Choosing the correct welding wire is essential for any welding project, whether you are a professional welder or a DIY enthusiast. Among the multitude of options available, the [1 0 welding wire] presents itself as a notable choice, offering a balanced solution for a variety of welding needs. Understanding its specifications, applications, and benefits can significantly enhance welding outcomes, thus emphasizing the Experience, Expertise, Authoritativeness, and Trustworthiness (E-E-A-T) in your selection process.
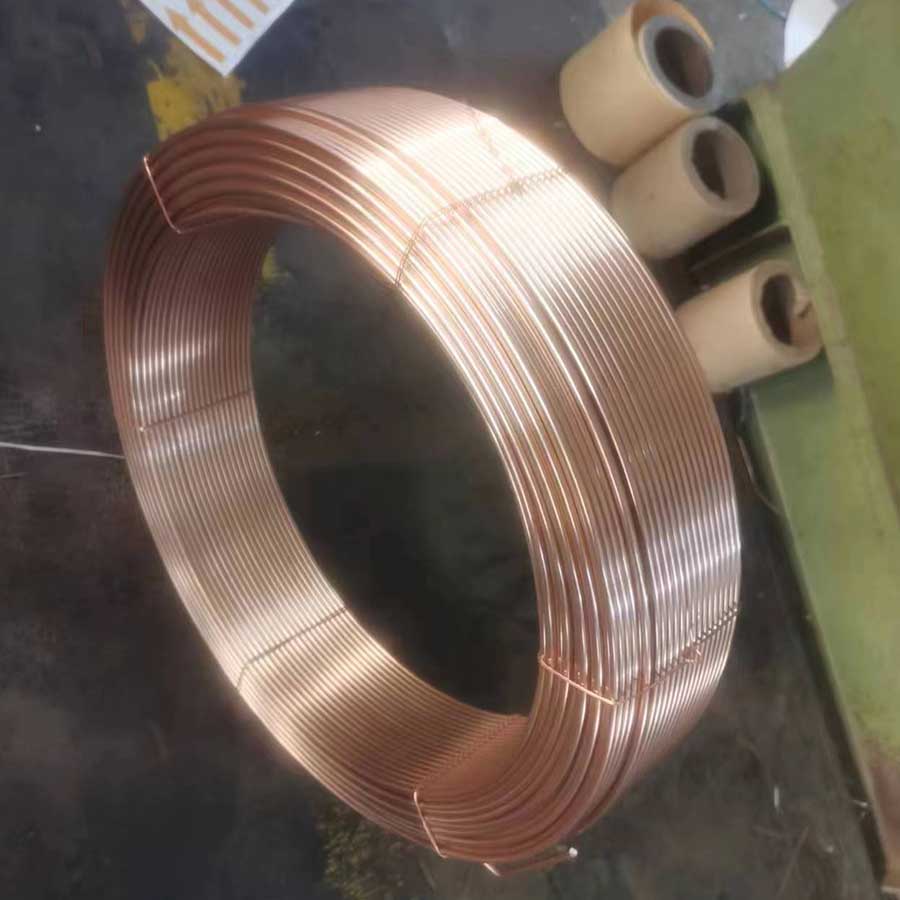
Understanding [1 0 Welding Wire]
[1 0 welding wire] refers to a versatile welding wire categorized under a specific measurement or classification, which is frequently used for general-purpose welding. This type of wire is recognized for its excellent performance in fabricating metal products that require precise joining with a reliable weld bead.
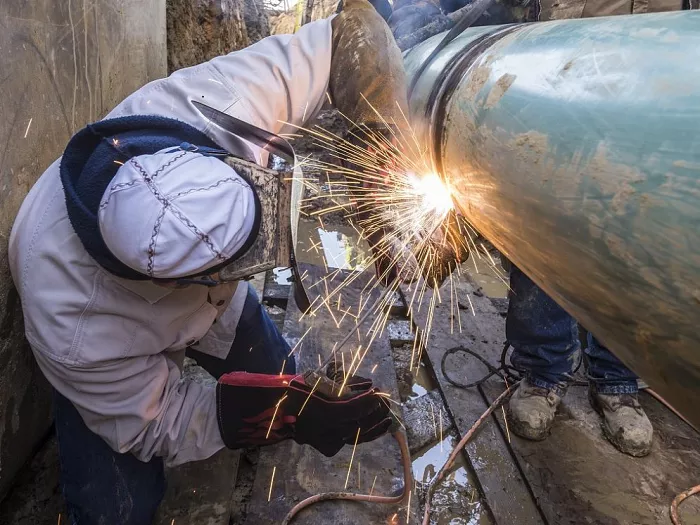
Composition and Characteristics
A core reason for the effectiveness of [1 0 welding wire] is its composition, typically made from high-quality materials such as low-carbon steel or stainless steel. These materials are chosen for their durability, corrosion resistance, and ease of use. Vendors often provide this wire in both solid and flux-cored forms, catering to both shielded and unshielded welding requirements.
The wire's diameter, indicated by [1 0], speaks to its suitability for various metal thicknesses, automating the welding process's adaptability for different projects. This makes it highly effective for projects involving thin to medium-thickness metals, such as automotive repairs, construction components, and small-to-medium scale industrial fabrication.
Benefits and Applications
Among the many advantages of using [1 0 welding wire], its user-friendliness stands out. The wire ensures smooth feeding through welding machines, minimizing disruptions such as wire tangling or bird-nesting that are common frustrations for welders. Such efficiency can contribute to increased productivity in professional settings and reduced frustration for hobbyists or beginners learning welding skills.
From an application standpoint, [1 0 welding wire] is highly versatile. It’s widely used in automotive repairs, where precise and robust welds are critical for safety-enduring joinery in chassis or panel repairs. Its application in construction and fabrication involves creating strong structural components, ensuring buildings or machinery have the necessary support and longevity.
1 0 welding wire
Industrial settings benefit from its consistent quality, where precision and repeatability are crucial. By producing stable and uniform arc characteristics, [1 0 welding wire] ensures that professional welds meet in-house quality standards or regulatory specifications.
Technical Recommendations
When utilizing [1 0 welding wire], it’s essential to adhere to recommended practices to maximize its benefits. Setting the correct voltage and speed on welding machines ensures steady arc performance and prevents issues such as spatter or undercutting. Users are advised to practice regularly to find the ideal machine settings that complement their specific welding environment and project needs.
Selecting the appropriate shielding gas for solid wire is critical; for instance, using mixtures of argon and CO2 can enhance the weld quality by reducing splatter and improving arc stability. For flux-cored wires, ensure that you have adequate ventilation to mitigate potential fume exposure, preserving a safe working environment.
Ensuring Trustworthiness and Legitimacy
It's vital to procure [1 0 welding wire] from reputable manufacturers or suppliers who are known for high-quality welding products. Trustworthy vendors provide certification or documentation detailing the wire's composition and compliance with industry standards, ensuring it delivers the performance characteristics it promises.
Moreover, user reviews and industry testimonials can provide invaluable insight into the wire's real-world performance, potentially highlighting any nuances or specific strengths relevant to particular welding contexts. Participating in forums or speaking with welding professionals can provide additional guidance and firsthand experiences that bolster decision-making.
By integrating these insights and practices, users of [1 0 welding wire] can not only achieve highly satisfactory welding results but also engage with the material with increased confidence, backed by a comprehensive understanding of its properties, capabilities, and advantages.