For anyone involved in fabrication and metalwork, understanding the intricacies of welding is crucial, particularly when it comes to choosing the right welding wire. Among the most important components in this process is the welding wire flux core, an indispensable tool for many professionals and hobbyists alike. Tapping into years of expertise and industry authority, this article aims to arm you with the knowledge necessary to make informed decisions concerning this remarkable product.
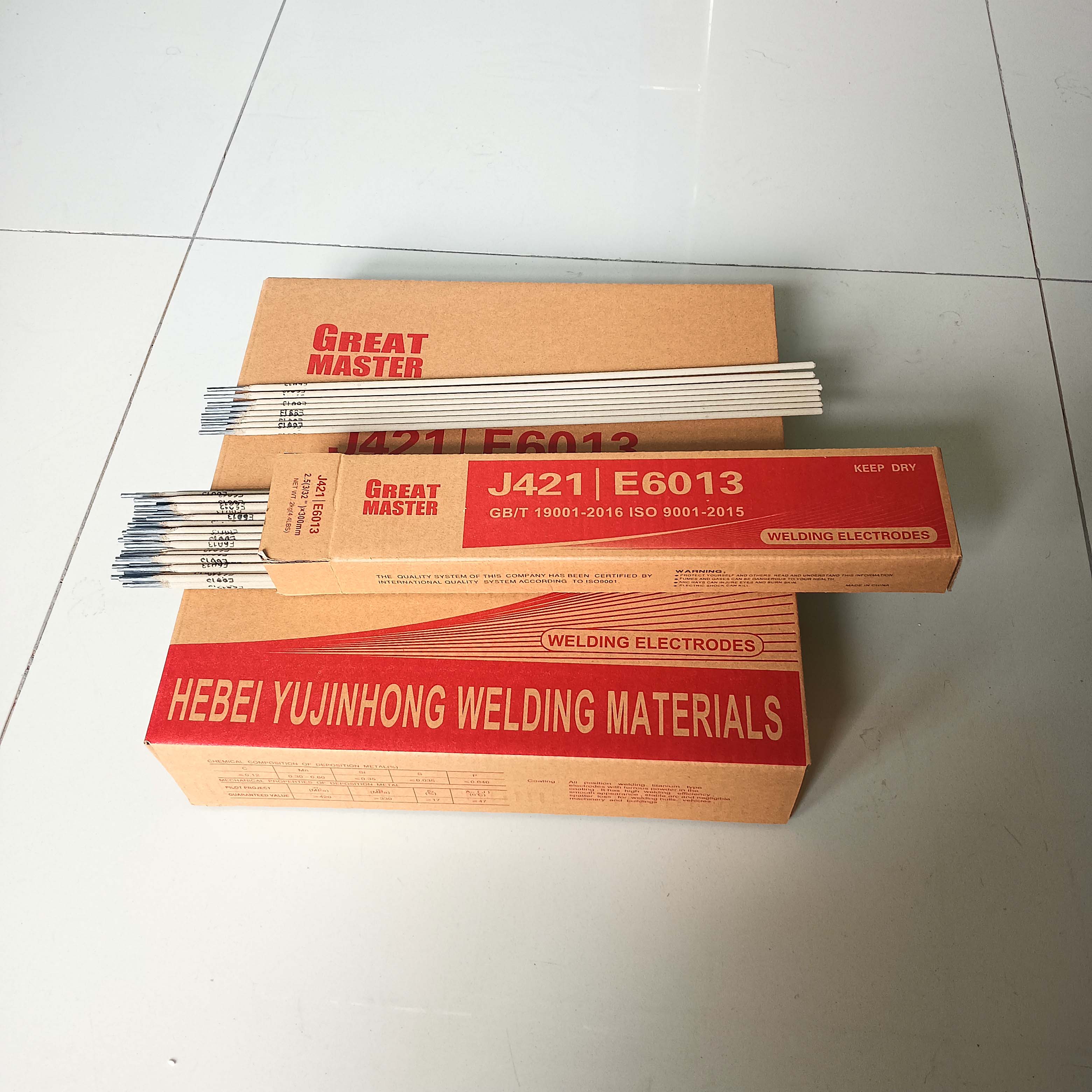
Flux-cored arc welding (FCAW) is celebrated for its versatility and efficiency, a favored technique especially in situations that demand robust and reliable results. The core feature of FCAW is its self-shielding wire, which eliminates the need for a separate shielding gas, making it especially advantageous in outdoor and drafty environments where gas-shielded welding might falter. This ability to perform effectively in challenging conditions underscores why flux core welding wire has earned its esteemed position among welding professionals.
Of notable importance is the experience one accumulates in selecting the appropriate flux core wire. With myriad options available, from E71T-11 suitable for general steel applications to specialized variations engineered for more exotic materials, the selection process is as nuanced as it is critical. Expertise in matching the right wire to the project not only optimizes the quality of the weld but also enhances productivity, reducing the likelihood of costly defects and rework.
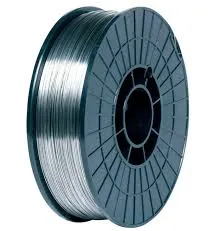
The flux core wire's remarkable welding capability lies in its innovative design. Comprising a tubular electrode filled with flux, this design allows for deeper penetration and lends itself to a smooth bead profile, reducing spatter and thus, cleaning time—a significant concern in large-scale production environments. Experienced welders appreciate that even with varying skill levels, flux core wire provides a forgiving nature; the flux creates a slag covering that shields the molten metal, contributing to a stronger, more durable weld joint.
welding wire flux core
From a technical standpoint, the expertise surrounding flux core wire extends to understanding its structure and properties. The flux within the wire not only acts as a shielding agent but also contributes alloying elements to the weld pool, enhancing the mechanical properties of the final product. Professionals in the field emphasize the significance of understanding these chemical contributions, as they can impact the weld’s strength, ductility, and corrosion resistance. This level of knowledge is particularly authoritative in industries where compliance with stringent standards is non-negotiable.
Trustworthiness in flux core welding comes with acknowledging and mitigating potential drawbacks. While the absence of a separate shielding gas simplifies the process, it does demand vigilance in controlling welding parameters to prevent excessive smoke and potential porosity in the weld bead. Therefore, maintaining a clean work environment and meticulously following manufacturer guidelines is indispensable maintenance of integrity in every welding task.
In conclusion, the welding wire flux core is an invaluable asset for completing high-quality welds with efficiency and reliability. Empowered by a comprehensive understanding of its features and applications, professionals can significantly enhance their welding projects. By leveraging experience and honed expertise, they can address complex welding challenges with a proven, authoritative approach that underscores trust and integrity within their field. Whether you’re a seasoned welder or an enthusiastic newcomer, mastering the nuances of flux core wire is a decisive step toward achieving welding excellence.