Flux core stainless wire has become an indispensable asset for welders dealing with diverse applications across industries. This specialized wire, utilized for flux-cored arc welding (FCAW), merges the robustness of stainless steel with the adaptability of flux core technology, making it a preferred choice for projects demanding durability and precision.
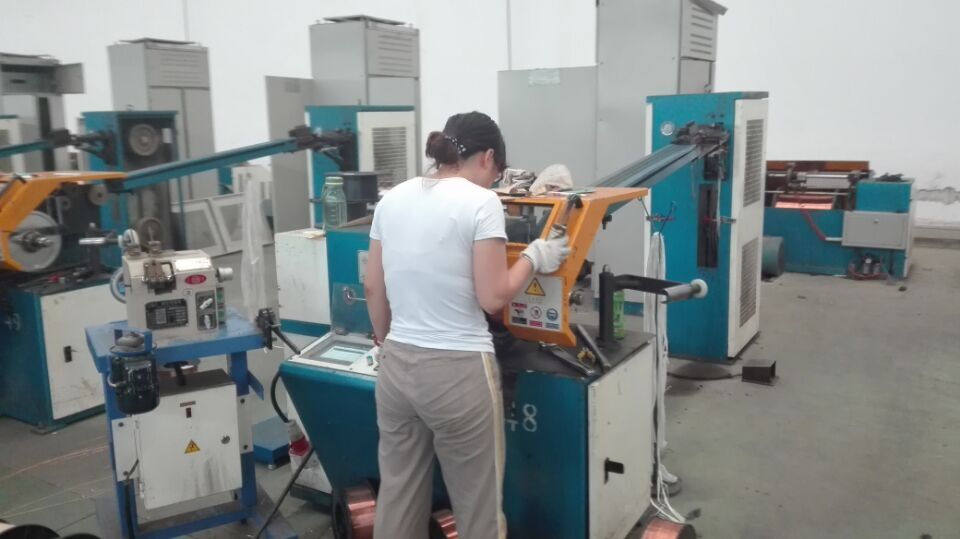
Flux core stainless wire boasts a unique construction that involves a hollow tube filled with flux. This design enables the wire to produce its shielding gas, safeguarding the weld pool from atmospheric contamination. The reduced need for an external gas supply enhances its usability in outdoor environments and drafty conditions where traditional gas-shielded welding might falter.
One of the pivotal advantages of using flux core stainless wire is its superior penetration capability. This aspect makes it exceptionally efficient for welding thicker materials, a common requirement in industries such as shipbuilding, petroleum processing, and construction. It allows for deep penetration and strong, reliable welds that withstand rigorous service conditions.
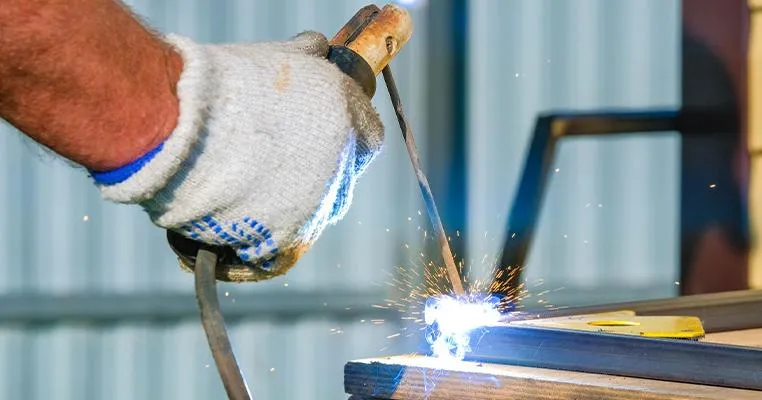
Moreover, the performance efficiency of flux core stainless wires is notable in its deposition rate. High deposition rates mean faster weld completion times, reducing labor costs and increasing project throughput. This efficiency is particularly beneficial during large-scale manufacturing processes or when time constraints are critical.
Flux core stainless wires are designed to handle high heat inputs typical in FCAW processes, producing minimal spatter and clean welds. The resulting bead appearance is sleek and meets industry standards, minimizing post-weld cleanup and further streamlining production lines.
flux core stainless wire
In terms of versatility, these wires are available in various grades, including 308, 309, and 316. Each grade offers unique properties suitable for specific applications. For instance, grade 308 is widely used for general-purpose stainless steel welding, whereas grade 316 provides enhanced corrosion resistance, vital for marine or highly acidic environments.
It's important to note the expertise required to maximize the benefits of flux core stainless wire. While the FCAW process can be more forgiving than other welding methods, understanding wire feed speed, voltage settings, and travel speed is crucial. Proper technique ensures optimal weld quality and performance, so a competent operator is invaluable.
Safety and reliability are cornerstones of trustworthiness in any welding operation. Flux core stainless wire aligns with industry safety standards, ensuring welders have confidence in the materials they use. Manufacturer credentials and compliance certificates can provide additional assurances regarding product quality and safety.
The environmental considerations associated with flux core stainless wire usage add another layer of appeal for contemporary businesses. With increasing emphasis on sustainable practices, opting for welding methods that minimize waste and energy consumption is a step towards eco-friendly operations.
In summary, flux core stainless wire is a crucial component in the welding industry, offering a blend of durability, efficiency, and reliability. Its construction simplifies complex welding environments, and its performance matches the demanding needs of modern industries. Whether you're handling thick junctions in shipbuilding or crafting corrosion-resistant containers, this wire emerges as an expert's choice for unparalleled results. Engaging with suppliers that prioritize quality and customer support ensures your operations remain at the forefront of technological advancements, enhancing both productivity and profitability.