Welding electrodes are indispensable tools in the realm of fusion welding, playing a crucial role in determining the quality and strength of the welded joint. This article delves into the intricacies of welding electrodes, showcasing insights and experiences that blend technical expertise, authoritative knowledge, and a commitment to safety and reliability.
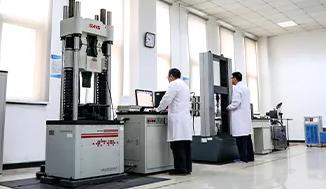
Selecting the right welding electrode is paramount to achieving optimal welding results. Types of electrodes, such as consumable and non-consumable, are designed to cater to different welding needs and environments. Consumable electrodes, used in techniques like Shielded Metal Arc Welding (SMAW), melt during the welding process to act as filler material. Non-consumable electrodes, typically employed in Tungsten Inert Gas (TIG) welding, do not melt and are used to sustain the arc while the external filler material is manually added. Understanding these distinctions is crucial for any welding project, as each type of electrode has its own application suited to specific materials and conditions.
Achieving superior weld quality necessitates more than merely selecting the appropriate electrode; it demands an understanding of the material composition and the environment in which the welding will occur.
Experienced welders know that electrode diameter and length influence the welding arc's stability and penetration. A correct match between the base material and the electrode composition, whether it's for carbon steel, stainless steel, or aluminum, ensures the weld's strength and durability.

Authoritative sources emphasize safety as a paramount concern in welding. Proper electrode storage is critical to maintaining their efficiency; electrodes must be kept in dry conditions to prevent moisture absorption, which can lead to hydrogen-induced cracking. Furthermore, adhering to stringent safety standards, such as utilizing appropriate personal protective equipment (PPE) and ensuring ventilation during welding operations, mitigates health risks associated with welding fumes and radiation.
welding electrode
Trust in welding electrodes is built through rigorous testing and adherence to industry standards. Reputable manufacturers subject their products to comprehensive quality control tests, including tensile strength and impact resistance assessments, to verify their reliability. Certifications from bodies like the American Welding Society (AWS) further assure users of the electrodes' compliance with industry benchmarks.
Investing in high-quality welding electrodes is a testament to a commitment to craftsmanship and safety. In-depth understanding of welding technology, paired with the practical knowledge of seasoned welders, can turn challenges into opportunities for innovation and excellence in weld crafting. Emphasizing education and continuous improvement, companies and professionals alike can advance their expertise while ensuring the integrity and longevity of their welds.
Ultimately, welding electrodes are more than tools—they are the foundation of creating structures that stand the test of time. Mastering their use not only enhances welding efficiency but also fosters a culture of safety and reliability in the industry. With this detailed exploration, professionals can confidently navigate the nuances of electrode selection and application, ensuring that every weld delivers the highest standards of quality and performance.