Selecting the right MIG welding wire can make a significant difference in achieving high-quality welds and ensuring efficiency in your projects. The best wire not only influences the weld's strength and appearance but also optimizes the welding process, enhancing productivity. When considering which MIG welding wire to use, several factors come into play, each requiring careful analysis to match the right product to the specific task requirements.
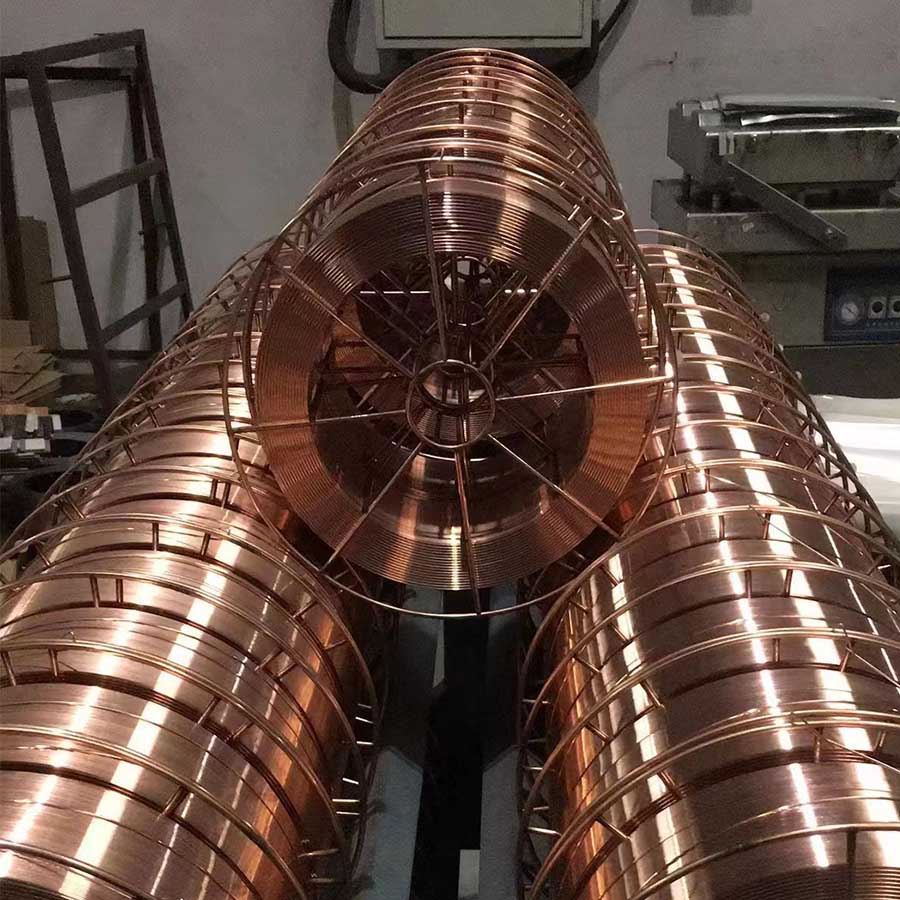
Experience across various welding projects underscores the importance of using a high-caliber MIG welding wire. Having personally worked with an array of wires, I can assert that factors such as wire composition, diameter, and intended use critically determine the welding outcome. For instance, when working with carbon steel, employing a copper-coated mild steel wire like the ER70S-6 enhances the welding process. This type of wire is renowned for its excellent strength, ductility, and smooth welding characteristics, making it a preferred choice for both novice and experienced welders.
Expertise in welding also dictates the necessity of understanding gas compatibility with your wire selection. Matching the MIG welding wire with an appropriate shielding gas is paramount. This not only optimizes the arc stability but also significantly reduces spatter, leading to cleaner welds. When using ER70S-6 wire, a mix of Argon and CO2 is often recommended for optimal results. The Argon-CO2 blend enhances the arc, providing a cleaner finish and improving penetration.
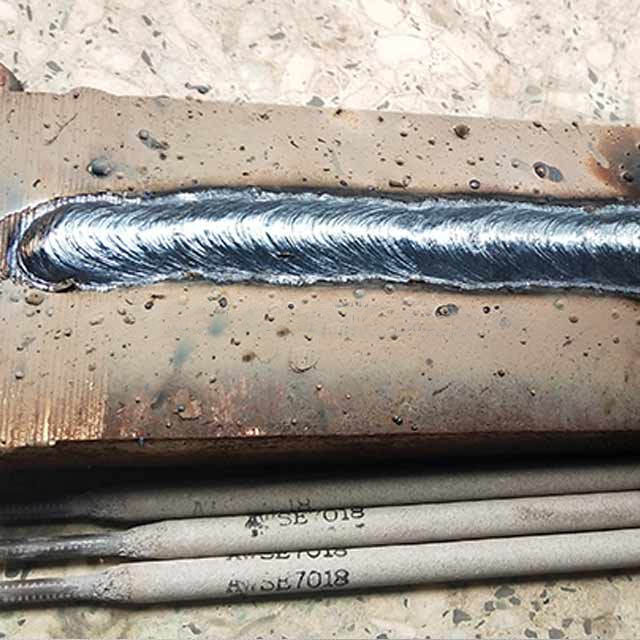
In terms of authoritativeness, the input from welding professionals and industry standards cannot be overlooked. Recognized bodies like the American Welding Society (AWS) provide classifications for wires which can help ensure that the selected wire meets the necessary quality standards for specific applications. For instance, choosing a wire that meets the specifications of AWS ER70S-6 indicates compliance with established criteria for tensile strength and chemical composition, which are critical for high-quality welds.
From a trustworthiness perspective, ensuring that the MIG welding wire is sourced from reputable manufacturers is crucial. Brands that have consistently demonstrated reliability and quality control, such as Lincoln Electric and Hobart, provide an assurance of durability and performance. Additionally, checking for customer reviews and feedback provides insight into real-world performance and potential issues, guiding towards making an informed decision.
best mig welding wire
Moreover, considering the wire diameter is essential for various thicknesses of the workpiece. Thin wires like 0.023 inches are suitable for light materials and automotive sheet metal, while thicker wires like 0.045 inches work well for heavy-duty projects. This selection influences the ease of use and the quality of the weld, and must align with the welder's capabilities and the material in question.
With the ongoing advancements in welding wire technology, some wires are specifically engineered to cater to the need for high-speed applications while others focus on reducing welding fumes for a cleaner workspace. Retailers increasingly offer flux-cored wires that provide versatility, usable in outdoor environments where wind might otherwise disturb the protective gas shield. These wires are an excellent solution for structural steel welding, offering deeper penetration and stable arc characteristics in adverse conditions.
The best choice of MIG welding wire is, therefore, multipronged. It considers personal competency, material thickness, and environmental factors. For those seeking premium quality, investing in reputable brands that offer extensive product ranges and customer support is invaluable. Aligning experience with manufacturer guidelines ensures the maintenance of best practices across all welding projects.
Ultimately, the right MIG welding wire enhances productivity, minimizes defect occurrence, and upholds safety standards. Its selection is as much about technical specification as it is the understanding of the welding environment and project demands. Consulting with welding experts, staying informed on industry trends, and continuously evaluating personal project outcomes helps in consistently selecting the best MIG wire for any specific task.