Understanding the nuances of welding is essential for professionals seeking to elevate their craft to a level that guarantees both precision and durability. One tool that plays a pivotal role in this domain is the MIG flux core welding wire. This type of welding wire has revolutionized the process, enhancing flexibility and offering superior outcomes in various welding projects.
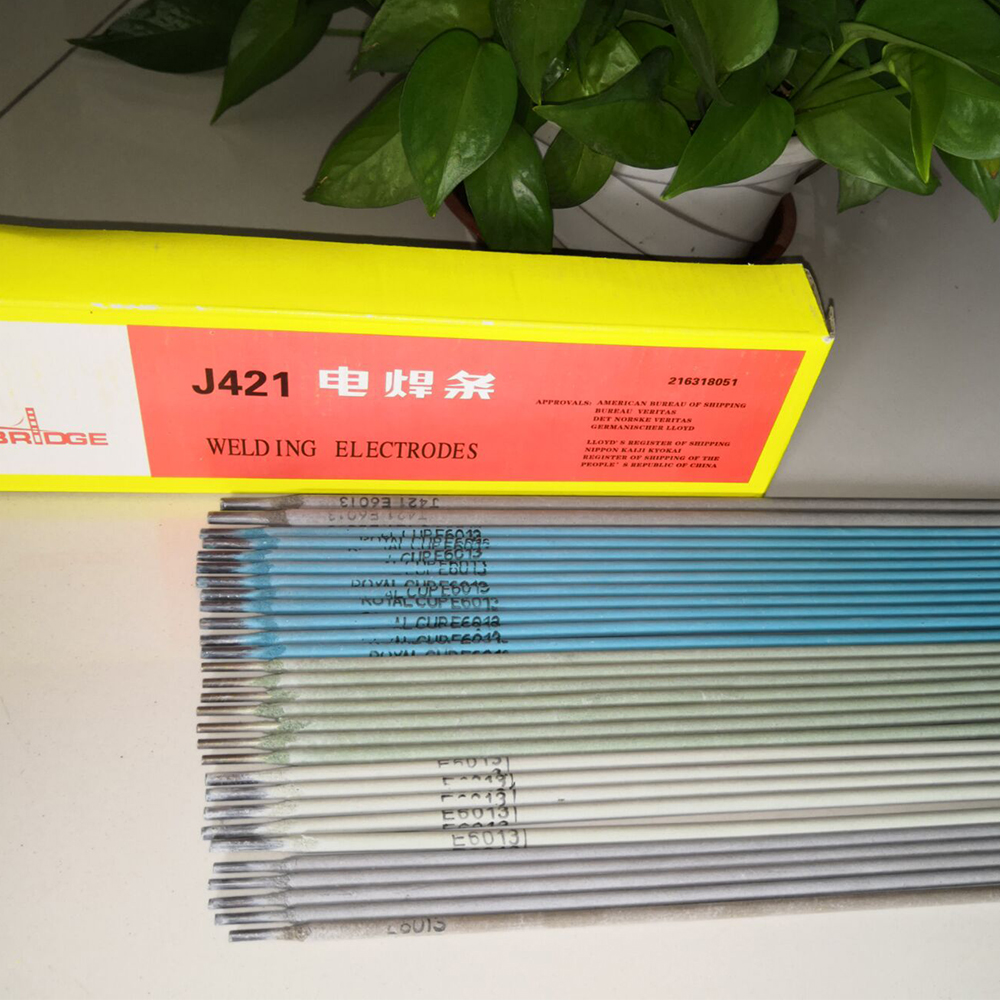
MIG flux core welding wire is a hybrid between MIG (Metal Inert Gas) and FCAW (Flux-Cored Arc Welding) processes. This unique combination takes the best of both worlds the simplicity and speed of MIG welding along with the strength and versatility of flux-cored welding. This welding wire consists of a hollow tube filled with flux, encased in metal. Unlike solid MIG wires, the flux within provides additional shielding from atmospheric contaminants, which is crucial for maintaining weld integrity and strength.
For any welder aiming to achieve exceptional results, the choice of welding wire is paramount.
MIG flux core welding wire offers advantages that cannot be overlooked. One of the key benefits is its ability to perform exceptionally well in windy or outdoor conditions without the need for external shielding gas. This makes it an ideal choice for projects such as construction or agricultural repairs where portability and flexibility are necessary.
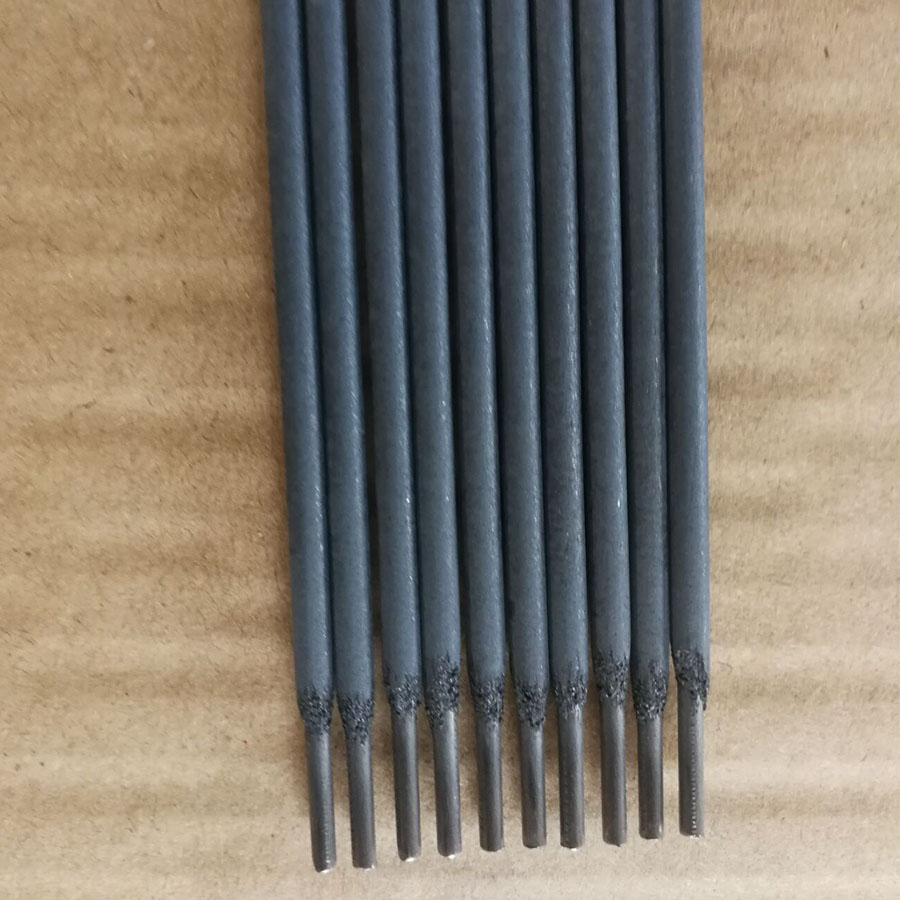
From an experiential perspective, these wires provide a smoother and more forgiving arc, reducing the likelihood of weld defects like spatter or porosity. This is particularly beneficial when welding thicker or dirty materials, which are typically challenging even for experienced welders. The flux core enhances penetration capability, allowing the welder to work with thicker materials without extensive edge preparation.
mig flux core welding wire
Expert welders consistently emphasize the importance of matching the wire type with their specific project requirements. MIG flux core welding wire is available in a variety of alloys and thicknesses, each designed to cater to different materials and applications. For instance, wires made from stainless steel are optimal for work involving high-corrosion environments, while those made from mild steel are suitable for general-purpose welding.
When discussing the authoritativeness and trustworthiness of this product, it is essential to highlight the standards and certifications governing its use. Most quality welding wires comply with the standards set by the American Welding Society (AWS). These standards ensure that the wire meets the specific mechanical and chemical properties required for comprehensive applications, thereby instilling confidence in its performance.
Although MIG flux core welding has simplified many aspects of the welding process, it still requires an understanding of proper techniques and settings. Achieving the right balance between wire feed speed, voltage, and travel speed is crucial to exploit the full potential of this welding wire. Therefore, investing time in practice and possibly consulting instructional resources ensures mastery over the technique and optimal results.
In summary, the MIG flux core welding wire stands as a testament to innovation in the welding field. Its unmatched versatility, combined with its robust performance in less-than-ideal conditions, makes it a commendable choice for both novice and professional welders. Moreover, its alignment with industry standards further establishes its credibility, making it a trustworthy component in any welder's toolkit. By understanding and leveraging the capabilities of this sophisticated welding wire, individuals can enhance their craftsmanship and assure the long-term durability of their projects.