When working with welding steel rods electrodes, understanding their composition and application is vital for achieving optimal results. As a seasoned expert in metallurgy and welding, I bring to you a comprehensive guide rooted in deep technical knowledge and field experience.
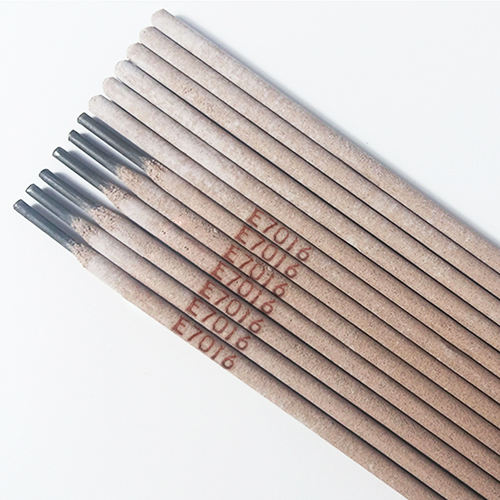
Selecting the right electrode for welding steel rods is pivotal in ensuring the strength and durability of your weld. The type of steel, its application, and environmental conditions influence this choice. Electrodes are generally coated metal rods that act as a filler to join two steel surfaces. They come in various compositions, each suitable for specific welding techniques and environments.
One major category of electrodes is the mild steel variant, often used for general-purpose applications due to its versatility. Experts recommend E6010 and E6011 electrodes for their deep penetration capabilities, especially when working in dirty, rust-laden, or painted environments. Their fast-freeze characteristics allow for vertical and overhead positions, which are challenging angles in welding projects.
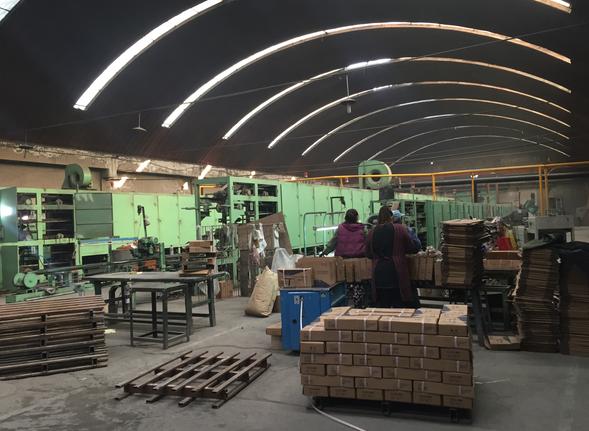
For projects demanding greater strength and reduced impurity sensitivity, low-hydrogen electrodes such as E7018 are preferred. These are engineered to minimize moisture absorption, thereby reducing hydrogen-induced cracking, a common problem in weld zones. Skilled welders appreciate the smooth arc and strong mechanical properties these electrodes offer.
High carbon steel presents another challenge due to its hardened nature. Specialized electrodes such as E8018 and E9018 provide the necessary strength and compatibility. These electrodes ensure the weld area is resilient to stress, minimizing the risk of fracture or wear over time.
Practical application extends beyond electrode selection. Welding parameters — including current, polarity, and voltage settings — are crucial. Amperage must be precisely calibrated to the electrode's size and the steel's thickness to avoid defects like splatter, porosity, and undercut. For instance, thicker steel requires higher amperage for deeper penetration, while thinner materials benefit from lower settings to prevent burn-through.
welding steel rods electrodes
In terms of technology adoption, advancements in digital welding machines offer precision unmatched by traditional models. Modern machines can store specific settings for different electrodes, allowing welders to quickly adapt to various tasks without manual recalibrations. This innovation improves the efficiency and consistency of welds, vital for high-stakes industries such as aerospace and infrastructure.
The role of preparation cannot be understated.
Cleanliness of the steel surface dictates the weld's integrity. Even the best electrodes can't compensate for poor surface preparation. Removing rust, dirt, and oil ensures a clean weld pool, crucial for fusion at a molecular level. Utilizing mechanical grinders or chemical solutions can help achieve the desired cleanliness.
Safety, a paramount consideration, must always accompany the technical aspects of using welding steel rods electrodes. Appropriate protective gear, including gloves, masks, and aprons, safeguard against high temperatures, UV radiation, and airborne particles. Additionally, proper ventilation in the workspace prevents the inhalation of harmful fumes.
It's also worth noting the ecological footprint. As the industry moves towards sustainability, there is increased interest in electrodes that produce minimal waste. Companies are exploring biodegradable fluxes and recycling programs to ensure that welding residues don't harm the environment.
In conclusion, mastering the use of welding steel rods electrodes requires a deep understanding of materials, equipment, and techniques. An authoritative approach integrates this knowledge with practical, hands-on experience, ensuring that every weld is both a testament to skill and a commitment to quality and safety. These insights not only foster trust among clients and colleagues but also contribute significantly to the advancement of welding technology and practice.