In the realm of metal fabrication, choosing the right welding materials is pivotal for success and efficiency. One such essential material is flux cored MIG wire, a consumable that has revolutionized the welding process. It is paramount to delve into the intricacies of this wire to understand how its attributes cater to industry needs.

Flux cored MIG wire, often employed in environments where high productivity is a requirement, serves as an invaluable tool due to its unique construction. Unlike traditional solid wires, this wire consists of a tubular design filled with flux. This configuration not only enhances the metal deposition rate but also contributes to reduced welding time and improved overall project efficiency. For welders seeking heightened productivity without compromising quality, this type of wire provides the ideal solution.
When it comes to welding through slightly oxidized or contaminated surfaces, flux cored MIG wire truly shines. The flux core has a significant role in safeguarding against the ill effects of surface impurities, ensuring a stable arc and improving penetration. This trait makes it an excellent choice for fieldwork, where surface preparation might not always be optimal, thus granting welders the flexibility to work effectively in diverse and demanding conditions.
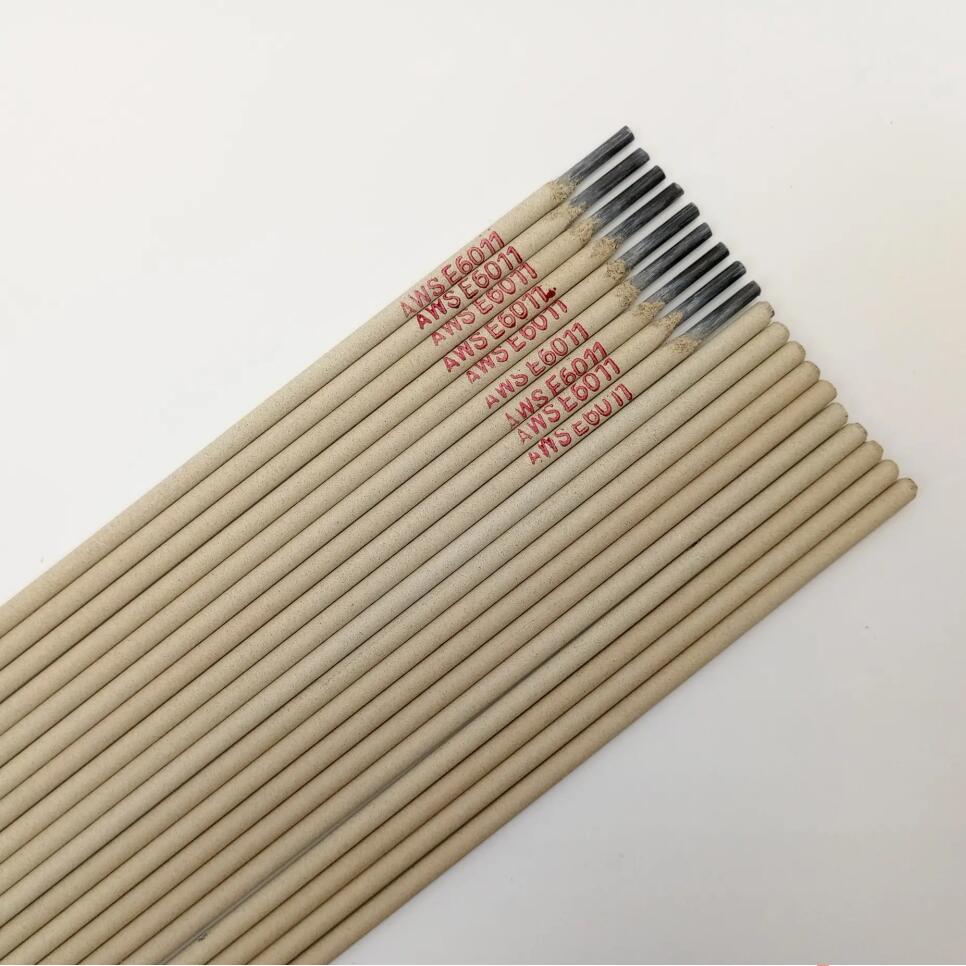
The expertise required to leverage the full potential of flux cored MIG wire cannot be overstated. Professional welders appreciate how the wire accommodates a variety of positions, excelling in overhead, vertical, and horizontal welding scenarios. This versatility is particularly important for complex structures and assemblies. The ease of use coupled with consistent performance underscores its suitability for both seasoned professionals and those newer to the craft, enabling a higher skill cap while providing a gentler learning curve.
flux cored mig wire
As an authority in welding, recognizing and recommending the appropriate specifications of flux cored MIG wire can elevate one's standing within the community. Factors such as wire diameter, composition, and current requirements must be evaluated to ensure compatibility with specific projects. Such attention to detail demonstrates a keen understanding of welding dynamics, empowering fabricators to innovate and achieve superior results.
Trustworthiness in discussing flux cored MIG wire comes from hands-on experience and a thorough grasp of safety protocols. Professionals know that managing the increased fumes and spatter, characteristic of flux cored welding, necessitates proper ventilation and protective gear. Abiding by these safety measures not only protects the workforce but also maintains compliance with occupational safety standards, fortifying the trust clients and colleagues place in a welder's expertise.
The landscape of welding continues to evolve, yet flux cored MIG wire remains a trusted ally for those in the industry. It combines innovation and practicality, delivering performance that meets the high standards expected in modern fabrication. By integrating this advanced wire into their workflow, professionals can ensure precision, reliability, and optimum productivity, further cementing their reputation as meticulous and reliable craftsmen in a competitive market.