Stainless steel stick welding, often referred to as SMAW (Shielded Metal Arc Welding), is a versatile process prized for its adaptability, even in challenging environments. As industries increasingly demand robust materials for construction and repair, stainless steel's corrosion-resistant properties make it an indispensable component. Selecting the right welding rod and mastering the technique are crucial aspects when working with stainless steel.
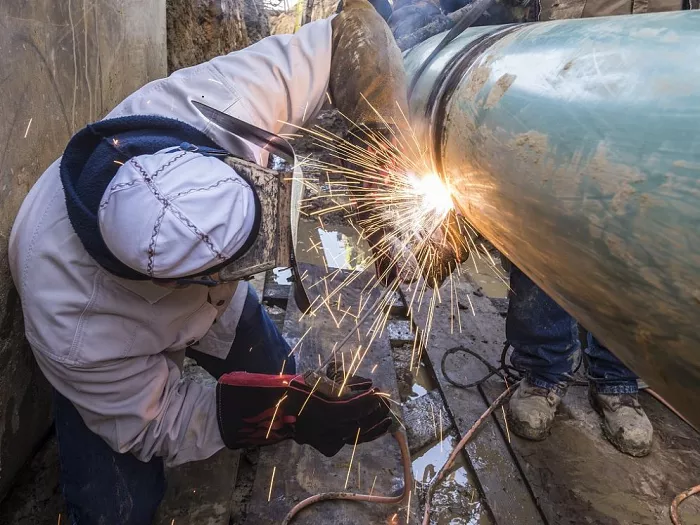
A critical factor in stainless steel stick welding is choosing the appropriate electrode. Electrodes such as E308L, E309L, and E316L are commonly used, depending on the type of stainless steel and the application's requirements. E308L electrodes, for instance, are optimal for welding 304 and 304L stainless steels, providing a balance of strength and ductility. These electrodes ensure a clean finish with robust mechanical properties, making them ideal for structures requiring both durability and aesthetics.
When it comes to expertise, controlling the heat input is paramount. Stainless steel's thermal conductivity is less than that of mild steel, meaning excessive heat can lead to warping or, worse, chromium carbide formation, which can compromise corrosion resistance. A lower amperage coupled with tight arc gaps helps maintain an optimal heat input, preserving the material's integrity.
Adjusting travel speed to ensure a consistent bead also enhances weld quality and minimizes post-weld cleanup.

Authoritativeness in stainless steel stick welding comes from understanding its applications across various industries. In sectors like food processing and pharmaceuticals, where cleanliness is paramount, stainless steel's hygienic properties are exploited to maintain sterile environments. Welding in such contexts requires not only precision but thorough post-weld cleaning to prevent contamination. Experienced welders utilize passivation – a process that restores the corrosion-resistant surface layer – to ensure longevity and adherence to industry standards.
stainless steel stick welding
Trustworthiness in executing stainless steel stick welding can be reinforced by adhering to stringent quality standards and certifications. Recognized credentials such as those from the American Welding Society (AWS) ensure that welding practices meet industry benchmarks for safety and quality. Welders should keep abreast of the latest techniques and technologies, attending workshops and earning qualifications that underscore their competency and commitment to excellence.
The adaptability of stainless steel stick welding is further evidenced in its field application. Unlike other methods that may suffer from limitations in windy or remote locations, stick welding remains reliable in adverse conditions. It doesn’t require gas shielding, which is particularly advantageous in outdoor settings where wind can disrupt gaseous shields in other welding methods. This resilience makes it indispensable for on-site repairs and constructions.
In conclusion, stainless steel stick welding is a dynamic process characterized by its adaptability, precision, and durability. Mastery of this technique demands continuous learning and adherence to quality standards, ensuring that welded structures stand the test of time. By understanding the principles and nuances of this welding approach, professionals can deliver reliable and aesthetically pleasing results, fostering trust and satisfaction among clients and industries alike.