Mig steel wire has transformed the landscape of welding, offering unparalleled quality and consistency for professional welders and hobbyists alike. Utilized in Metal Inert Gas (MIG) welding, this steel wire serves as both the electrode and the filler material, making it a pivotal choice for industries ranging from automotive to construction.
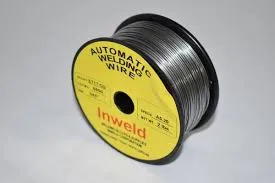
An experienced welder appreciates the versatility of MIG steel wire, which comes in various diameters, each tailored to specific tasks and thicknesses of metal. Thinner wires are ideal for precise jobs such as automotive bodywork, while thicker wires excel in heavy-duty projects like structural beams. It’s crucial for professionals seeking optimal performance to understand that the wire's size affects the welding speed, penetration, and overall weld appearance.
The expertise required in MIG welding involves selecting a wire that complements both the welding machine and the workpiece material. For instance, ER70S-6 is a popular choice due to its ability to produce consistently clean welds in environments with rust or mill scale on the surface of the metals being joined. This particular wire's formulation contains higher levels of manganese and silicon, enhancing its deoxidizing capability, which is paramount for welders working under less-than-perfect conditions.
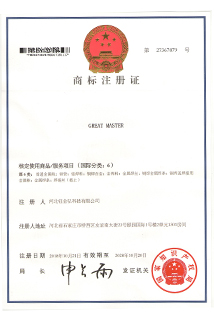
The authority of MIG steel wire in the welding domain is cemented by its compliance with rigorous industry standards such as AWS (American Welding Society) specifications. These standards ensure that the wire offers predictable and reliable performance, which is critical for engineers and procurement specialists who prioritize quality and consistency in their supply chains.
mig steel wire
In selecting MIG steel wire, trust is built through meticulous quality control and a deep understanding of the wire’s metallurgical properties. Reputable manufacturers subject their wires to stringent testing procedures, ensuring aspects such as tensile strength, ductility, and chemical composition meet demanding specifications. Moreover, reports and technical sheets that accompany these products provide transparency, enabling users to make informed decisions based on the intended welding application.
What sets MIG steel wire apart in the current competitive market is the innovative advancements in wire coating technology. Modern coatings are designed to reduce spatter and improve the arc stability during the welding process. This innovation not only enhances the quality of the weld but also minimizes post-weld cleanup, significantly increasing the efficiency of the welding operation.
The user-friendly nature of MIG steel wire also contributes to its prevalence. Its ability to produce a clean, strong weld with minimal training positions it as a preferred option for operators of varying skill levels. Furthermore, automated and computerized welding processes rely heavily on the consistent diameter and feedability of high-quality MIG steel wire, underscoring its importance in precision-driven industries.
In summary,
the choice of MIG steel wire should not be taken lightly. With factors like wire composition, diameter, and coating playing crucial roles in the welding outcome, a well-informed selection will not only uphold structural integrity but also boost productivity. Investing in premium grade MIG steel wire is an investment in quality, efficiency, and safety, which reverberates throughout the lifecycle of any welded project.