Mastering the Art of MIG, TIG, and Stick Welding for Optimal Results
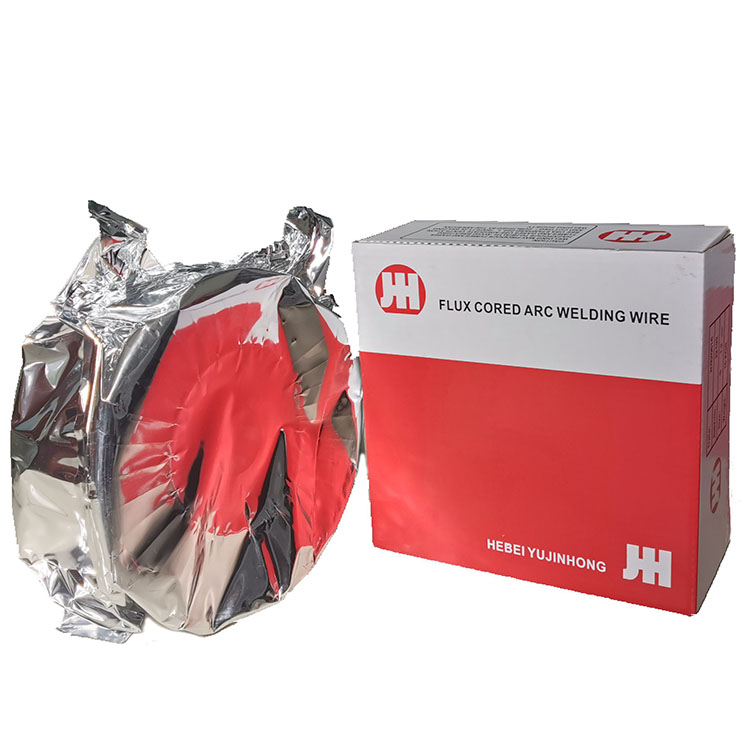
When it comes to the realm of welding, few skills are as indispensable as those associated with MIG, TIG, and Stick welding. Each method possesses unique characteristics that set them apart, serving various purposes and applications across industries. For anyone entrenched in or new to the welding sector, understanding the nuances of each type is pivotal for both product quality and career advancement.
MIG Welding The Workhorse of the Industry
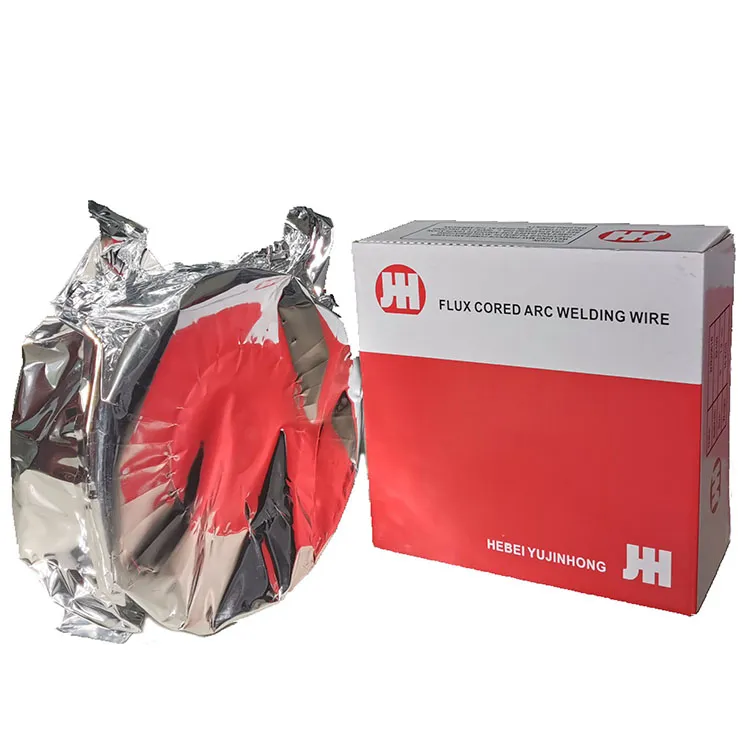
Metal Inert Gas (MIG) welding, also known as Gas Metal Arc Welding (GMAW), is revered for its ease of use and efficiency.
It employs a continuous wire feed as an electrode and shielding gas to protect the weld pool. Beginners and experts alike celebrate MIG welding for its straightforward nature and high productivity, especially on thicker metals like steel and aluminum.
MIG welding shines in environments where speed and efficiency are paramount. Automotive manufacturing, construction, and large-scale fabrication benefit greatly from the rapid application and minimal downtime associated with this method. Professionals often point out its minimal learning curve, making it the ideal starting point for novices. However, mastery in MIG comes from understanding the precise voltage and wire speed settings that can vary significantly depending on the material and thickness.
TIG Welding Precision and Finesse
Tungsten Inert Gas (TIG) welding, or Gas Tungsten Arc Welding (GTAW), stands out for its precision and control. Unlike MIG, TIG uses a non-consumable tungsten electrode and requires both hands for operation—one holding the torch and the other feeding the filler material. This dual-hand control allows for unmatched detail and finish, an essential factor when working with delicate materials such as stainless steel and exotic metals.
Industries such as aerospace, art, and high-end custom fabrication rely heavily on TIG welding for its clean, high-quality welds without the need for excessive finishing work. Those who've mastered TIG welding often highlight the importance of patience and practice, as the method requires a deep understanding of heat settings, angles, and travel speed for optimal performance. Moreover, a trustworthy TIG welder must ensure a steady hand and an apt eye for detail, affirming the technique's appropriateness for top-tier manufacturing requirements.
mig tig stick welding
Stick Welding Rugged and Versatile
Shielded Metal Arc Welding (SMAW), commonly referred to as Stick welding, is known for its versatility and rugged applicability in less than perfect environments. Using a consumable electrode coated in flux, this technique can be employed on rusty or dirty surfaces—a situation other welding methods may struggle to accommodate.
Particularly advantageous for outdoor and remote construction projects, Stick welding does not require a shielding gas, making it less susceptible to windy conditions. Advisory committees within the welding community suggest its pertinence in construction, maintenance, and repair fields, citing its affordability and equipment durability as key assets. Experienced welders often earmark Stick welding for its broad adaptability, allowing for effective work on a wide range of materials, including cast iron and alloys.
Conclusion Choosing the Right Method
Selecting the appropriate welding technique depends heavily on the material, environment, and desired outcome. For beginners, MIG offers a practical introduction to welding basics, while TIG provides the challenge for those seeking to perfect their finesse and technique. Stick welding, on the other hand, remains an exemplary choice for harsher conditions where adaptability reigns supreme.
For professionals across the spectrum, continuous learning and adapting to new technologies remain crucial. Investing in expert training and certifications solidifies trust and credibility, anchoring one’s authority in a competitive field. Tools like updated equipment and a well-maintained workspace can significantly uplift the quality of work produced.
In conclusion, MIG, TIG, and Stick welding each play an integral role in the fabric of manufactured goods, infrastructure, and art. Understanding and mastering these techniques not only enhances product outcomes but also fortifies an individual’s reputation as a skilled craftsman in the welding industry.