to their professional expertise. Each electrode is designed for a particular set of conditions and material types. The coating, a critical component, provides additional stability and protection during the welding process. For welders looking for reliability and consistency, the E6010 electrode stands out with its ability to generate deep penetrating arcs, ideal for pipe welding and those positions where access is limited.
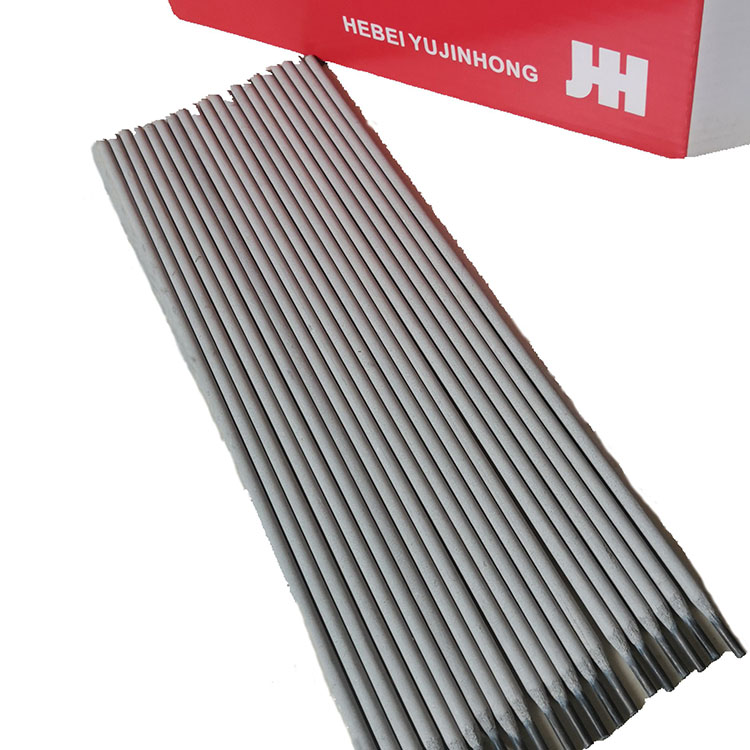
The choice of electrode influences not just the technical outcome but also the operational efficiency of welding projects. In terms of expert recommendations, matching the electrode to your welding equipment is critical. Some welding machines operate better with certain types of electrodes. For instance, AC machines often pair best with electrodes like the E7018, known for its low hydrogen coating that minimizes moisture absorption and cracking in the weld.
electrodes welding
Trustworthiness is established over years of hands-on experience. Seasoned welders often share insights that textbooks cannot provide. For instance, the subtle differences in handling and performance of electrodes under varying environmental conditions – like humidity and temperature – can dramatically change the weld's outcome. Thus, genuine, hands-on practice adds to a welder's credibility and the trust in their work.
Understanding the nuances of electrode welding reveals the breadth of skill and knowledge required behind the scenes. Mastery involves familiarizing oneself with technical manuals and electrode specification sheets, which provide detailed information about operating currents, positions, and suitable base materials. Beyond documentation lies the practical realm, where learning is enriched by trial and error, iterating through different electrodes to find the most suitable for your specific welding context.
Recognized welding certification programs further bolster authoritative standing in the practice. They teach comprehensive welding techniques, electrode chemistry, and safety precautions – factors that contribute to a welder's professional development. Moreover, daily maintenance of both electrodes and welding equipment is crucial, as it prevents unexpected downturns in performance and consistency. For the welding industry, adopting digital solutions for record-keeping ensures traceability and promotes quality standards.
Ultimately,
the craft of electrode welding marries art with science. Through a commitment to continued learning, openness to technology advances, and a respect for the materials worked with, welders not only bring processes to life but build a reputation grounded in expertise, reliability, and innovation.