Wire MIG welding, a cornerstone technique in the manufacturing and construction industries, unfolds a realm of efficiency and precision. As a professional welder with over two decades of experience, the nuances of wire Metal Inert Gas (MIG) welding reveal the profound impact this technique has on productivity and quality.
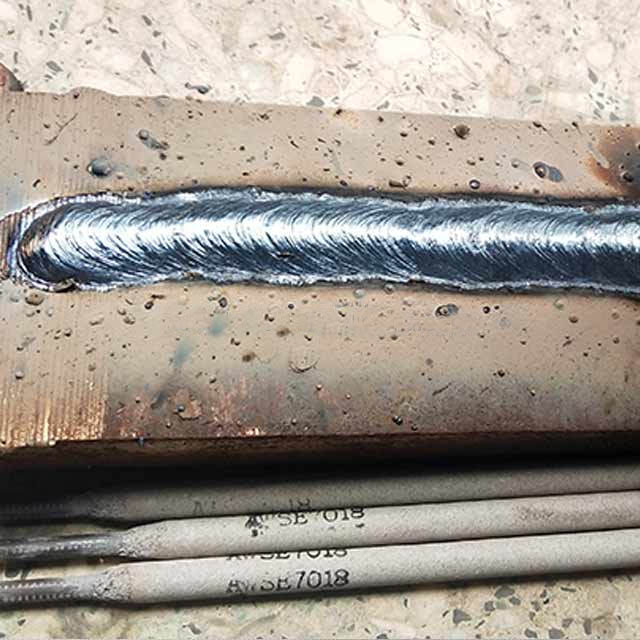
At its core,
wire MIG welding offers unmatched versatility. It seamlessly welds a variety of metals, from carbon steel and stainless steel to aluminum, with different thicknesses. This adaptability is largely attributed to the continuous wire feed system. Unlike traditional arc welding that uses electrodes, MIG welding utilizes a spool of wire fed through the nozzle, acting as both an electrode and filler material. This continuous feed ensures a consistent arc and, consequently, a uniform weld.
Experience dictates that the choice of wire is crucial. The selection ranges from solid wires to flux-cored wires, each with unique benefits. Solid wires, for example, offer cleaner welds with minimal spatter, ideal for precision tasks like automotive repairs. On the other hand, flux-cored wires allow for deeper penetration, making them perfect for thicker materials and outdoor projects where wind could interfere with shielding gases.
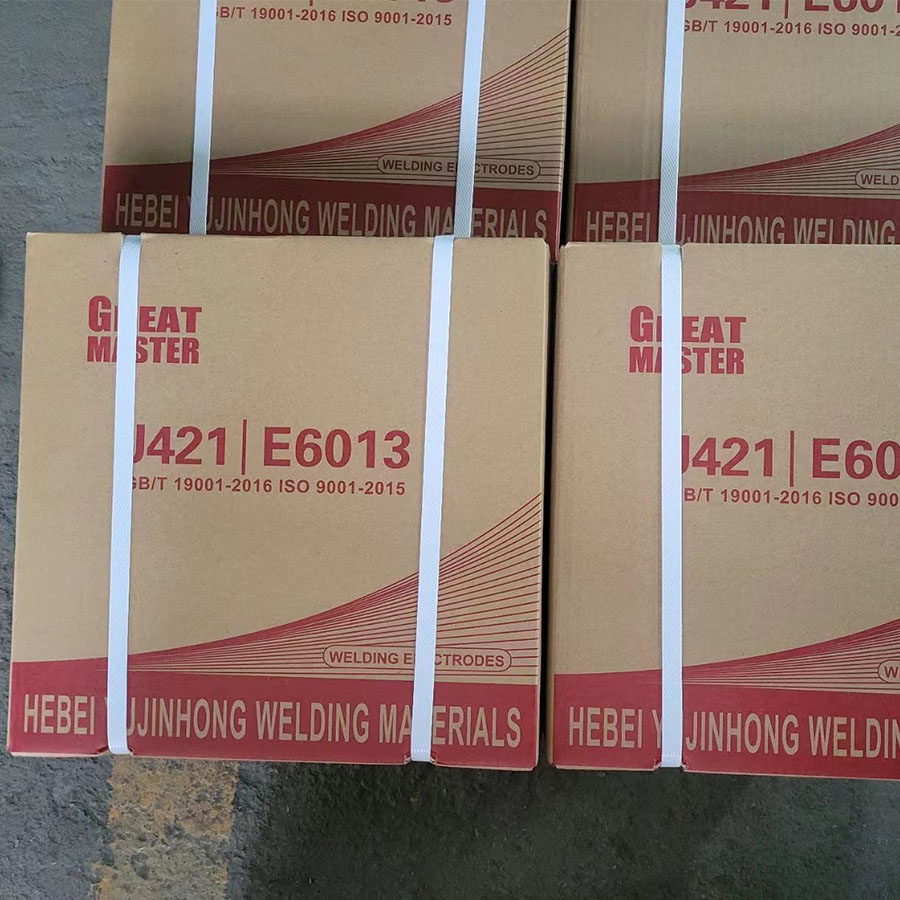
Expertise in wire MIG welding extends beyond the mere selection of wire types; it involves mastering the intricate balance of machine settings. Voltage, amperage, and feed rate must be meticulously adjusted to achieve the optimal weld. A low voltage setting might not provide adequate penetration, leading to weak joints, while excessive voltage can cause burn-through, compromising structural integrity. Similarly, incorrect feed rates lead to an erratic weld pool, resulting in aesthetic and functional drawbacks.
wire mig welding
Authoritativeness in MIG welding is demonstrated through proficiency in adapting to diverse working conditions. Master welders understand that environmental factors such as temperature, humidity, and even wind can significantly affect weld quality. Deploying shielding gases like argon or carbon dioxide mitigates oxidation, with expert welders tailoring gas mixtures to optimize weld strength and appearance.
Trustworthiness in the domain is underpinned by adherence to safety protocols and industry standards. Wire MIG welding is notoriously forgiving, often producing less smoke and fumes than stick welding. However, it remains imperative to implement comprehensive safety measures. Utilizing appropriate personal protective equipment (PPE), including helmets with auto-darkening lenses, gloves, and protective clothing, is non-negotiable. Furthermore, maintaining equipment in prime condition through regular checks ensures operational reliability and weld consistency.
The journey to mastering wire MIG welding is marked by continuous learning and adaptation. Innovations in MIG technology, such as pulsed MIG and synergic MIG, continue to redefine possibilities, enhancing control over the arc and deposition rate. Pulsed MIG, for example, allows welders to alternate between high and low peak currents, reducing spatter and improving weld quality. Such advancements underscore the dynamic nature of the field, demanding an ongoing commitment to skill enhancement.
In the ever-evolving landscape of welding, wire MIG welding stands as a testament to the blend of artistry and precision. Its application across various sectors underscores its importance as a fundamental skill for modern welders. As technology advances, those equipped with the knowledge and expertise in wire MIG welding will continue to thrive, reinforcing the relevance and indispensability of this technique in achieving superior structural integrity and aesthetic excellence.