Understanding Mig Welding with Steel Wire A Comprehensive Overview
MIG (Metal Inert Gas) welding, also known as Gas Metal Arc Welding (GMAW), is a popular and versatile welding technique that utilizes a continuous wire feed as the electrode. When it comes to MIG welding steel wire, a unique combination of efficiency, precision, and adaptability sets it apart in the world of fabrication and construction.
Steel wire, the core element in MIG welding, serves as the filler material that joins two metal parts together. It is available in various diameters and compositions, each designed to cater to specific welding requirements and steel types. The percentage mentioned, mig steel wire, could potentially refer to the welding parameters, such as the wire feed speed or the percentage of shielding gas used during the process.
The choice of steel wire for MIG welding depends on factors like the thickness of the workpiece, the desired strength of the weld, and the environment in which the welding will take place. Mild steel wires are commonly used for general-purpose welding, while alloy steel wires offer enhanced strength and resistance to corrosion.
One key advantage of MIG welding with steel wire is its speed. The continuous wire feed allows for a rapid welding process, making it efficient for large-scale projects or where time is of the essence. Additionally, the use of shielding gas, usually a mixture of argon and carbon dioxide, protects the molten puddle from atmospheric contamination, ensuring a clean and high-quality weld Additionally, the use of shielding gas, usually a mixture of argon and carbon dioxide, protects the molten puddle from atmospheric contamination, ensuring a clean and high-quality weld
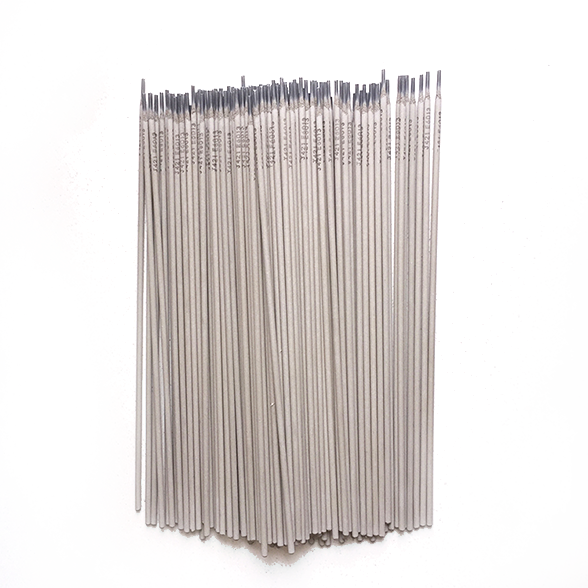
Additionally, the use of shielding gas, usually a mixture of argon and carbon dioxide, protects the molten puddle from atmospheric contamination, ensuring a clean and high-quality weld Additionally, the use of shielding gas, usually a mixture of argon and carbon dioxide, protects the molten puddle from atmospheric contamination, ensuring a clean and high-quality weld
mig steel wire.
The welding parameters, including the mig steel wire settings, are crucial for optimal results. Adjustments in wire feed speed, voltage, and welding speed can significantly influence the penetration depth, bead appearance, and overall weld quality. Proper selection and control of these variables ensure a strong, visually appealing, and structurally sound weld.
MIG welding with steel wire also offers the flexibility to switch between different positions, such as flat, vertical, and overhead, making it suitable for a wide range of applications, from automotive repairs to construction projects.
In conclusion, MIG welding with steel wire is a powerful tool in the hands of a skilled welder. Its efficiency, versatility, and adaptability make it a go-to method for many industries. Understanding the mig steel wire parameters and selecting the right steel wire for the job is essential for achieving the best possible welding results. With careful attention to detail and proper technique, MIG welding with steel wire can deliver outstanding performance and durability in any welding project.